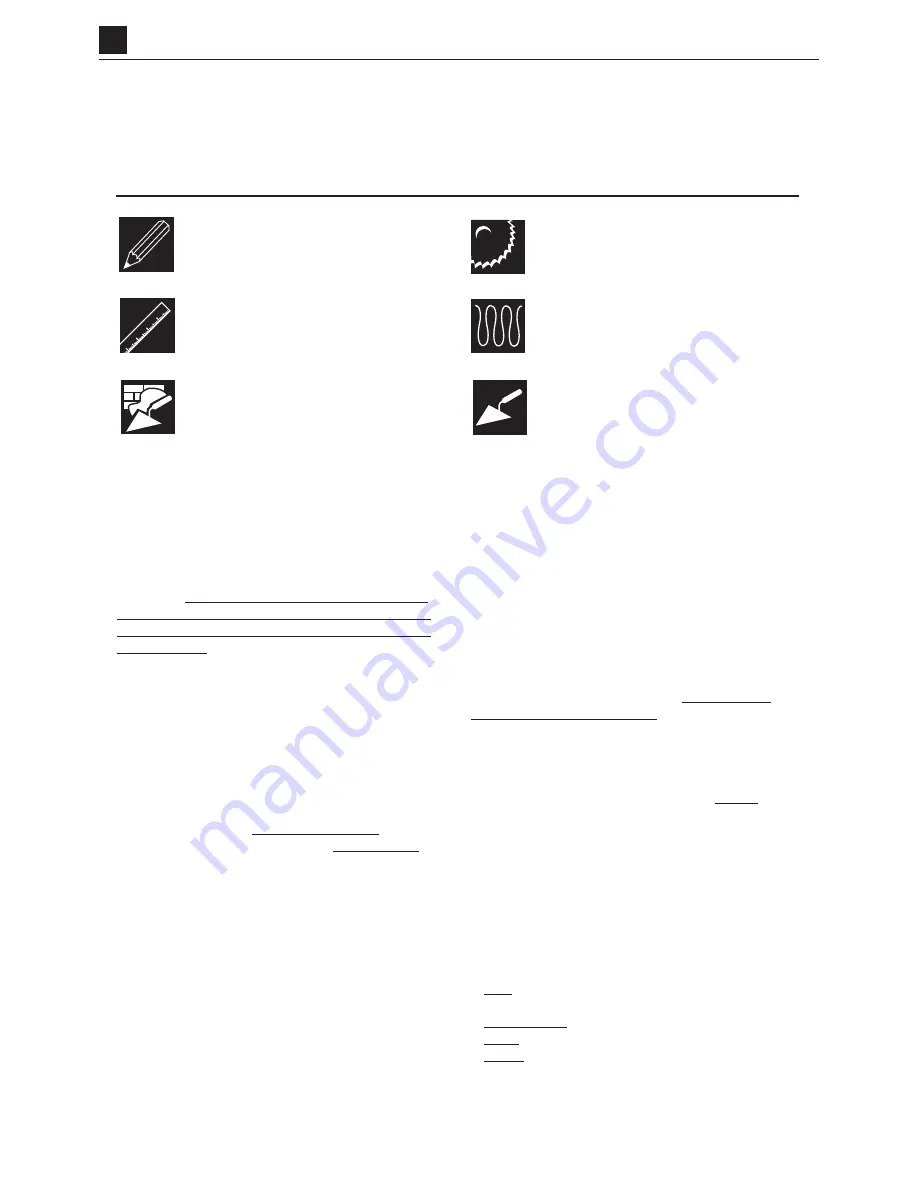
GABRIEL KERAMIK AB
3
Foreword
General
Gabriel tiled stoves consist of prefabricated modules,
cast from fireproof material. The stoves should be
built by an approved tradesman.
A building permit is needed when building a new
tiled stove. Before starting to fire, the tiled stove has
to be inspected by the Building Control Officer, (see
local and national regulations regarding installation
of fire places).
Distance and measurements
As to the following pictures in this manual you place
the first module 50 mm from a combustible wall. A
non-combustible hearth shall be placed on the floor
in front of the stove (for size, see local regulations).
A 300 mm free space is needed in front of the soot
holes on each side of the stove. The hole in the
base for inlet air to the convection heat must not be
blocked. The manual’s control measurements (page 5)
are very important, while the other measurements
should be seen as a guide during the assembly.
Support
The foundation and floor support of the stove has to
be approved before assembly.
The weight of the stove is between 1300-1800 kg
depending on the model and flue connection.
Therefore the foundation requires sufficient bearing
capacity and shall be checked and approved in
accordance with the building permit, (consult your
local building authorities).
Thickness of joints
The joints between the modules are approx.10 mm.
Use a suitable wet brush for neat, tight joints.
Explanation of symbols/foreword
Marking with a pen
Important positions, areas for sawing and
placing of mortar are marked with a pen.
Control measurement
Shows important measurements during
assembly.
Trowel
Shows where the clay mortar is placed.
Rendered areas
Shows the areas that shall be rendered
with clay mortar.
Saw
Shows where the prefabricated modules
should be sawn.
Insulation
Shows where you place the insulation.
Flue connection
Gabriel stoves can be either rear or top connected.
A prefabricated flue can be directly connected on the
top of the stove. Check with your local dealer for the
best solution.
Step-by-step installation
Please follow the step-by-step assembly and pay
attention to the control measurements that are shown.
A certain tolerance is allowed but make sure the
control measurements are kept as it has a profound
impact on the tiling, which is to follow.
The thickness of joints should be approx.10 mm. For
good adherence, wipe the contact surfaces with a
squeezed sponge before jointing.
During the assembly the outer rings are always to be
one step ahead of the inner blocks.
Equipment
Trowels, brick layer, a long water level, radiator
brush, folding rule, chisel, buckets, sponge, rubber
mallet, covering plastic, angular grinder, hack saw, 2
ladders, joint sponge, wooden wedge.
Material included in the delivery
• Clay and sand - Clay mortar mix: 1:3½ (1 part
of clay to 3½ part of sand).
• Tile adhesive
• Grout
• Silicon - if during transport a module is broken it
can easily be fixed with the supplied heat-resistant
silicon or clay mortar by gluing the pieces together.
Safety instructions
Read these instructions carefully before
starting the assembly. Incorrect assembly
can cause serious damage and fire risk.
Make sure prior to the assembly that the
building permit is approved and that the
local chimney sweep has approved the
installation.