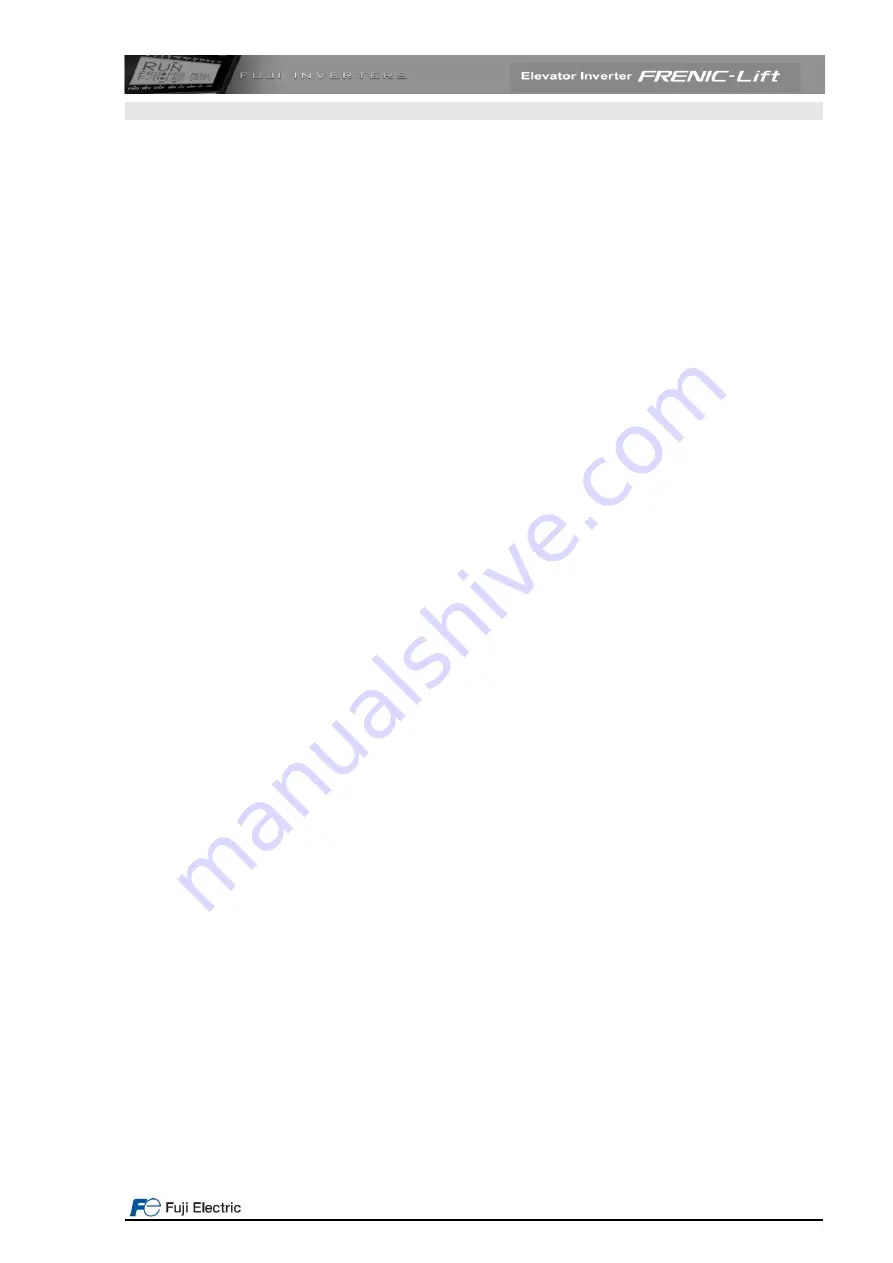
Page
3
of
42
Fuji Electric Europe GmbH
Contents
Chapters
Page
0. About this manual
4
1. Safety information
5
2. Conformity to European standards
7
3. Technical data
8
3.1
400 V series
8
3.2 200 V series (3ph and 1ph)
9
3.3 Over-rating in 400 V series
9
4. Removing and mounting the terminal block and front covers (5.5 to 22 kW)
10
5. Connections
11
5.1 Power connections
11
5.2 Control signals connection
12
5.3 Use of input terminals for speed set point selection
12
5.4 Control terminals description
13
a. Analog inputs
13
b. Digital inputs
13
c. Relay outputs
14
d. Transistor outputs
14
e. Communication connections (keypad, DCP 3, PC, CANopen)
15
6. Hardware configuration
16
7. Encoder
17
7.1 Standard (Built-in) input connection for 12/15 V incremental encoder
17
7.2 Option card OPC-LM1-IL for induction motors (with or without gear)
18
7.3 Option card OPC-LM1-PS1 for synchronous motors with ECN 1313 EnDat 2.1
19
7.4 Option card OPC-LM1-PR for synchronous motors with ERN 1387
20
8. Keypad operation
21
8.1 Overview
21
8.2 Keypad menus
22
8.3 Example of function setting
23
9. Signals timing diagram for normal travel using high and creep speeds
24
10. Signals timing diagram for travel using intermediate speeds
25
11. Settings
25
11.1 Introduction
25
11.2 Specific settings for induction motors (with encoder)
26
11.3 Specific settings for permanent magnet synchronous motors
27
11.4 Specific settings for induction motors in open loop (geared motors without encoder)
28
11.5 Additional settings for induction motor in open loop
29
11.6 Setting the speed profile
29
11.7 Recommended values for acceleration and deceleration related functions
31
12. Function tables
32
12.1 Travel optimization
32
12.2 Start and stop optimization
33
12.3 Additional functions and settings if needed
33
12.4 Input and output terminals function settings
34
12.5 Bit assignment of functions H98 and L99
34
13. Special operation
35
13.1 Short floor operation
35
13.2 Creepless operation
37
14. Recovering the lift from speed limiter condition
37
15. Rescue operation
38
16. Soft start for closed loop installations (IM and PMSM) with high friction
39
17. Alarm messages
40