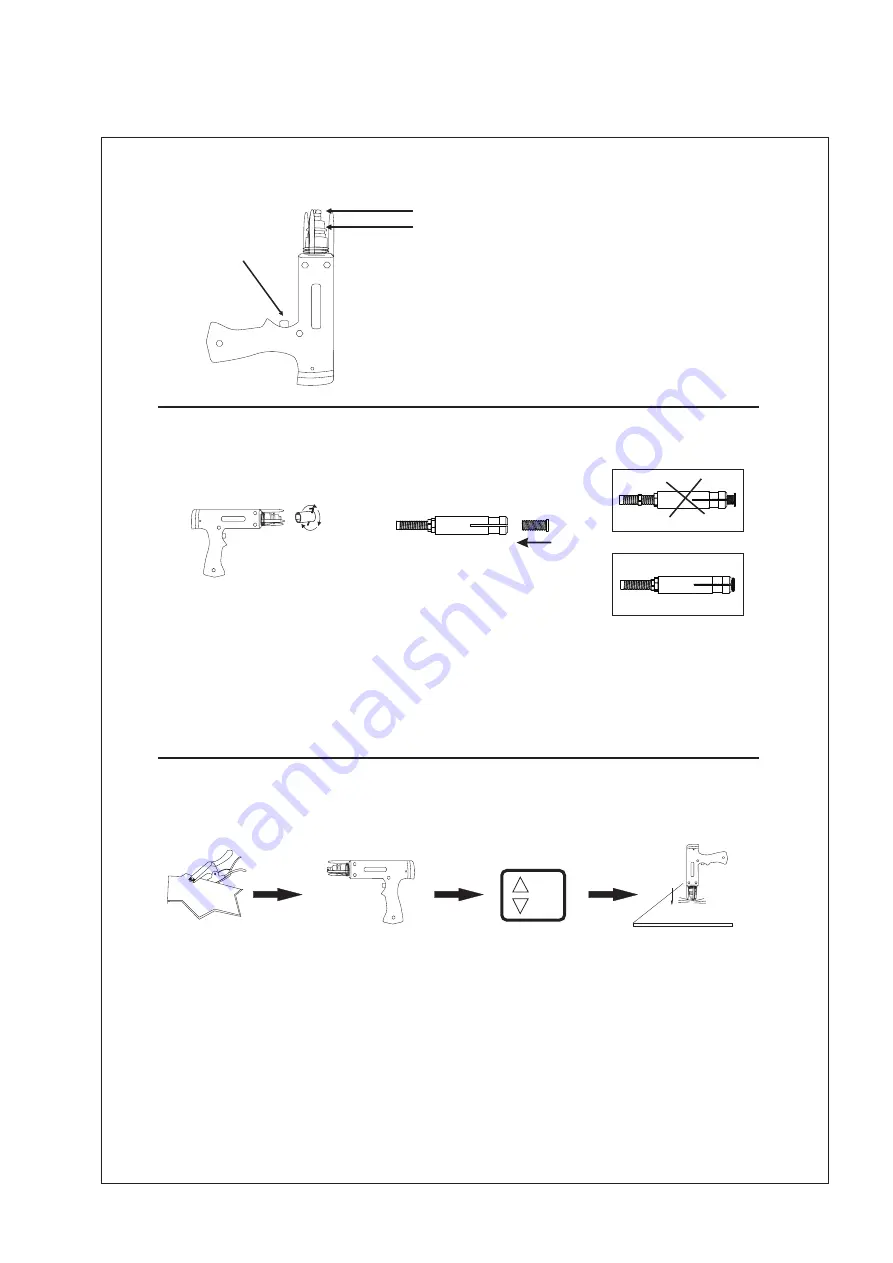
1
2
%
3
Wrong
R i g h t
(
1
)
(
2
)
A. Aluminium welding gun
1
、
Ferrule
2
、
Trigger switch
3
、
Weld chuck
B. Aluminium welding gun setup
1.Insert a ferrule grip into the foot and tighten the frerule
2.Insert a stud into the weld chuck.A different chuck is required for each different stud
diameter(0.6mm chuck with 0.6mm stud,0.4mmchuck with 0.4mm stud)
3.Place the weld chuck into the chuck adapter.Make sure that the chuck is seated
properly in the adapter.
C. Aluminium welding gun application
Connect ground cable to
a clean,paintfree location
on metal workpiece,as
close to welding area as
possible.
Weld gun with
chuck and stud
Adjust current
(
See page 9
)
Place the weld gun perpendicular
to the dent area on the workpiece.
Apply pressure to the gun.Hold
gun steady and push trigger to
weld..
Remark
:
1
、
Setting amperage too high or time too long can cause workpiece surface (vehicle
body)damage .
Please weld other workpieces for practice before actual operations.
2
、
Setting correct amperage and time according to the workpiece thickness.
3
、
Continuing another operation is applicable after these procedures finished .If not, please
shut off the main power supply and switch off
the
unit
.
P a g e . 1 1
3 . A l u mi n iu m W el di ng G u n A pp l ic a tio n