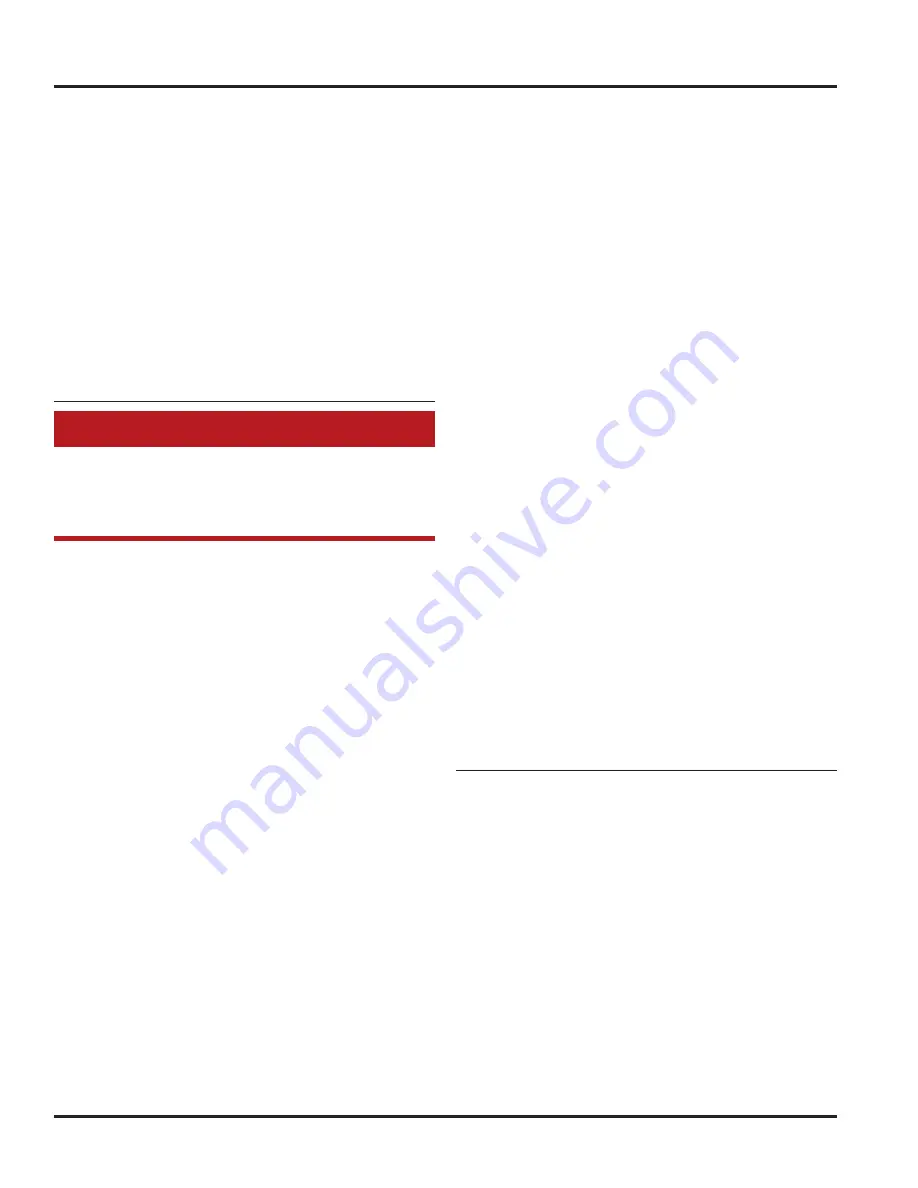
2 - INSTALLATION
© Fulton 2018
2-18
VSRT_IOM_2018-1213
11. The specific gas pressure requirement for each
boiler is indicated on the boiler nameplate,
located on the boiler. Parameters depend on
what fuel(s) the boiler is designed to burn. (See
Table 4 gas inputs and pressures.)
12. For
natural gas
a pressure of 3” to 13.8” w.c. is
required at the gas train at full input. Do not
exceed 13.8” w.c. For
propane
, a pressure of 7”
to 13.8” w.c. is required at the gas train at full
input. Do not exceed 13.8” w.c. For installations
equipped with gas pressures exceeding 13.8”w.c.,
consult the factory for gas pressure requirements.
Electrical Supply
!
WARNING
Assure all electrical connections are powered down
prior to attempting replacement or service of electrical
components or connections of the equipment.
NOTE
Adhere to the following:
1. Install wiring and grounding equipment in
accordance with jurisdictional authority. In
the absence of such requirements, install in
accordance with National Electrical Code, ANSI/
NFPA 70.
2. Make sure the information on the electrical
drawing corresponds to your voltage and
frequency. Check the supply voltage and make
sure that there is no over-or under-voltage
exceeding 10% of the nominal value.
3. For three-phase motors, the line to line full load
voltage must be balanced within 1% of the rated
motor voltage. Operation outside of these limits
will degrade motor performance. 575V rated
motors cannot be operated at voltages above
600V. Depending on the motor manufacturer, a
208V rated motor may not be able to run below the
design voltage.
4. Locate schematic. Each boiler is shipped with its
own unique electrical schematic diagram, a copy
of which is located in an envelope on the inside of
the panel box door.
5. A wall-mounted, fused disconnect sized for the
unit must be provided and fitted by the client/
contractor if disconnect is not supplied on the
panel.
6. Fuses must be sized according to motor name
plates and local electrical codes.
7. Connect power to the terminal strip as supplied
on the inside of the panel box.
Note:
Single
skid systems are generally shipped
completely prewired.
8. Multiple skid systems may require wiring
between the skids. Please note that Fulton
will run conduit and wire the devices on each
skid. For devices that are disconnected for
shipping, the wire will be left at the end of the
conduit where possible and wired in the field
(by others). When the system has multiple skids
that are adjoining, the conduit will be installed to
break at the skid joints. The wire for the conduit
running between the skids will be shipped loose
to prevent damage when the skids are put back
together. These wires will need to be run by the
installing contractor in the field and wired to
proper locations. If there is wiring between skids
that are not adjoining, then this will need to be
done by others.
9. If the unit is not skid-mounted at the factory,
the client/contractor is required to wire the feed
water pump starter.
Note:
If the pump motor is
not supplied by Fulton, the motor starter may not
be supplied.
Water Chemistry
RECOMMENDED WATER CONDITIONS FOR
BOILERS/UNFIRED STEAM GENERATORS
Table 5 lists recommendations for feed water and boiler
water. Contact your local water treatment professional
for testing and treatment recommendations. It is very
important that a strict water treatment program is
followed.
It is critical that the boiler water chemistry follow Table
5 whenever water is in the boiler. Solids that enter with
the feed water will concentrate in the boiler. A regular
schedule of boiler blowdown (see
Maintenance
section
of this manual) must be maintained to prevent high solid
concentrations from corroding the vessel or forming
deposits.