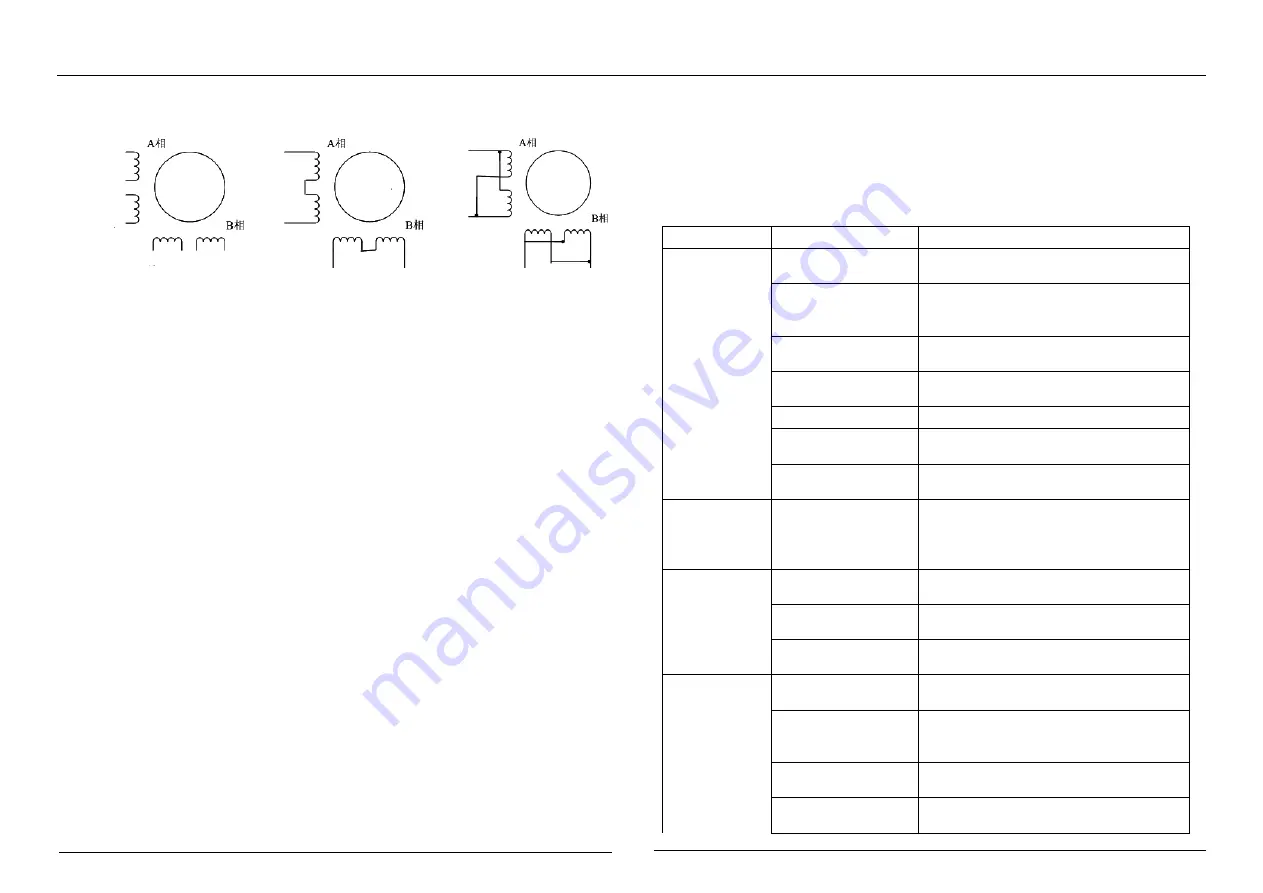
User’s Manual for FD430 Digital 2-Phase Stepper Driver
User’s Manual for FD430 Digital 2-Phase Stepper Driver
15 16
terminals of the same phase of the driver(A+,A- is one phase, B+,B- is another
phase). 57HS22 motor lead definition, Series and Parallel Connections method is
shown below.
3
)
FD430 driver can only drive 2-phase hybrid step motors, which cannot drive 3-phase
and 5-phase stepping motor.
4
)
The method of judging whether the stepping motor is connected in series or in
parallel is correct, When the driver is not connected, directly rotate the motor shaft
by hand, If it can rotate easily and evenly, then the wiring method is correct; If the
resistance is large and uneven rotation with a certain sound, then the wiring method
is incorrect.
Ⅷ
. Protection Functions
1
)
Short Circuit Protection / Over-current Protection
Over-current protection will be activated when continuous current exceeds the limit
current value or in case of short circuit between motor coils or between motor coil and
ground, and RED LED will turn on once within each periodic time (3 s). Reset the driver
by repowering it to make it function properly after removing above problems.
2
)
Over-voltage protection
When power supply voltage exceeds 38VDC, protection will be activated and RED
LED will turn on twice within each periodic time (3 s). Reset the driver by repowering it
to make it function properly after removing above problems.
3
)
Phase Error Protection
。
Motor power lines wrong & not connected will activate this protection. RED LED
will turn on four times within each periodic time (3 s). Reset the driver by repowering it
to make it function properly after removing above problems.
Attention
:
since there is no protection against power leads (
﹢
,
﹣
) reversal, it is critical
to make sure that power supply leads correctly connected to driver. Otherwise, the driver
will be damaged instantly.
Ⅸ
. Frequently Asked Questions
1. Problem Symptoms and Possible Causes
Symptoms
Possible Problems
Solution
Motor is not
rotating
No Power
Check the power supply circuit for normal
power supply
The motor shaft
strong, Control signal
is too weak.
Control pulse signal is too weak, Signal
current increased to 7~16mA
microstep resolution
is too small
select the right microstep resolution
setting
Current setting is too
small
Select the right current setting
Drive is protected.
Power on again
Enable signal is low
high.
Enable signal is high or not connected.
Does not respond to
Input control signals
Not powered.
Motor
rotating in the
wrong
direction
Motor phases may be
connected in reverse
Exchanging the connection of two wires
for a coil to the driver will reverse motion
direction.
Alarm
indicator is on
Wrong motor
connection
Check connection
Power supply is too
high or too low.
Check Power Supply
Motor or Driver is
bad
.
Replace motor or driver
Inaccurate
location
Control signal is
disturbed
Eliminate interference
Shielded ground is
not connected or
disconnect
Reliable grounding.
Open winding of
motor
Check motor wire
Micro-step resolution
setting is wrong.
select the right micro-step resolution
setting
Lead definition
Tandem
Parallel
57HS22
57HS22
57HS22
蓝
S45
红
S45
黄
S45
绿
S45
白
S45
橙
S45
棕
S45
黑
S45
Figure8 Tandem and Parallel connection