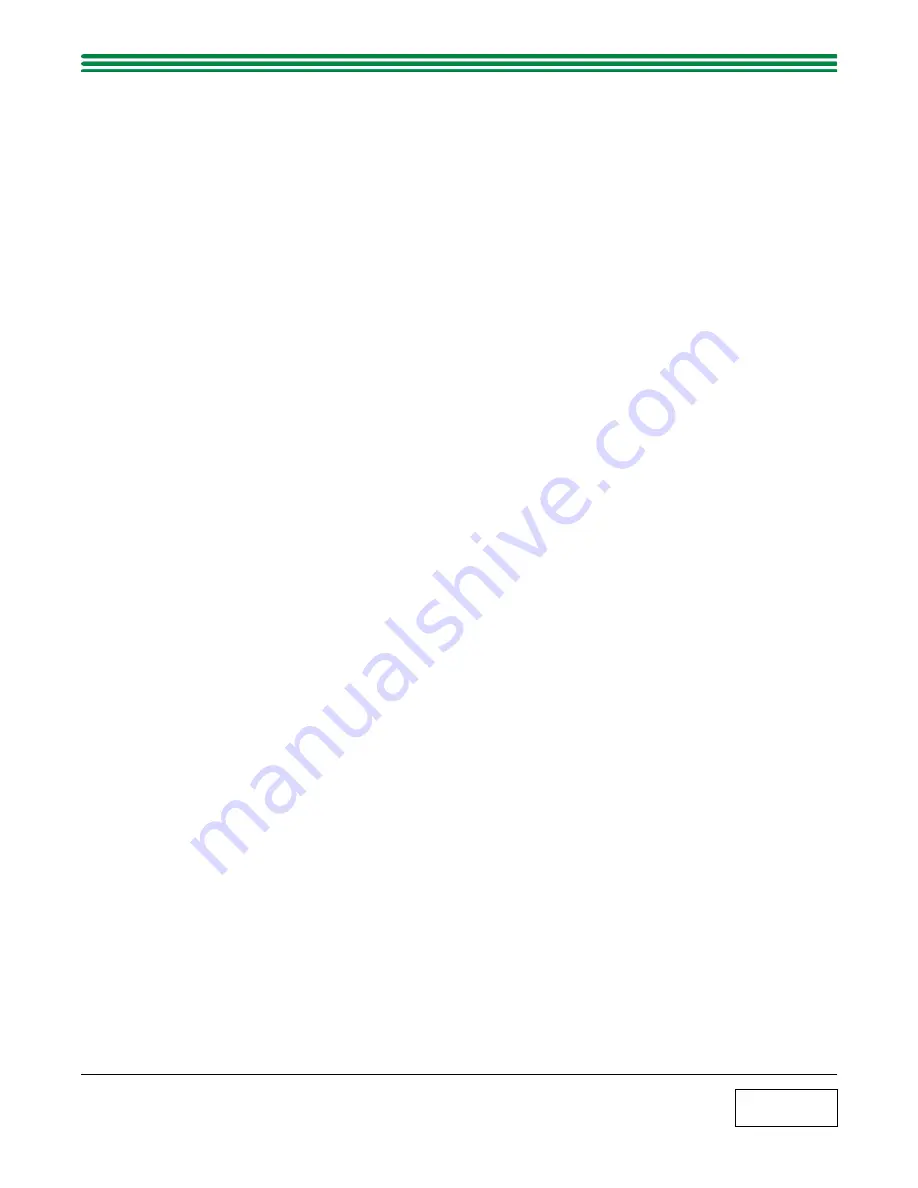
AFR200 Series, Product User Guide
This document is subject to change without notice.
Caution: None of GAC products are flight certified controls including this item
Copyright © 2010, Governors America Corp., All Rights Reserved
10
PUG4144 D
3.5 Communication & Configuration
The controller has both RS232 and CANbus communication capability. Communication with SmartVU is done
over RS232 using a serial port or USB to serial converter. The CANbus is typically used to communicate with
other devices such as J1939 capable display devices, and data readers.
3.5.1 SmartVU Configuration Software
The AFR is programmed and calibrated using GAC’s SmartVU configuration software. The SmartVU interface
allows the user the ability to customize engine performance real-time, monitor data, view diagnostic information,
and store configurations. This information is covered in greater detail in later sections.
3.5.2 Diagnostics
The AFR has the ability to diagnose and indicate numerous failure conditions as well as store an extensive fault
history. This information is readily indicated by the Malfunction Indicator Lamp (MIL) output or by the status
indication LEDs on the AFR itself. For more detailed diagnostics the SmartVU diagnostic interface provides a
host of information including engine data, speed vs. load mapping and OBDII P-codes and GAC G-codes. This
information is covered in greater detail in later sections.
3.6 Optional Sensors
The following section covers the optional sensors which are available for interface with the AFR. Note that the
post-catalytic oxygen and the exhaust gas temperature sensor capability are only available with certain variations
of the AFR whereas the engine oil pressure and coolant temperature sensor inputs are available with all
variations.
3.6.1 Post-Catalytic Oxygen (O2) Sensor
An additional narrow-band stoichiometric oxygen sensor can be mounted in or behind the catalytic converter to
monitor converter efficiency. These are referred to as the downstream O2 sensors. A downstream oxygen sensor
works exactly the same as an upstream O2 sensor in the exhaust manifold. If the converter is doing its job and is
reducing the pollutants in the exhaust, the downstream oxygen sensor should show little activity (few lean-to-rich
transitions, which are also called "cross-counts"). The sensor's voltage reading should also be fairly steady (not
changing up or down), and average 0.45 volts or higher. If the signal from the downstream oxygen sensor starts
to mirror that from the upstream oxygen sensor(s), it means converter efficiency has dropped off and the
converter isn't cleaning up the pollutants in the exhaust.
3.6.2 Engine Oil Pressure (EOP) Sensor
The engine oil pressure sensor is used by the AFR in order to diagnose and determine whether or not a low oil
pressure condition exists during engine operation. The setpoint is entered via SmartVU and the AFR will then
shutdown the engine in the event of a failure.
3.6.3 Engine Coolant Temperature (ECT) Sensor
The engine coolant temperature sensor is used by the AFR to gauge engine temperature and alert the operator or
shutdown the engine in the event of an over temperature condition. The GAC offered coolant temperature sensor
is a thermistor where the sensors resistance varies inversely to temperature changes. This number can be
displayed on a scan tool, and may also be used by the instrument panel cluster or driver information center to
display the temperature reading of the coolant.