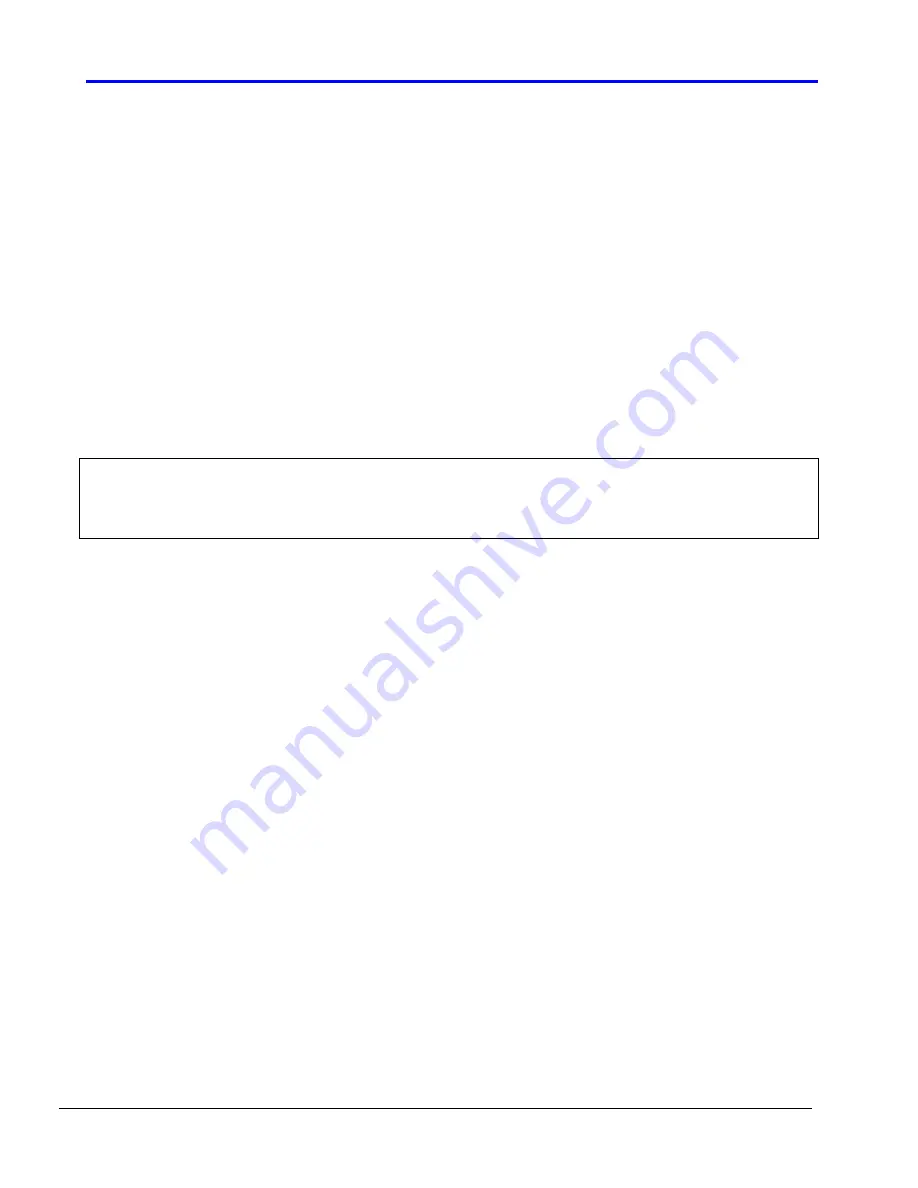
Section 3
3.17 Calibration
Consult the Reference Manual for most calibration procedures.
3.17.1 SCR
Follow the calibration procedure described in the Reference Manual.
3.17.2 Belt speed
Go to the calibration screen. Check the box 50% output. Using a stopwatch, time the belt speed over a
known distance, and calculate the actual belt speed. Enter the number in the Actual speed field. Un-check
the 50% output box. See Reference Manual Chapter 7 for more detail.
3.17.3 Thermocouples
The thermocouples are pre-calibrated. They do not require any additional calibration.
3.17.4 PID tuning
If you notice unstable behavior in a certain zone, use the following procedure to retune the PID:
NOTE: This procedure should only be attempted by qualified personnel. Unreasonable PID
parameters can stress the components of the system and cause premature failure of some
electrical systems.
Go to the recipe screen and select the PID tuning for the zone you’re interested in. Write down the values of
Gain and Integral before you start changing them! If all else fails, you can return to the factory default.
Set the integral to the maximum possible value and the Gain to 1. Wait until the temperature stabilizes.
Increase the Gain by 10%. Repeat until the temperature starts oscillating. Always wait for at least 5
oscillations before changing any parameters again. The temperature will be oscillating at a value BELOW
the setpoint. This is normal. The temperature will be anywhere between 5° and 50°C below the setpoint.
Now set the Integral to the period of previous oscillations (usually between 5 and 15 seconds). Round up to
the nearest integer. The temperature will slowly drift to a new value. Reduce the Integral term for faster
convergence.
At that point, the system may start oscillating again. Decrease the Gain by an additional 10% until stable.
The heating process inside the chamber is a first order process with very little lag time. This means that the
PID does not need a Derivative value to operate.
Oscillations are caused by gain too high, integral too short, or rate too long. Never set rate to more than one-
fourth of integral time. Sluggish response is caused by gain too low, integral too long, or rate too short.
The PID values will work over a rather wide range of temperature. However, on a High Temperature
furnace, the PID might require tuning for the low range of temperature, around 200°C, and different set of
parameters above 500°C. The machines are set up for one set of PID parameters at the factory. For furnace
fine tuning, it is the responsibility of owner’s process engineer to determine the final settings.
3-24
LA-309 Owner’s Manual
Summary of Contents for LA-309
Page 5: ...10 004 676 110000 v WARRANTY Warranty goes here ...
Page 6: ...vi LA 309 Owner s Manual ...
Page 12: ...Contents xii LA 309 Owner s Manual ...
Page 20: ...Section 1 1 8 LA 309 Owner s Manual ...
Page 68: ...Section 3 3 28 LA 309 Owner s Manual ...
Page 70: ...Section 4 4 2 LA 309 Owner s Manual ...
Page 72: ...Section 4 4 4 LA 309 Owner s Manual ...
Page 98: ...Section 5 5 2 LA 309 Owner s Manual ...
Page 100: ...Section 5 5 4 LA 309 Owner s Manual ...
Page 106: ...Section 5 5 10 LA 309 Owner s Manual ...
Page 108: ...Section 5 5 12 LA 309 Owner s Manual ...
Page 110: ...Section 5 5 14 LA 309 Owner s Manual ...
Page 112: ...Section 6 6 2 LA 309 Owner s Manual ...
Page 114: ......
Page 115: ......
Page 126: ...Section 7 1 Fiberfrax Cements MSDS 042006 Owner s Manual ...
Page 139: ...MSDS 2 Fiberfrax Duraboard MSDS 042006 MATERIAL SAFETY DATA SHEETS ...
Page 140: ...Section 7 2 Fiberfrax Duraboard MSDS 042006 Owner s Manual ...
Page 153: ...MSDS 3 Fiberfrax Fibers MSDS 042006 MATERIAL SAFETY DATA SHEETS ...
Page 154: ...Section 7 3 Fiberfrax Fibers MSDS 042006 Owner s Manual ...
Page 167: ...MSDS 4 Fiberfrax Papers MSDS 042006 MATERIAL SAFETY DATA SHEETS ...
Page 168: ...Section 7 4 Fiberfrax Papers MSDS 042006 Owner s Manual ...
Page 181: ...MSDS 5 Magnaform MSDS 050406 MATERIAL SAFETY DATA SHEETS ...
Page 182: ...Section 7 5 Magnaform MSDS 050406 Owner s Manual ...
Page 183: ......
Page 184: ......
Page 185: ...Section 7 6 RTU Silicone Red Hi Temp 042006 Owner s Manual ...
Page 186: ...MSDS 6 RTU Silicone Red Hi Temp 042006 MATERIAL SAFETY DATA SHEETS ...
Page 189: ...Section 7 7 Kaowool Insulation MSDS 050406 Owner s Manual ...
Page 190: ...MSDS 7 Kaowool Insulation MSDS 050406 MATERIAL SAFETY DATA SHEETS ...
Page 201: ...Material Safety Data Sheets 7 15 Notes ...
Page 202: ...Section 7 7 16 Owner s Manual ...
Page 204: ...Section 8 Owner s Manual ...
Page 206: ...Section 8 Owner s Manual ...
Page 212: ...iv Operation and Troubleshooting ...
Page 214: ...vi Operation and Troubleshooting ...
Page 224: ...Page 10 Operation and Troubleshooting ...
Page 231: ...9 1 Section 9 APPENDIX B 9 1 EC913 CALIBRATION REPORT 9 2 SERIES EC900 OXYGEN ANALYZERS ...
Page 232: ...Section 8 Owner s Manual ...
Page 233: ......
Page 234: ...Section 8 Owner s Manual ...
Page 279: ...Section 8 Owner s Manual ...
Page 281: ...MSDS MATERIAL SAFETY DATA SHEETS ...
Page 282: ...16 Notes ...