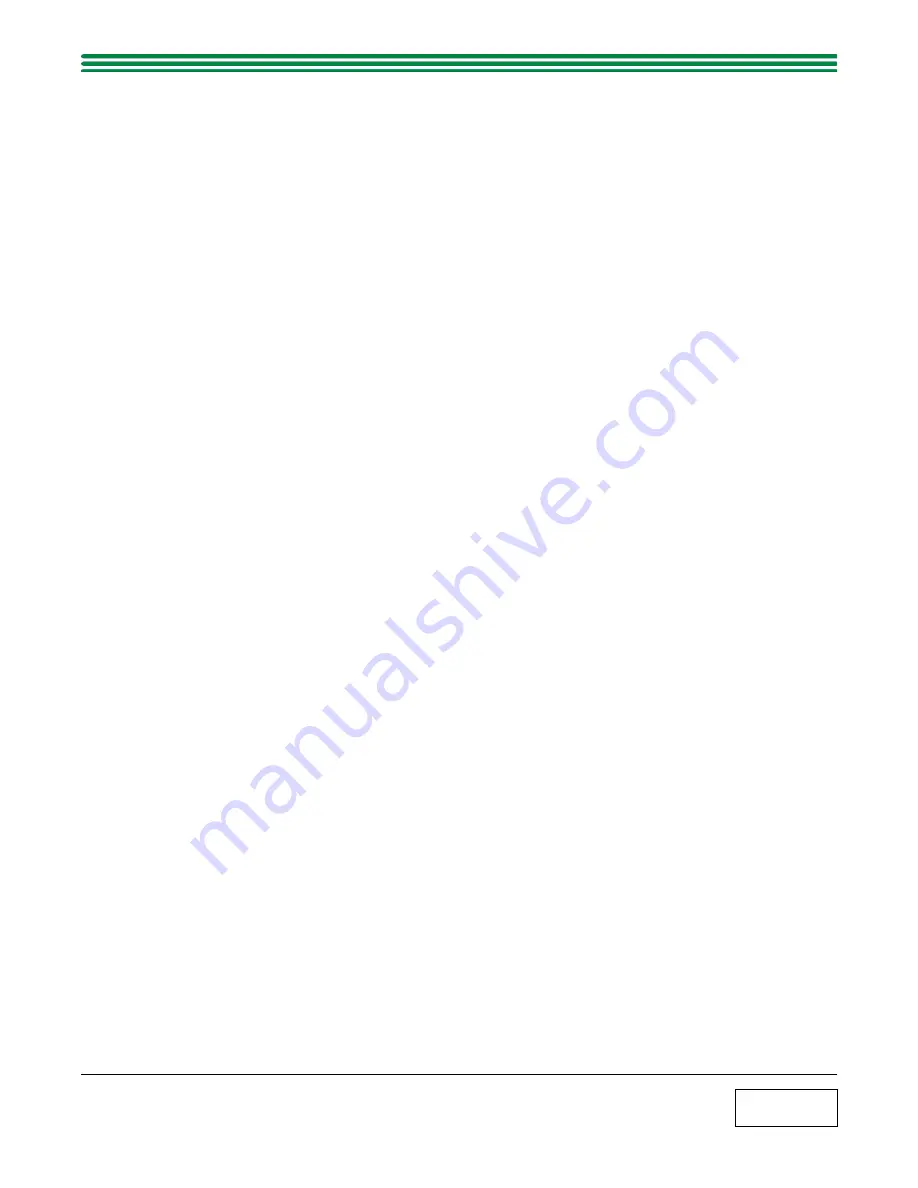
AFR200 Series, Product User Guide
This document is subject to change without notice.
Caution: None of GAC products are flight certified controls including this item
Copyright © 2010, Governors America Corp., All Rights Reserved
9
PUG4144 D
opened and vacuum drops. The Manifold Absolute Pressure (MAP) sensor is a key sensor because it is used to
determine engine load. It is optional if none of the multi-PID functionality is desired.
3.2.3 Engine Speed Sensor
Engine speed information for the speed governing algorithm is usually received from a magnetic speed sensor.
The speed sensor is typically mounted in close proximity to an engine driven ferrous gear, usually the engine
flywheel ring gear. As the teeth of the gear pass the magnetic sensor, a signal is generated which is proportional
to engine speed.
Other speed sensing devices may be used, provided the generated frequency is proportional to the engine speed
and meets the voltage and frequency range specification. The AFR will begin to govern the engine once the RPM
reaches the crank termination set point.
3.3 Speed Control and Protection
The proprietary multiple PID governor control system provides fast and accurate control (+/- 0.25%) of the
engines speed to any dynamic load changes in isochronous or droop operation. When connected to a throttle
body actuator and supplied with a magnetic speed sensor signal the governor portion will direct the engine to the
desired speed setting.
The governor has several built in configurable features: three fixed and variable speed with correlating droop
settings; engine overspeed shutdown protection; speed ramping from idle to operation speed; and starting fuel
control for lower engine exhaust emissions. The three fixed governed speeds and one variable governed speed
are all selectable through two discrete inputs. An additional accessory input is available for connecting to GAC
load sharing modules (generator set option).
The AFR will protect the engine by shutting it down in the event of an engine overspeed, low oil pressure, high
coolant temperature, or high exhaust temperature. These thresholds are all customizable using SmartVU.
Additionally the controller is designed to withstand reverse polarity connections, transient voltage spikes, and
engine speed data loss in the event of a failure.
3.3.1 Auxiliary (AUX) Speed Trim Input
The auxiliary input signal is intended to provide a speed trim input for the engine to synchronize with another
power source / generator. The aux input range is 0-10 volts with a nominal value of 5 VDC. When enabled, the
input tells the governor what speed to set the engine to.
The AFR is configured for a negative slope meaning that a value of 10V will be the lowest engine speed and 0V
will be the highest engine speed. The default window for engine speed adjustment is + / - 10% from the fixed
speed setting.
3.4 Fueling States
During the engine cranking cycle, starting fuel can be adjusted from an almost closed, to a nearly full fuel position.
Once the engine has started, the speed control point is determined by the idle speed set point and the speed
ramping algorithm. The speed ramping functions adjust the engines speed acceleration and deceleration and is
fully customizable by SmartVU.
After engine speed ramping has been completed, the engine will be at its governed operating speed. When at the
desired governed engine speed, the actuator will be energized with sufficient current to maintain the desired
engine speed in a closed loop speed control, independent of engine load (isochronous operation).