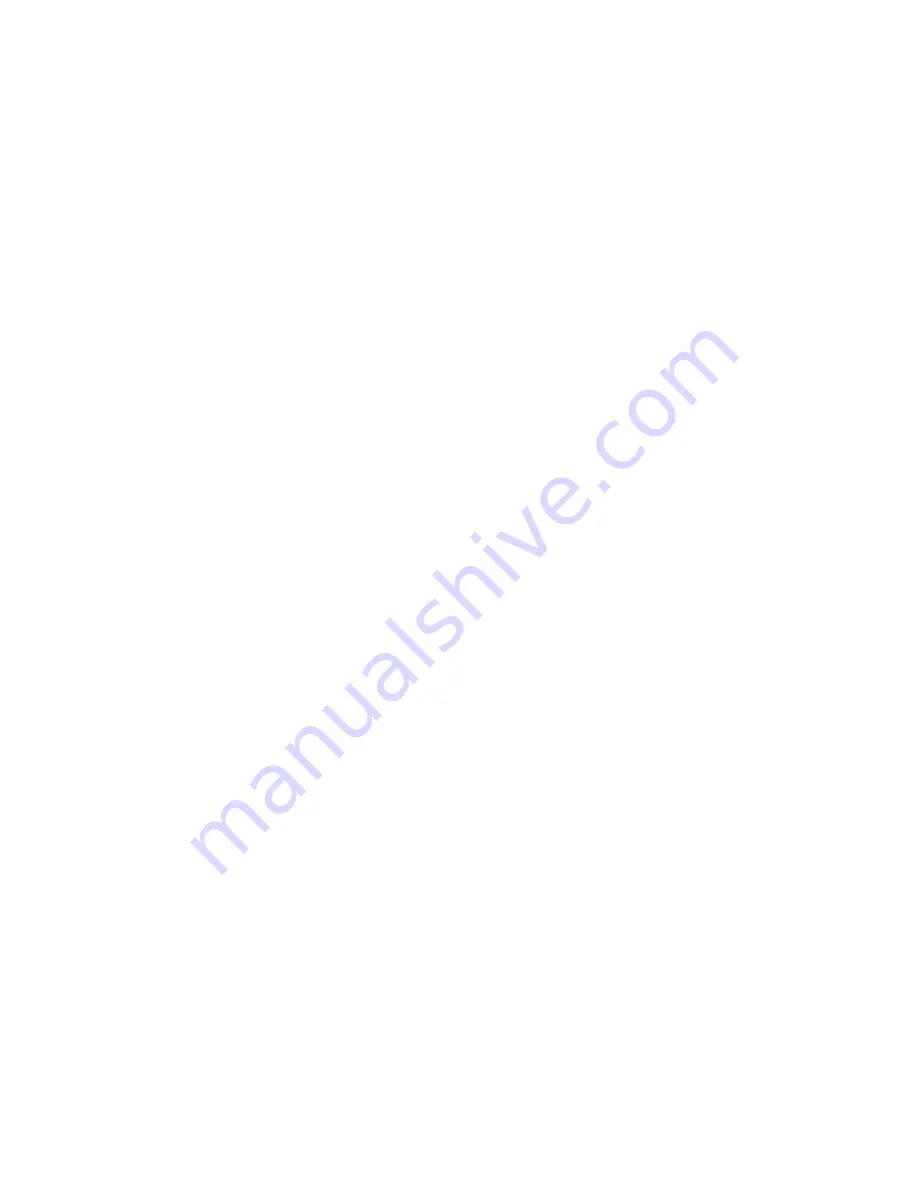
Product Specification
Page 11 of 18
1303090MS01
LA-309 Controlled Atmosphere Infrared Furnace
April 15, 2009
11.0 FINISH
11.1
All exposed parts (frame, uprights, and panels) shall be painted with corrosion-resistant paint.
Color shall be to Manufacturer’s specification unless otherwise specified at time of order:
Sherwin Williams Stone Gray, P/N F63TXA-0382-2322 Polane-T Texture or equal.
12.0 FACILITIES IMPACT
12.1
Thermal Load: Properly exhausted systems shall induce approximately the following thermal
load upon the facility: 1-1.5 kW
12.2
Hazardous Exhausts or Products: Customer product induced only.
12.3
Noise Impact: Negligible
12.4
Water requirements: none
13.0 DOCUMENTATION
13.1
Manufacturer shall provide Owner’s manual documentation as follows:
13.1.1
One (1) printed copy of Owner’s manual including machine specific instructions for
installation; equipment operation; service and troubleshooting; specifications; engineering data
sheets; drawings and schematics; and MSDS.
13.1.2
One (1) perfect bound printed copy of FurnacePros Continuous Belt IR Furnace Reference
Manual including information on IR furnace nomenclature, thermal processing; furnace control
and software; maintenance, troubleshooting and calibration; and process engineering.
13.1.3
One (1) Reinstallation Software CD-ROM shall be supplied containing the furnace program,
software utilities, and soft versions of the Owner’s Manual, Reference Manual and drawings.
13.2
In addition, soft versions of items 13.1.1 and 13.1.2 shall be installed on the furnace computer,
along with the Dell™ help screen for access at the furnace PC.
14.0 ACCEPTANCE CRITERIA
14.1
Manufacturer’s QA shall assure that the furnace is manufactured as described in this document
and meeting the requirements herein. The furnace shall be certified and documented according
to Manufacturer’s standard quality assurance procedures before Customer factory witness
testing (FAT) begins.
14.2
Any Customer acceptance criteria shall be mutually agreed upon and must be presented in
writing at least 4 weeks prior to furnace in-plant acceptance testing (FAT).
14.3
Manufacturer shall provide Purchaser with a minimum of 2 weeks notice of when the
equipment will ready for Factory Acceptance Testing (FAT). Purchaser may witness FAT in
Manufacturer’s facility. Duration of FAT testing is normally 1-2 days.
14.4
The furnace shall be fully shop tested before shipment. Contract price is based on all testing
performed with 480 Vac, 60 Hz, 3-phase power source. Alternate power requirements can be
provided at additional cost.
14.5
Upon acceptance of the furnace by Manufacturer’s QA (with or without Customer
representative present) and upon completion of final punch-list items, Manufacturer shall have
fulfilled its obligation of in-plant acceptance and shall ready the furnace for shipment.
14.6
Purchaser shall then receive a notification that the equipment has successfully completed the
Factory Acceptance Testing (FAT) and is ready for shipment.
14.7
Manufacturer shall provide startup and training services as purchased and if so provided, final
testing shall be performed at Purchaser’s site after completion of installation and startup.
Summary of Contents for LA-309
Page 5: ...10 004 676 110000 v WARRANTY Warranty goes here ...
Page 6: ...vi LA 309 Owner s Manual ...
Page 12: ...Contents xii LA 309 Owner s Manual ...
Page 20: ...Section 1 1 8 LA 309 Owner s Manual ...
Page 68: ...Section 3 3 28 LA 309 Owner s Manual ...
Page 70: ...Section 4 4 2 LA 309 Owner s Manual ...
Page 72: ...Section 4 4 4 LA 309 Owner s Manual ...
Page 98: ...Section 5 5 2 LA 309 Owner s Manual ...
Page 100: ...Section 5 5 4 LA 309 Owner s Manual ...
Page 106: ...Section 5 5 10 LA 309 Owner s Manual ...
Page 108: ...Section 5 5 12 LA 309 Owner s Manual ...
Page 110: ...Section 5 5 14 LA 309 Owner s Manual ...
Page 112: ...Section 6 6 2 LA 309 Owner s Manual ...
Page 114: ......
Page 115: ......
Page 126: ...Section 7 1 Fiberfrax Cements MSDS 042006 Owner s Manual ...
Page 139: ...MSDS 2 Fiberfrax Duraboard MSDS 042006 MATERIAL SAFETY DATA SHEETS ...
Page 140: ...Section 7 2 Fiberfrax Duraboard MSDS 042006 Owner s Manual ...
Page 153: ...MSDS 3 Fiberfrax Fibers MSDS 042006 MATERIAL SAFETY DATA SHEETS ...
Page 154: ...Section 7 3 Fiberfrax Fibers MSDS 042006 Owner s Manual ...
Page 167: ...MSDS 4 Fiberfrax Papers MSDS 042006 MATERIAL SAFETY DATA SHEETS ...
Page 168: ...Section 7 4 Fiberfrax Papers MSDS 042006 Owner s Manual ...
Page 181: ...MSDS 5 Magnaform MSDS 050406 MATERIAL SAFETY DATA SHEETS ...
Page 182: ...Section 7 5 Magnaform MSDS 050406 Owner s Manual ...
Page 183: ......
Page 184: ......
Page 185: ...Section 7 6 RTU Silicone Red Hi Temp 042006 Owner s Manual ...
Page 186: ...MSDS 6 RTU Silicone Red Hi Temp 042006 MATERIAL SAFETY DATA SHEETS ...
Page 189: ...Section 7 7 Kaowool Insulation MSDS 050406 Owner s Manual ...
Page 190: ...MSDS 7 Kaowool Insulation MSDS 050406 MATERIAL SAFETY DATA SHEETS ...
Page 201: ...Material Safety Data Sheets 7 15 Notes ...
Page 202: ...Section 7 7 16 Owner s Manual ...
Page 204: ...Section 8 Owner s Manual ...
Page 206: ...Section 8 Owner s Manual ...
Page 212: ...iv Operation and Troubleshooting ...
Page 214: ...vi Operation and Troubleshooting ...
Page 224: ...Page 10 Operation and Troubleshooting ...
Page 231: ...9 1 Section 9 APPENDIX B 9 1 EC913 CALIBRATION REPORT 9 2 SERIES EC900 OXYGEN ANALYZERS ...
Page 232: ...Section 8 Owner s Manual ...
Page 233: ......
Page 234: ...Section 8 Owner s Manual ...
Page 279: ...Section 8 Owner s Manual ...
Page 281: ...MSDS MATERIAL SAFETY DATA SHEETS ...
Page 282: ...16 Notes ...