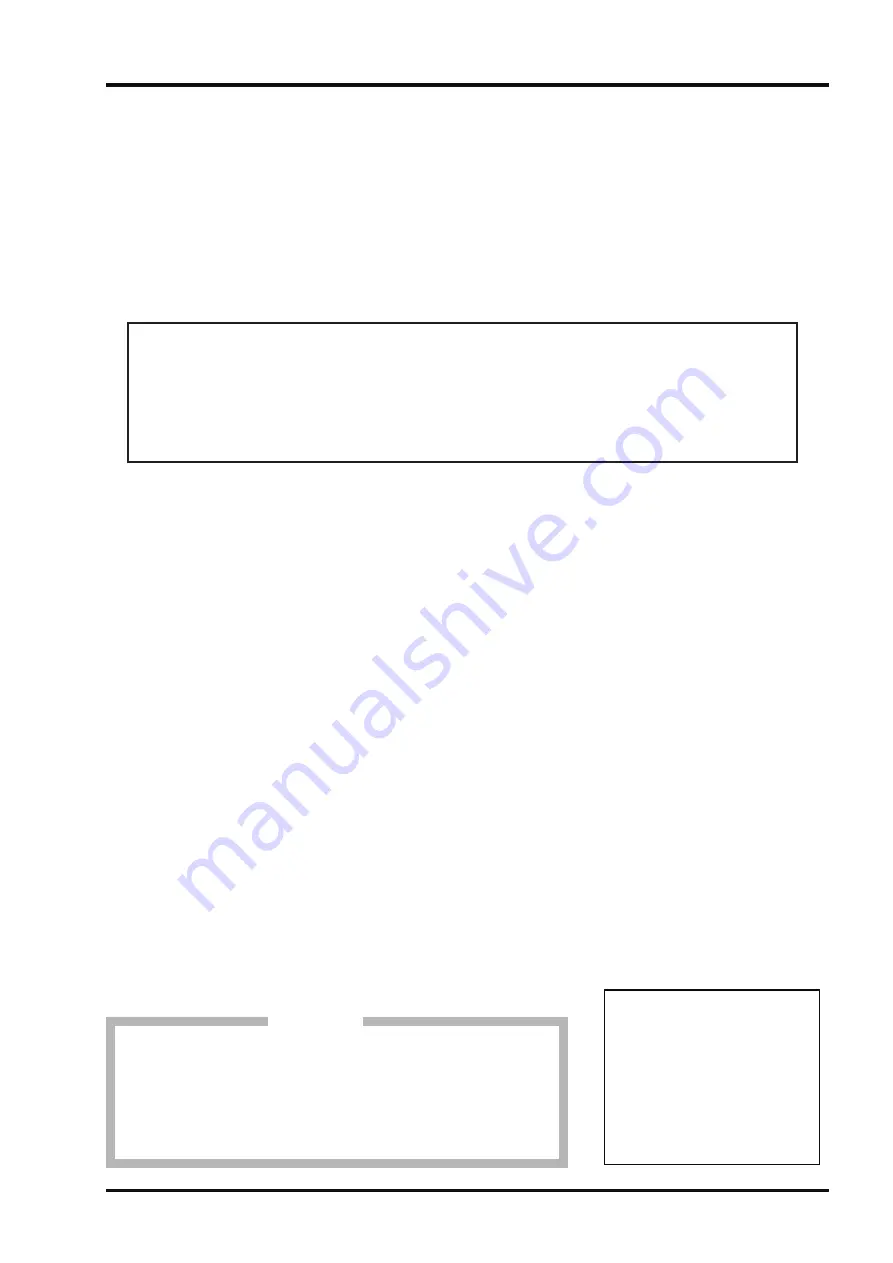
TN5A1191-E
i
This service manual describes the infrared gas analyzer (Type: ZPA, ZPB, ZPG).
This service manual is intended for use with the instruction manual to help you in understanding maintenance and
inspection for the infrared gas analyzer (ZPA, ZPB, ZPG). However, the basic operation of the analyzer is not covered
in this manual.
This manual provides information about the parameter settings in the factory mode, adjustment and precautions for
parts replacement, and troubleshooting for the infrared gas analyzer (ZPA, ZPB, ZPG) which are not covered in the
instruction manual.
This service manual gives you useful hints to take immediate remedy for after-sales service.
x
First read the instruction manual and service manual carefully until an adequate understanding is acquired,
and then proceed to installation, operation and maintenance of the gas analyzer. Wrong handling may
cause an accident or injury.
x
The specifications of this analyzer will be changed without prior notice for further product improvement.
x
Modification of this gas analyzer is strictly prohibited unless a written approval is obtained from the
manufacturer. Fuji Electric will not bear any responsibility for a trouble caused by such a modification.
Manufacturer:
Fuji Electric Co., Ltd.
Type:
Described in Fuji Electric’s company nameplate on main frame
Date of manufacture: Described in Fuji Electric's company nameplate on main frame
Product nationality: Japan
PREFACE
x
It is prohibited to transfer part or all of this manual without Fuji
Electric's permission in written format.
x
Description in this manual will be changed without prior notice
for further improvement.
Request
©Fuji Electric Co., Ltd. 2013
Issued in June, 2013
Rev. 1st edition October, 2013
Rev. 2nd edition July, 2018
Summary of Contents for ZPA
Page 1: ......
Page 11: ...TN5A1191 E 3 1 2 Optical unit ...
Page 14: ...6 TN5A1191 E 2 ZPB ...
Page 15: ...TN5A1191 E 7 3 ZPG ...
Page 41: ...TN5A1191 E 33 APPENDIX 2 DATA FLOW DIAGRAM ...
Page 45: ......