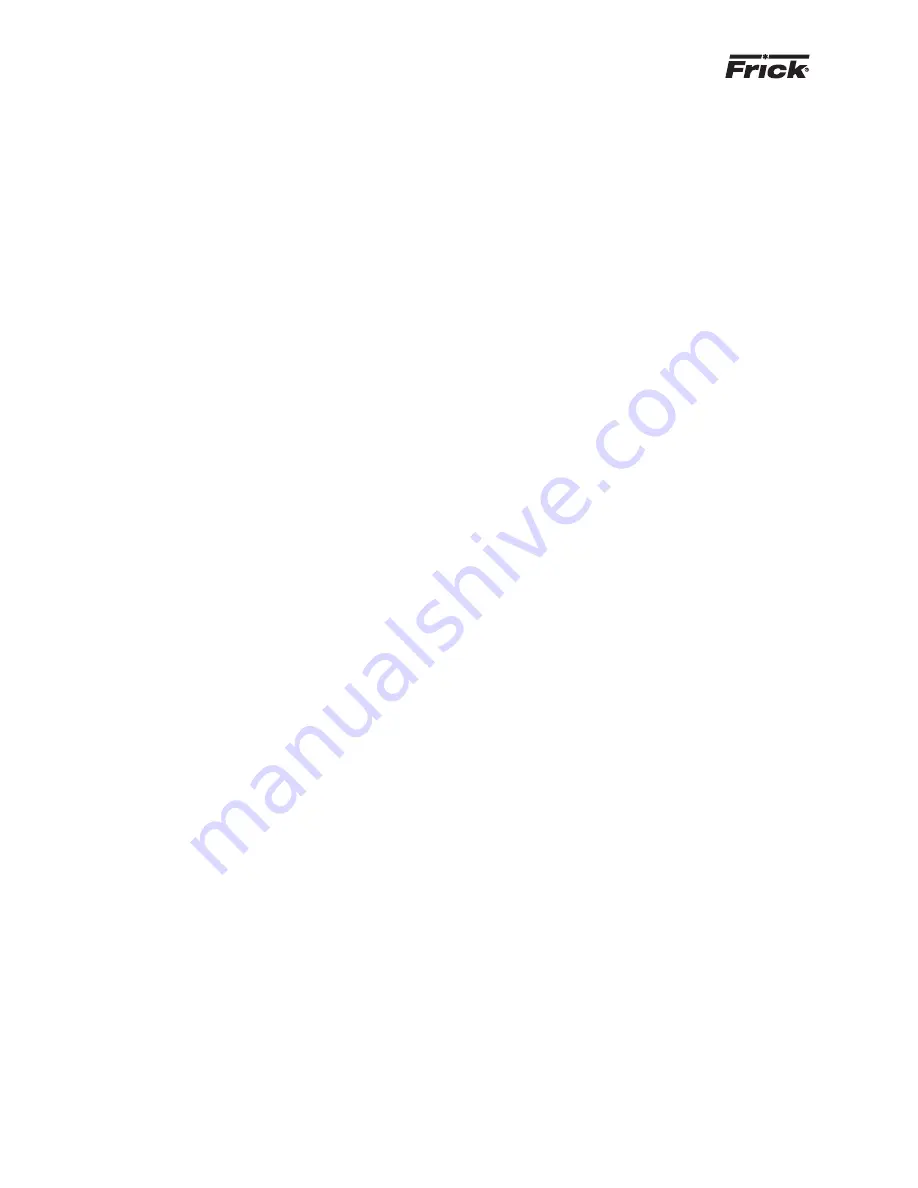
RWF ROTARY SCREW COMPRESSOR UNITS
MAINTENANCE
S70-600 IOM
Page 48
RWF COMPRESSOR PRESTART CHECKLIST
The following items MUST be checked and completed by the installer prior to the arrival of the
Frick Field Service Supervisor. Details on the checklist can be found in this manual. Certain items
on this checklist will be reverified by the Frick Field Service Supervisor prior to the actual start-up.
Mechanical Checks
__ Confirm that motor disconnect is open
__ Isolate suction pressure transducer
__ Pressure test and leak check unit
__ Evacuate unit
__ Remove motor tunnel cover
__ Remove coupling center and do not reinstall
__ Check for correct position of all hand, stop, and check
valves prior to charging unit with oil or refrigerant
__ Charge unit with correct type and quantity of oil
__ Lubricate motor bearings (if applicable)
__ Check oil pump alignment (if applicable)
__ Check for correct economizer piping (if applicable)
__ Check separate source of liquid refrigerant supply (if
applicable, liquid injection oil cooling)
__ Check water supply for water-cooled oil cooler (if appli-
cable, water cooled oil cooling)
__ Check thermosyphon receiver refrigerant level (if appli-
cable, thermosyphon oil cooling)
Electrical Checks
__ Confirm that main disconnect to motor starter and mi-
cro is open
__ Confirm that electrical contractor has seen this sheet,
all pertinent wiring information, and drawings
__ Confirm proper power supply to the starter package
__ Confirm proper motor protection (breaker sizing)
__ Confirm that all wiring used is stranded copper and is
14 AWG or larger (sized properly)
__ Confirm all 120 volt control wiring is run in a separate
conduit from all high voltage wiring
__ Confirm all 120 volt control wiring is run in a separate
conduit from oil pump and compressor motor wiring
__ Confirm no high voltage wiring enters the micro panel
at any point
__ Check current transformer for correct sizing and instal-
lation
__ Check all point-to-point wiring between the micro and
motor starter
__ Confirm all interconnections between micro, motor
starter, and the system are made and are correct
After the above items have been checked and verified:
__ Close the main disconnect from the main power supply to the motor starter
__ Close the motor starter disconnect to energize the micro
__ Manually energize oil pump and check oil pump motor rotation
__ Manually energize compressor drive motor and check motor rotation
__ Leave micro energized to ensure oil heaters are on and oil temperature is correct for start-up
Summary: The Frick Field Service Supervisor should arrive to find the above items completed.
He should find an uncoupled compressor drive unit (to verify motor rotation) and energized oil
heaters with the oil at the proper standby temperatures. Full compliance with the above items
will contribute to a quick, efficient and smooth start-up.
The Start-up Supervisor will:
1. Verify position of all valves
2. Verify all wiring connections
3. Verify compressor driver rotation
4. Verify oil pump motor rotation
5. Verify the % of FLA on the micro display
6. Verify and finalize alignment
7. Calibrate slide valve and slide stop
8. Calibrate temperature and pressure readings
9. Correct any problem in the package
10. Instruct operation personnel
Note: Customer connections are to be made per the electrical diagram for the motor starter
listed under the installation section and per the wiring diagram found in Frick publication
S90-010 M.
Sign this form & fax to 717-762-2422
Signed:
___________________________________
to confirm completion.
Print Name:
___________________________________
Company:
___________________________________
Summary of Contents for RWF
Page 37: ...RWF ROTARY SCREW COMPRESSOR UNITS MAINTENANCE S70 600 IOM Page 37 P I DIAGRAM ...
Page 47: ...RWF ROTARY SCREW COMPRESSOR UNITS MAINTENANCE S70 600 IOM Page 47 OPERATING LOG SHEET ...
Page 53: ...RWF ROTARY SCREW COMPRESSOR UNITS MAINTENANCE S70 600 IOM Page 53 ...
Page 54: ...RWF ROTARY SCREW COMPRESSOR UNITS MAINTENANCE S70 600 IOM Page 54 ...
Page 55: ...RWF ROTARY SCREW COMPRESSOR UNITS MAINTENANCE S70 600 IOM Page 55 ...