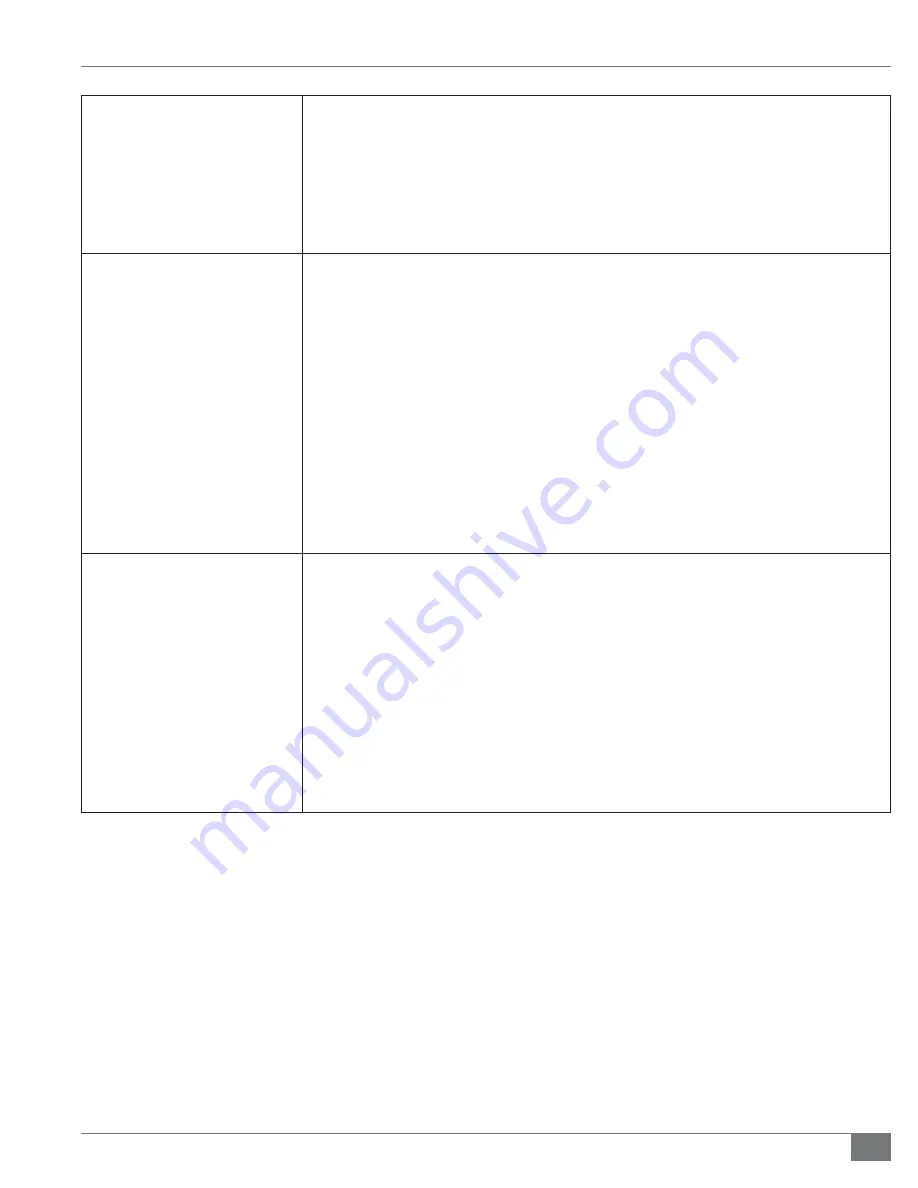
Questions? Call (315) 298-5121, or visit us online at www.fulton.com
SECTION 4
FBW-IOM-2014-0311
MAINTENANCE
4-5
Faulty Wiring Connections
1. With power off, check continuity of circuit through each point in the circuit.
2. If a break in the circuit is found, the connection should be repaired use the following tools:
wire cutters, wire strippers, fl at-head screwdriver, Phillips head screwdriver, crimping pliers,
needle nose pliers, tape, connectors, or wire splice connectors.
3. After the break has been corrected recheck it with a continuity light with the power off. Then
turn off power on and check with multi-meter.
Faulty Contactor Contact
Points
1. If a contactor has burned or dirty contacts, they should be brushed clean with a fi ne sandpa-
per or emery paper.
2. If they are burned through, the contactor should be replaced.
3. If they do not engage completely, the contactor coil may be weak and the contactor should be
replaced.
4. An amp meter may be used to check amp draw through each leg of the contactor.
5. With power off an ohm meter can be used to check the contactor points between the contac-
tor supply and contactor feed to verify the contactor is pulling in. A visual inspection on the side
of the contactor can be made to see if the contactor is engaging.
6. All power coming into the contactor should be checked with a volt meter to verify proper feed-
ing of contactor to eliminate possible overload.
7. If a contactor is in need of replacement, mark each wire and remove with a fl at-head screw-
driver; remove the base screws and replace with new contactor.
Faulty Elements
1. With the power off, a continuity tester can be used to see if an element is burned out between
each point.
2. If the power is on, a volt meter can be used to check power between each point on the ele-
ments.
3. If an element is bad, it will require a fl at-head screwdriver to remove wires. Two crescent or
adjustable wrenches to remove bolts from element face. A new gasket and gasket seal should
be used when replacing the element.
4. Be sure to check incoming voltage and amperage to each element to avoid overloading the
element.
5. If the elements are dirty and not burned out, they may be cleaned by using caustic soda or
soda ash in a combined solution.