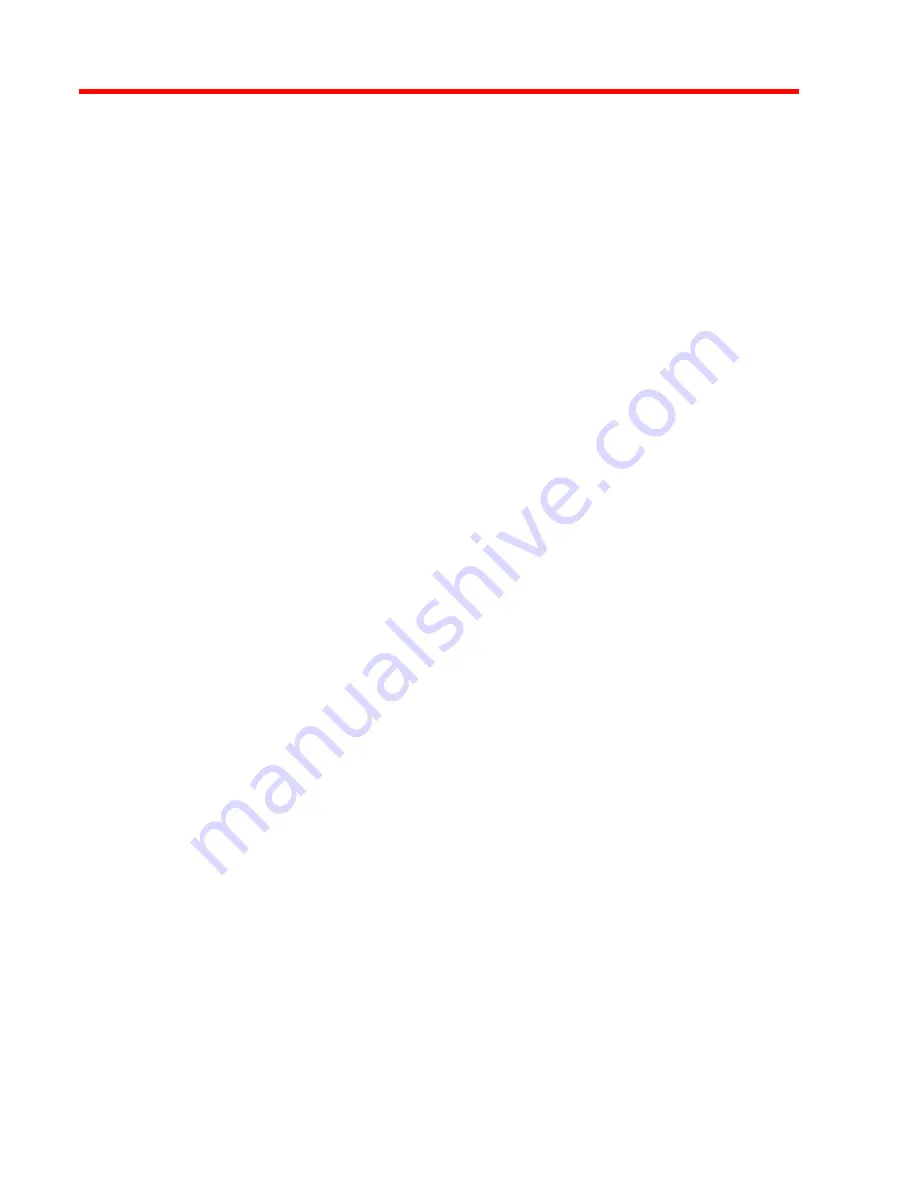
General information
Page 12
M1060008_US
v
1
Combination with Thermal Storage System
The Froling FHG boiler is required to be installed with a Thermal Storage
System, this system may require periodic maintenance. Please review
the periodic maintenance requirements of the thermal storage system
with the owner / system operator.
The Froling FHG boiler must be installed with a thermal storage system
capable of absorbing the complete output of the boiler during periods
when the building is not calling for heat. A means for protecting the
boiler against cold return water temperatures must also be provided.
Further information on acceptable ways of meeting these warranty
requirements is provided in the owner's manual.
The manual and supporting documentation must be retained by the
owner/ system operator for reference and future use.
The installer is responsible for familiarizing the owner/ system operator
with all aspects of boiler operations, safety procedures, monitoring and
cleaning requirements, shut down procedures, and annual maintenance
requirements.
1.2.6
Chimney connection / Chimney system
The Chimney is one of the most critical factors in the successful
operation of any solid fuel heater, including the Froling FHG boiler. A
good Chimney will provide a continuous and dependable draft to pull the
exhaust gasses out of the building.
NOTICE:
The boiler must be connected to a 6’’ (150 mm) diameter Factory-Built
Type UL 103 HT (ULC S629 in Canada) approved Chimney or to a tile-
lined masonry Chimney. The Chimney must be in good condition. If the
boiler is connected to a dirty or inadequate Chimney, it can present a
serious fire hazard.
All Chimneys and connections must conform to NFPA standard #211. No
other appliance should be connected to this flue unless allowed by the
local code authority. Consult your local inspector for Chimney
requirements and install the boiler in accordance with all applicable
codes. Please review the following diagram before connecting the boiler
to the Chimney.
The entire flue gas system is to be designed to prevent possible soot-up,
insufficient draft, and condensation.
Chimney must be 6’’ (150 mm) diameter listed UL-103 HT or ULC-S629
residential all-fuel type or tile-lined masonry. Flue Gas Pipe connection
to the chimney must be 6’’ (150 mm) diameter made of a minimum 24
MSG black steel.
Follow manufacturer’s installation instructions for installing and
supporting any specific Chimney product.
Flue gas exhaust temperatures can be low enough to cause
condensation in Chimneys. Condensation will, over time, damage a
masonry Chimney. Accordingly, installation of a stainless steel Chimney
liner (made with 316 or AL-294C alloys) inside the Chimney flue is
strongly recommended.