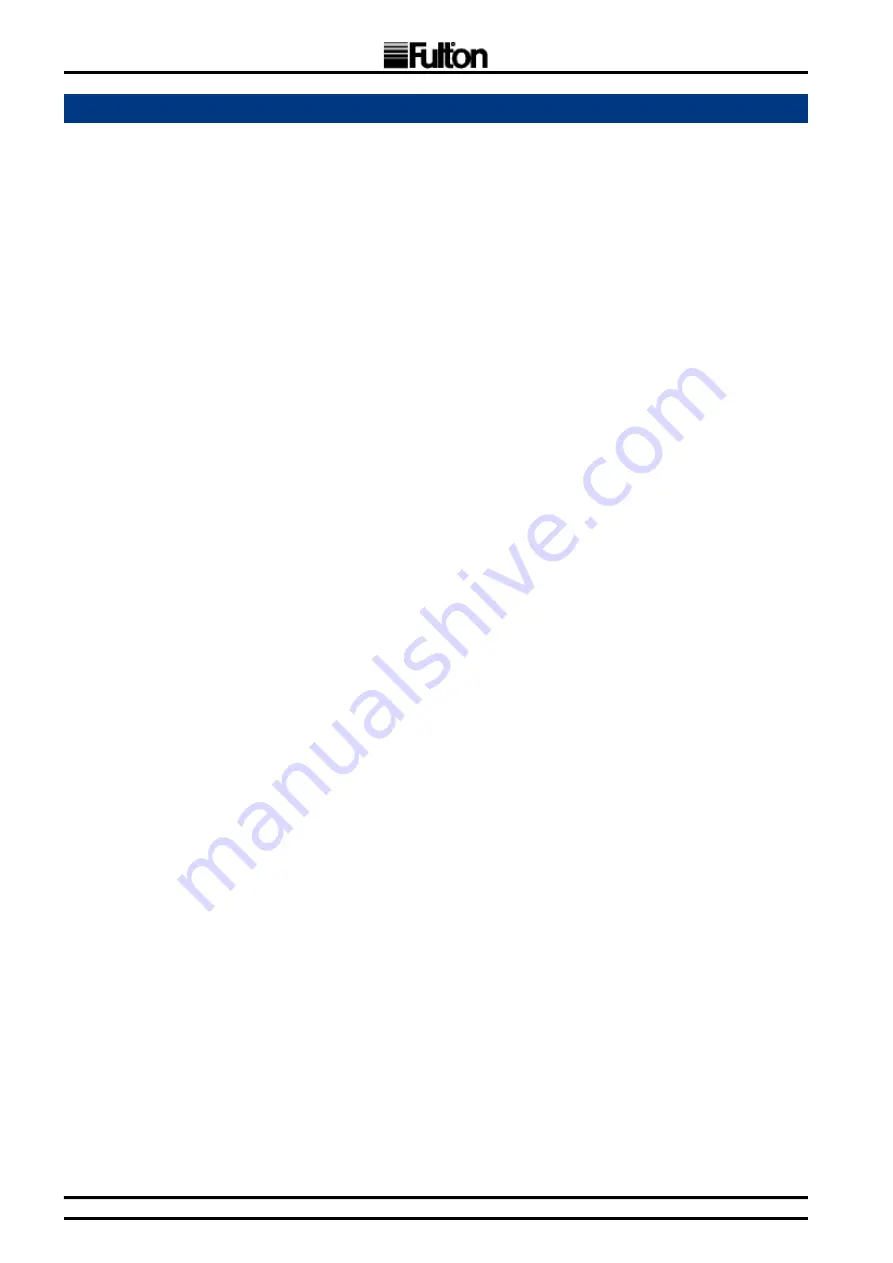
FT-C Vertical Electric Thermal Fluid Heater Manual 12 2013 ISSUE 1
Page 44
3
3.6.8
GAS FIRED MODULATING BURNER
SETTING PILOT
1) Verify the main burner switch is in the OFF position.
2) Supply power to the heater. The AZL will display “system test” and then move to the main
menu.
3) Select PWLogin, press Enter. Select AccessServ. Press Enter. (This type of step will be shown
as PWLogin > AccessServ for the remainder of this section. Enter the service passwords
using the arrow key. The password is case sensitive. The case of a letter can be changed by
pressing the other arrow key. (For example, if you used the right arrow key to get to the letter
A, press the left arrow key to get a). After you have pressed Enter on the last character of the
password, press Enter once more to accept the password. If you do not have the password,
contact your Fulton Authorized Representative to perform the changes. Service=NB# or
OEM=AAAA (Enter after each A).
4) Select Params&Display. Press Enter. Select Ratio Control. Press Enter. Select ProgramStop.
Press Enter. Change the Program Stop to 44 Interv1 by using the arrow keys. Con! rm the
change by pressing Enter. This will set the burner management system to a ‘pilot hold’ setting.
5) Verify that the current value “curr” changes to 44 Interv 1.
6) The full listing of program stops are:
» 24: Air damper in the prepurge position
» 32: Traveling to the FGR position
» 36: Ignition position (before pilot ignition)
» 44: Ignition position (after pilot ignition)
» 52: Ignition position (after main burner ignition)
» 72: Air damper in the postpurge position
» 76: Traveling to the FGR position
7) Press Escape 4 times to get back to the main menu.
8) Under ManualOperation > Setload, change the load to 0% by using the arrow keys. Press Enter
and verify the 0% has been acknowledged in the “curr” field.
9) Press Escape once to get back to the ManualOperation menu.
10) Under Auto/Manual/OFF, change the operation to Burner On by using the
arrow keys. Press enter and verify that “Burner On” is acknowledged in the
current field.
11) Press Escape twice to get back to the main menu.
12) Turn the main burner switch Local or On position.
13) Increase the set point. Under operation-Heater set point go to setpoint W1 using the arrow key
then press Enter. Change the set point under new, using the arrows and press Enter. The new
set point should appear under actual and displayed in degrees.
14) After several seconds the burner control will start its pre-ignition phase andthe blower will start.
15) You can observe the status of the burner by going to the main menu (by pressing Escape) then
selecting Operational Stat > Normal Operation.
16) The unit will purge then drive to the ignition position and the pilot should light.
Summary of Contents for FT-0080C
Page 38: ...FT C Vertical Electric Thermal Fluid Heater Manual 12 2013 ISSUE 1 Page 30...
Page 80: ...FT C Vertical Electric Thermal Fluid Heater Manual 12 2013 ISSUE 1 Page 72...
Page 85: ...FT C Vertical Electric Thermal Fluid Heater Manual 12 2013 ISSUE 1 Page 77 5...
Page 86: ...FT C Vertical Electric Thermal Fluid Heater Manual 12 2013 ISSUE 1 Page 78 5...
Page 87: ...FT C Vertical Electric Thermal Fluid Heater Manual 12 2013 ISSUE 1 Page 79 5...
Page 88: ...FT C Vertical Electric Thermal Fluid Heater Manual 12 2013 ISSUE 1 Page 80 5...
Page 90: ...FT C Vertical Electric Thermal Fluid Heater Manual 12 2013 ISSUE 1...