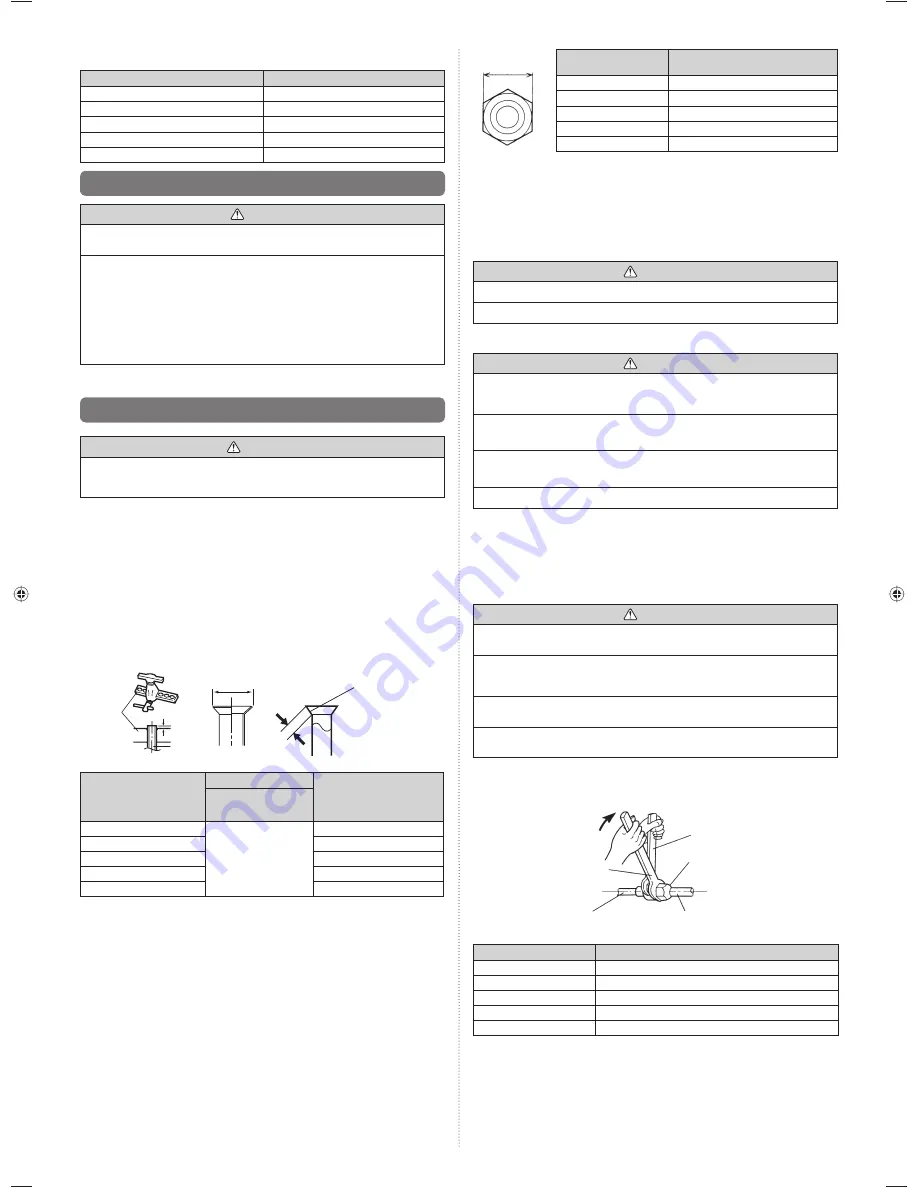
En-5
Width across
fl
ats
Pipe outside
diameter [mm (in.)]
Width across flats
of Flare nut [mm]
6.35 (1/4)
17
9.52 (3/8)
22
12.70 (1/2)
26
15.88 (5/8)
29
19.05 (3/4)
36
4.3.2. Bending pipes
•
If pipes are shaped by hand, be careful not to collapse them.
•
Do not bend the pipes in an angle more than 90°.
•
When pipes are repeatedly bend or stretched, the material will harden, making it
dif
fi
cult to bend or stretch them any more.
•
Do not bend or stretch the pipes more than 3 times.
CAUTION
To prevent breaking of the pipe, avoid sharp bends.
If the pipe is bent repeatedly at the same place, it will break.
4.3.3. Pipe connection
CAUTION
Be sure to install the pipe against the port on the indoor unit correctly. If the centering
is improper, the
fl
are nut cannot tighten smoothly. If the
fl
are nut is forced to turn, the
threads will be damaged.
Do not remove the flare nut from the indoor unit pipe until immediately before
connecting the connection pipe.
Do not use mineral oil on
fl
ared part. Prevent mineral oil from getting into the system
as this would reduce the lifetime of the units.
Be sure to connect the gas pipe after connecting the liquid pipe completely.
Detach the caps and plugs from the pipes.
(1)
Center the pipe against the port on the indoor unit, and then turn the
fl
are nut by
(2)
hand.
When the
fl
are nut is tightened properly by your hand, hold the body side coupling
(3)
with a separate spanner, then tighten with a torque wrench. (See the table below for
the
fl
are nut tightening torques.)
CAUTION
Hold the torque wrench at its grip, keeping it at a right angle with the pipe, in order to
tighten the
fl
are nut correctly.
Tighten the flare nuts with a torque wrench using the specified tightening method.
Otherwise, the
fl
are nuts could break after a prolonged period, causing refrigerant to
leak and generate a hazardous gas if the refrigerant comes into contact with a
fl
ame.
Connect the piping so that the control box cover can easily be removed for servicing
when necessary.
In order to prevent water from leaking into the control box, make sure that the piping is
well insulated.
When the
fl
are nut is tightened properly by your hand, hold the body side coupling with
a separate spanner, then tighten with a torque wrench. (See the table below for the
fl
are
nut tightening torques.)
Tighten with 2 wrenches.
Holding wrench
Flare nut
Connection pipe
Torque wrench
Indoor unit pipe
(Body side)
Flare nut [mm (in.)]
Tightening torque [N·m (kgf·cm)]
6.35 (1/4) dia.
16 to 18 (160 to 180)
9.52 (3/8) dia.
32 to 42 (320 to 420)
12.70 (1/2) dia.
49 to 61 (490 to 610)
15.88 (5/8) dia.
63 to 75 (630 to 750)
19.05 (3/4) dia.
90 to 110 (900 to 1,100)
Thicknesses of Annealed Copper Pipes (R410A)
Pipe outside diameter [mm (in.)]
Thickness [mm]
6.35 (1/4)
0.80
9.52 (3/8)
0.80
12.70 (1/2)
0.80
15.88 (5/8)
1.00
19.05 (3/4)
1.20
4.2. Pipe requirement
CAUTION
Refer to the Installation Manual of the outdoor unit for description of the length of
connecting pipe or for difference of its elevation.
Install heat insulation around both the gas and liquid pipes. Failure to do so may cause
water leaks.
Use heat insulation with heat resistance above 120 °C. (Reverse cycle model only)
In addition, if the humidity level at the installation location of the refrigerant piping is
expected to exceed 70 %, install heat insulation around the refrigerant piping. If the
expected humidity level is 70-80 %, use heat insulation that is 15 mm or thicker and if
the expected humidity exceeds 80 %, use heat insulation that is 20 mm or thicker. If
heat insulation is used that is not as thick as speci
fi
ed, condensation may form on the
surface of the insulation. In addition, use heat insulation with heat conductivity of 0.045
W/(m·K) or less (at 20 °C).
Use pipe with water-resistant heat insulation.
4.3. Flare connection (Pipe connection)
WARNING
Tighten the flare nuts with a torque wrench using the specified tightening method.
Otherwise, the
fl
are nuts could break after a prolonged period, causing refrigerant to
leak and generate a hazardous gas if the refrigerant comes into contact with a
fl
ame.
4.3.1. Flaring
Use special pipe cutter and
fl
are tool exclusive for R410A.
(1)
Cut the connection pipe to the necessary length with a pipe cutter.
(2)
Hold the pipe downward so that cuttings will not enter the pipe and remove any
burrs.
(3)
Insert the
fl
are nut (always use the
fl
are nut attached to the indoor and outdoor units
respectively) onto the pipe and perform the
fl
are processing with a
fl
are tool. Use
the special R410A
fl
are tool, or the conventional
fl
are tool. Leakage of refrigerant
may result if other
fl
are nuts are used.
(4)
Protect the pipes by pinching them or with tape to prevent dust, dirt, or water from
entering the pipes.
L
Die
Pipe
A
B
Check if [L] is
fl
ared uniformly
and is not cracked or scratched.
Pipe outside diameter
[mm (in.)]
Dimension A [mm]
Dimension B
-
0
0.4
[mm]
Flare tool for R410A,
clutch type
6.35 (1/4)
0 to 0.5
9.1
9.52 (3/8)
13.2
12.70 (1/2)
16.6
15.88 (5/8)
19.7
19.05 (3/4)
24.0
When using conventional
fl
are tools to
fl
are R410A pipes, the dimension A should be ap-
proximately 0.5 mm more than indicated in the table (for
fl
aring with R410A
fl
are tools)
to achieve the speci
fi
ed
fl
aring. Use a thickness gauge to measure the dimension A.
9379127035-02_IM.indb Sec1:5
9379127035-02_IM.indb Sec1:5
23/01/2013 16:25:41
23/01/2013 16:25:41