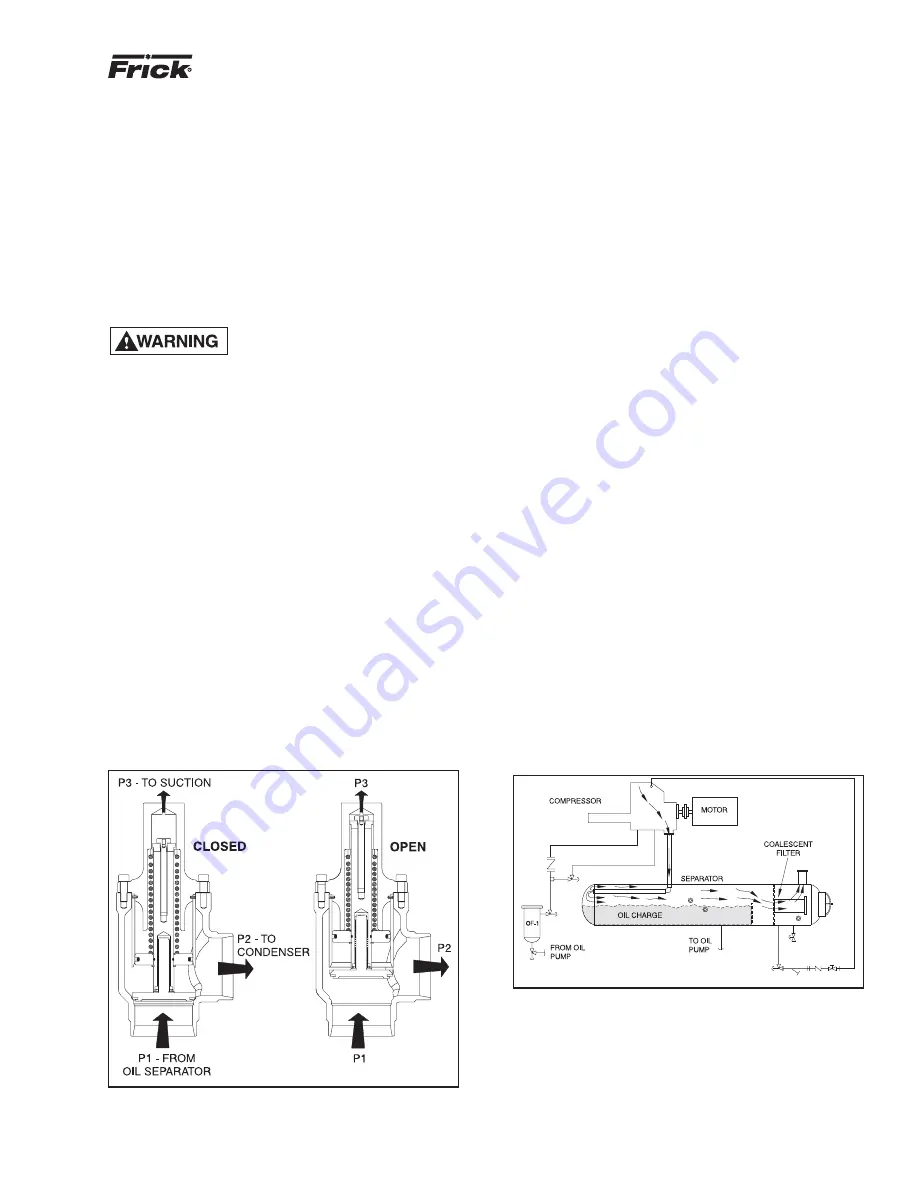
RWF ROTARY SCREW COMPRESSOR UNITS
OPERATION
S70-600 IOM
Page 13
COLD-START SYSTEM
The RWF package is equipped with a special "cold start"
discharge check valve (see Figure 13) on the gas outlet
connection of the oil separator. This valve causes the oil
separator to develop oil pressure rapidly on initial start in
order to lubricate the compressor without requiring an oil
pump, even in cold ambient temperatures with all pres-
sures equalized.
For high-stage packages, the cold-start valve is equipped
with a large spring that creates 30 psi of pressure in the oil
separator (above suction pressure), for lubrication of the
compressor.
DO NOT ATTEMPT TO SERVICE THE
COLD START VALVE. PLEASE CON-
TACT THE FRICK SERVICE
DEPARTMENT.
Once the compressor is running it will begin to force gas to
the condenser at connection P2. As the condenser heats
up it will begin to rise in pressure as the compressor suction
pulls down in pressure. As soon as differential pressure is
developed between the condenser and suction, these pres-
sures act across a piston inside the cold-start valve to par-
tially overcome the spring force. When the differential pres-
sure reaches and exceeds 30 psi, the piston fully over-
comes the spring force and powers the valve fully open for
very low operating pressure drop.
For booster applications, the valve is equipped with a lighter
spring which produces 15 psi oil pressure above suction
pressure before it fully powers open.
The RWF package is also equipped with a suction check
valve bypass. The oil separator will slowly bleed down to
system suction pressure when the unit is stopped. This al-
lows the compressor drive motor to have an easier start,
and the discharge check valve will seat more tightly. See
the "SUCTION CHECK VALVE BYPASS" section for
operation.
NOTE: For alarm descriptions and shutdown or cutout
parameters, see publication S90-010 O.
DEMAND PUMP OIL SYSTEM
This system is designed to provide adequate compressor
lubrication for some high stage applications that operate with
low differential pressure across the compressor suction and
discharge and all booster applications.
During the period from start-up to normal operation the oil
pressure alarm and oil pressure cutout setpoints will vary
according to formulas built into the microprocessor control
program.
NOTE: For alarm descriptions and shutdown or cutout
parameters, see publication S90-010 O.
COMPRESSOR OIL SEPARATION SYSTEM
The RWF is an oil flooded screw compressor. Most of the oil
discharged by the compressor separates from the gas flow
in the oil charge reservoir. Some oil, however, is discharged
as a mist which does not separate readily from the gas flow
and is carried past the oil charge reservoir. One or more
coalescer filter elements then COALESCE the oil mist into
droplets which fall to the bottom of the coalescer section of
the oil separator (see Figure 14). The return of this oil to the
compressor is controlled by a throttling valve on both high
stage and booster applications.
NOTE: Open throttling valve only enough to keep coa-
lescer end of separator free of oil.
The sight glass located near the bottom of the coalescer
section of the oil separator should remain empty during nor-
mal operation. If an oil level develops and remains in the
sight glass, a problem in the oil return separation system or
compressor operation has developed. Refer to MAINTE-
NANCE for information on how to correct the problem.
NOTE: The normal charging level is midway in the top
sight glass located midway along the oil separator shell.
OIL SEPARATION SYSTEMS
HORIZONTAL, MODELS 100 - 480
Figure 13 - Cold Start Valve
Figure 14
Summary of Contents for RWF
Page 37: ...RWF ROTARY SCREW COMPRESSOR UNITS MAINTENANCE S70 600 IOM Page 37 P I DIAGRAM ...
Page 47: ...RWF ROTARY SCREW COMPRESSOR UNITS MAINTENANCE S70 600 IOM Page 47 OPERATING LOG SHEET ...
Page 53: ...RWF ROTARY SCREW COMPRESSOR UNITS MAINTENANCE S70 600 IOM Page 53 ...
Page 54: ...RWF ROTARY SCREW COMPRESSOR UNITS MAINTENANCE S70 600 IOM Page 54 ...
Page 55: ...RWF ROTARY SCREW COMPRESSOR UNITS MAINTENANCE S70 600 IOM Page 55 ...