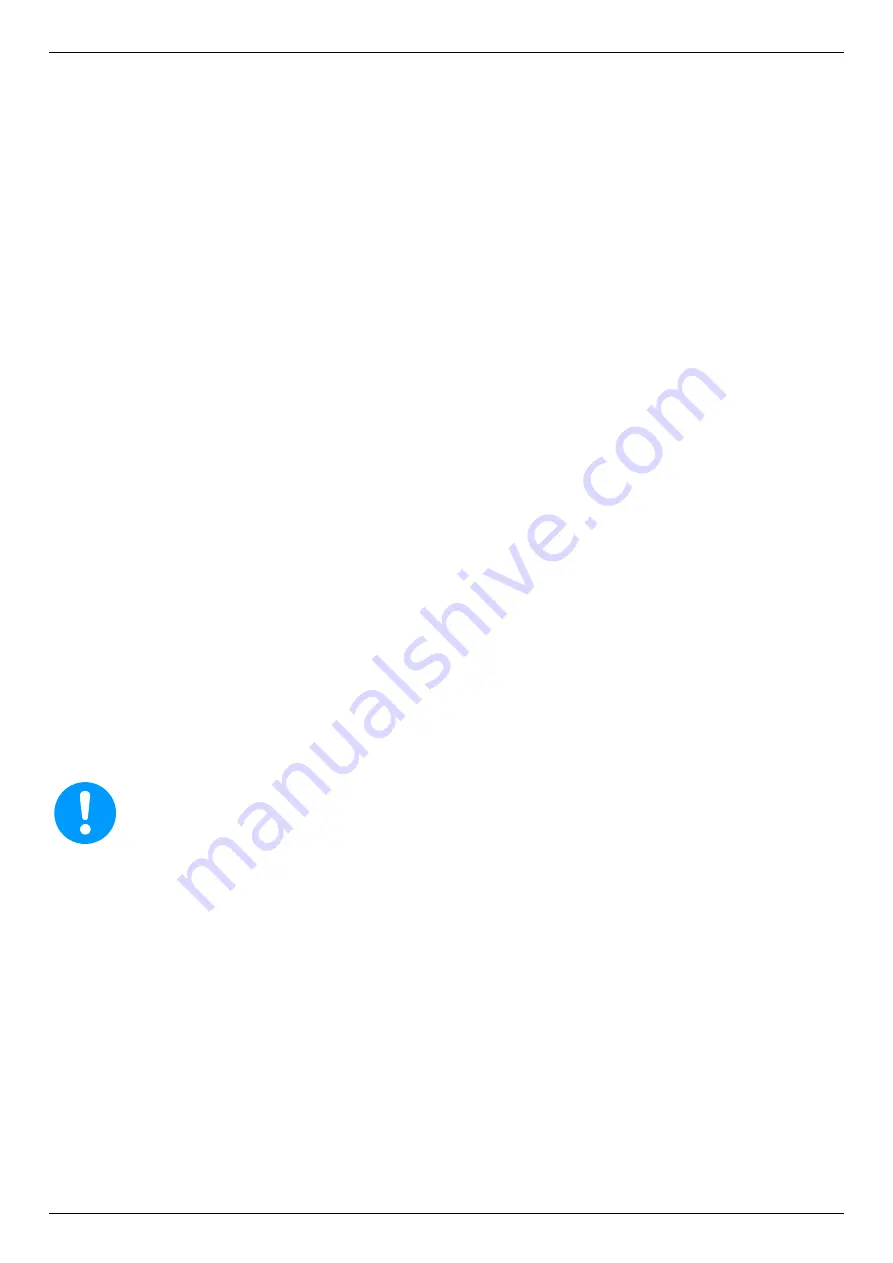
Technical data
24
– EN
ACT VS 3000 - 6000
11.10 Electronic Expansion Valve (EEV)
The electronic expansion valve (EEV) is an expansion device which is composed by a valve body operated from a
stepper motor. This component is managed from its driver according to heat exchanger superheating.
This parameter is calculated from the driver using a temperature sensor BS and a pressure sensor BP installed at
evaporator outlet refrigerant pipe. The driver operates the motor opening or closing the electronic expansion valve
(EEV) in order to keep constant at the setpoint the superheating.
On this dryer type, every Alu-Dry module has its electronic expansion valve EEV which control its superheating
independently.
In case of multiple Alu-
Dry module (1…n), every group composed by electronic expansion valve EEV (1…n), every
temperature sensor BS (1…n), every pressure sensor BP (1…n) and every driver DRV (1…n) is marked with a sticker.
The number on the sticker (1…n) identify the valve group.
11.11 Alu-Dry module
The heat exchanger module houses the air-to-air, the air-to-refrigerant heat exchangers and the demister type
condensate separator. The counter flow of compressed air in the air-to-air heat exchanger ensures maximum heat
transfer. The generous cross section of flow channel within the heat exchanger module leads to low velocities and
reduced power requirements. The generous dimensions of the air-to-refrigerant heat exchanger plus the counter flow
gas flow allows full and complete evaporation of the refrigerant (preventing liquid flood back to the compressor). The
high efficiency condensate separator is located within the heat exchanger module. No maintenance is required and the
coalescing effect results in a high degree of moisture separation.
11.12 Refrigerant pressure switches LPS
– HPS
As operation safety and protection of the dryer a series of pressure switches are installed in the gas circuit.
LPS:
Low-pressure protection device on the suction side of the compressor, trips if the pressure drops below the
pre-set value. The values are automatically reset when the nominal conditions are restored.
Calibrated pressure:
R407C
Stop 1.7 barg / 24,7 psig - Restart 2.7 barg / 39,2 psig
HPS:
This high-pressure controller device, located on the discharge side on the compressor, is activated when the
pressure exceeds the pre-set value. It features a manual-resetting button mounted on the protection device.
Calibrated pressure:
R407C
Stop 30 barg / 435 psig - Manual reset (P<23 bar / 334 psig)
11.13 Compressor crankcase heater
At low temperatures oil can more easily be mixed with the refrigerant gas. So, when the compressor starts, oil can be
drawn into the refrigeration circuit and liquid flood back to the compressor could occur.
To prevent this, an electrical resistance heater is installed in the bottom part of the compressor. When the system is
powered and the compressor is not running, this heater keeps the oil at the correct temperature.
Note!
During short-term shut down (max. two to three days), it is advisable to leave the dryer and the control
panel connected to the supply current circuit. Otherwise, it would be necessary at a restart of the dryer to
wait two hours, until the oil in the compressor has reached the specified operating temperature.
11.14 Electrical panel fan
Drivers enclosed in the electrical panel dissipates a consistent amount of heat. If the electrical panel temperature rises
above a set limit +40°C (104°F), a dedicated fan is activated to keep properly cooled the electrical panel and the
drivers.
It is important to keep the electric panel air intake filter free from dust and other impurities, furthermore it must be
regularly cleaned.
NOTE!-
With low temperatures, the electric panel fan will remain OFF.