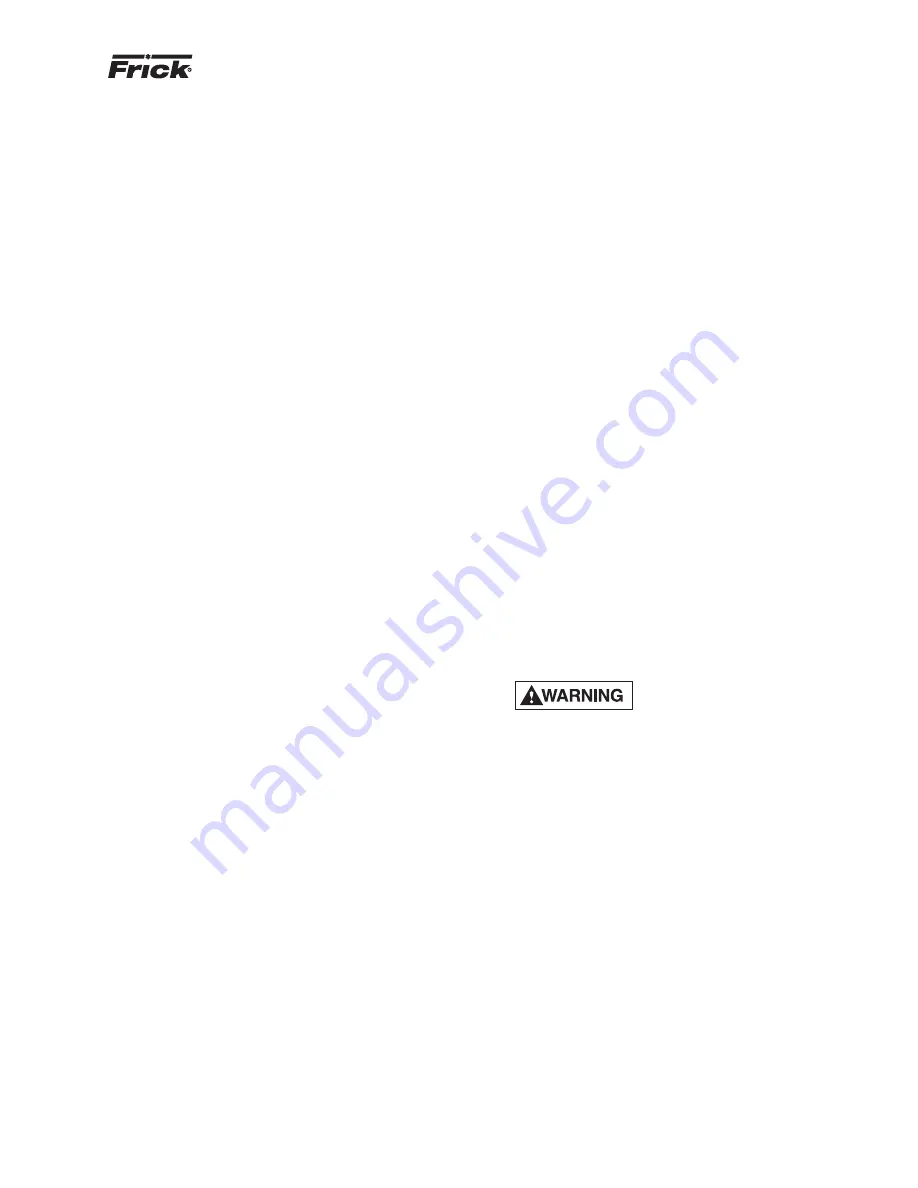
RWF ROTARY SCREW COMPRESSOR UNITS
MAINTENANCE
S70-600 IOM
Page 27
PRESSURE TRANSDUCERS - TESTING
1. Shut down the compressor and allow pressures to
equalize.
2. Isolate suction transducer PE-4 from the unit and de-
pressurize. NOTE: Recover or transfer all refrigerant va-
por, in accordance with local ordinances, before open-
ing to atmosphere.
3. Measure the voltage of PE-4 on connector P4 (termi-
nals WHT and BLK) on the SBC with a digital voltmeter.
4. The voltage reading should be 1.48 VDC to 1.72 VDC at
standard atmospheric pressure (14.7 PSIA or 0 PSIG). When
checking transducers at higher elevations, an allowance in
the readings must be made by subtracting approximately
0.02 VDC per 1000 feet of elevation above sea level. There-
fore, if PE-4 is measured at 5000 feet elevation under rela-
tively normal weather conditions, the output voltage should
differ by 0.10 VDC to read between 1.38 VDC and 1.62 VDC.
5. Isolate the oil pressure transducer PE-1 from the pack-
age and open it to atmosphere.
TROUBLESHOOTING GUIDE
Successful problem solving requires an organized approach
to define the problem, identify the cause, and make the
proper correction. Sometimes it is possible that two rela-
tively obvious problems combine to provide a set of symp-
toms that can mislead the troubleshooter. Be aware of this
possibility and avoid solving the “wrong problem”.
ABNORMAL OPERATION
ANALYSIS and CORRECTION
Four logical steps are required to analyze an operational
problem effectively and make the necessary corrections:
1. Define the problem and its limits.
2. Identify all possible causes.
3. Test each cause until the source of the problem is found.
4. Make the necessary corrections.
The first step in effective problem solving is to define the
limits of the problem. If, for example, the compressor peri-
odically experiences high oil temperatures, do not rely on
this observation alone to help identify the problem. On the
basis of this information the apparent corrective measure
would appear to be a readjustment of the liquid injection
system. Lowering the equalizing pressure on the thermal
expansion valve would increase the refrigerant feed and the
oil temperature should drop.
If the high oil temperature was the result of high suction
superheat, however, and not just a matter of improper liquid
injection adjustment, increasing the liquid feed could lead
to other problems. Under low load conditions the liquid in-
jection system may have a tendency to overfeed. The high
suction superheat condition, moreover, may only be tempo-
rary. When system conditions return to normal the units’ liq-
uid injection will overfeed and oil temperature will drop. In
solving the wrong problem a new problem was created.
When an operating problem develops compare all operat-
ing information on the MAIN OPERATING SCREEN with nor-
mal operating conditions. If an Operating Log has been main-
tained the log can help determine what constitutes normal
operation for the compressor unit in that particular system.
The following list of abnormal system conditions can cause
abnormal operation of the RWF compressor unit:
1. Insufficient or excessive refrigeration load.
2. Excessively high suction pressure.
3. Excessively high suction superheat.
4. Excessively high discharge pressure.
5. Inadequate refrigerant charge or low receiver level.
6. Excessively high or low temperature coolant to the oil
cooler.
7. Liquid return from system (slugging).
8. Refrigerant underfeed or overfeed to evaporators.
9. Blocked tubes in water cooled oil cooler from high min-
eral content of water.
10. Insufficient evaporator or condenser sizing.
11. Incorrect refrigerant line sizing.
12. Improper system piping.
13. Problems in electrical service to compressor unit.
14. Air and moisture present in the system.
Make a list of all deviations from normal plant operation and
normal compressor unit operation. Delete any items which
do not relate to the symptom and separately list those items
that might relate to the symptom. Use the list as a guide to
further investigate the problem.
The second step in problem solving is to decide which items
on the list are possible causes and which items are addi-
tional symptoms. High discharge temperature and high oil
temperature readings on a display may both be symptoms
of a problem and not casually related. High suction super-
heat or a low receiver level, however, could cause both
symptoms.
The third step is to identify the most likely cause and take
action to correct the problem. If the symptoms are not re-
lieved move to the next item on the list and repeat the pro-
cedure until you have identified the cause of the problem.
Once the cause has been identified and confirmed make
the necessary corrections.
SERVICING THE COLD-START VALVE
DO NOT ATTEMPT TO SERVICE THE
COLD START VALVE. PLEASE CON-
TACT THE FRICK SERVICE DE-
PARTMENT.
Summary of Contents for RWF
Page 37: ...RWF ROTARY SCREW COMPRESSOR UNITS MAINTENANCE S70 600 IOM Page 37 P I DIAGRAM ...
Page 47: ...RWF ROTARY SCREW COMPRESSOR UNITS MAINTENANCE S70 600 IOM Page 47 OPERATING LOG SHEET ...
Page 53: ...RWF ROTARY SCREW COMPRESSOR UNITS MAINTENANCE S70 600 IOM Page 53 ...
Page 54: ...RWF ROTARY SCREW COMPRESSOR UNITS MAINTENANCE S70 600 IOM Page 54 ...
Page 55: ...RWF ROTARY SCREW COMPRESSOR UNITS MAINTENANCE S70 600 IOM Page 55 ...