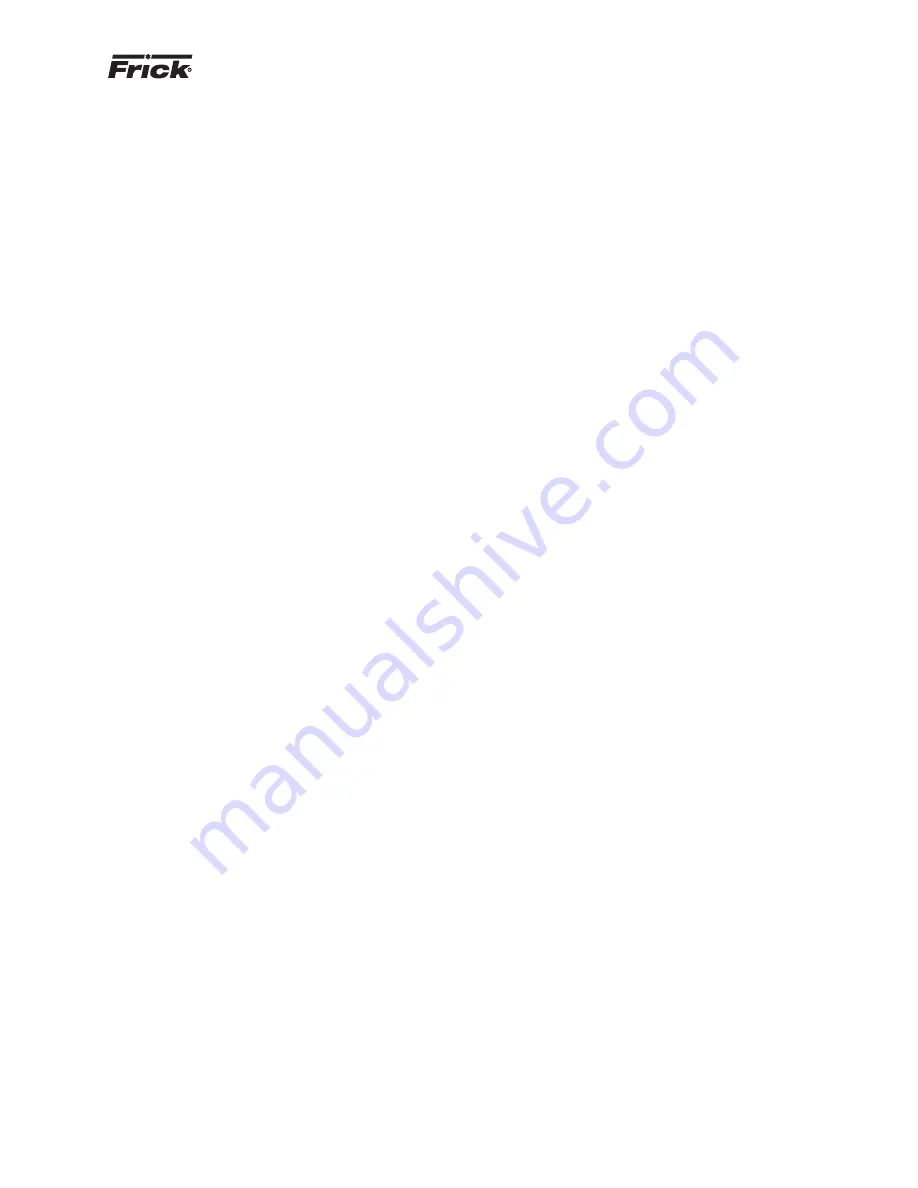
RWF ROTARY SCREW COMPRESSOR UNITS
OPERATION
S70-600 IOM
Page 17
INITIAL START-UP
Initial start-up must be performed under the supervision
of a FRICK authorized start-up representative to pre-
vent voiding the compressor warranty. Prior to the
start-up, the prestart check must be accomplished.
INITIAL START-UP PROCEDURE
Having performed the checkpoints on the prestart check list
the compressor unit is ready for start-up. It is important that
an adequate refrigerant load be available to load test the
unit at normal operating conditions. The following points
should be kept in mind during initial start-up.
1. It is imperative that during the initial start-up of the
package that the hand expansion valve on the main oil
injection line is fully open to ensure adequate oil flow.
There is still an orifice installed in the compressor to control
maximum oil flow. At initial start-up of the package the hand
expansion valve must be fully open. After initial start-up of
the package the hand expansion valve should be adjusted.
There are two methods of determining the correct adjust-
ment of this valve.
The best method to determine target discharge tempera-
ture is to run CoolWare. Run CoolWare or ScrewSelect with
the operating conditions of the compressor. The program
will give you a theoretical discharge temperature of the
compressor. Once this temperature is known, you may ad-
just the hand expansion valve. The ideal discharge tem-
perature is within 5°F + or – of the theoretical discharge
temperature. Adjust the valve to achieve the theoretical dis-
charge temperature. If you do not have access to CoolWare
or ScrewSelect, 180°F is a good target discharge tempera-
ture for a high stage ammonia compressor. Booster appli-
cations and compressors using HFC and HCFC refriger-
ants may run cooler. Compressors with high discharge pres-
sure may run hotter.
The first method is used for compressors with External Oil
Cooling (Thermosyphon, Water Cooled, and Glycol
Cooled). Before the initial startup of the compressor close
the hand expansion valve completely. Open the valve back
up and count the turns that it takes to fully open the valve.
After the initial startup close the valve to achieve approxi-
mately 180° F discharge temperature or the theoretical tem-
perature from CoolWare. Do not fully close the valve at any
time while the compressor is running.
The second method is used for compressors with Liquid
Injection Oil Cooling. Because the discharge temperature
is controlled by the Liquid Injection Thermal Expansion Valve
you will not be able adjust for the correct oil flow by using
the discharge temperature. Before the initial startup of the
compressor close the hand expansion valve completely.
Open the valve back up and count the turns that it takes to
fully open the valve. After the initial startup close the valve
½ way. If it took 10 turns to open the valve completely, then
turn it in 5 turns. If it took 7 turns to open, then close the valve
3 ½ turns. Do not close the valve any further than ½ the
number of turns required to fully open it.
Failure to properly adjust this valve can lead to excessive
noise and vibration of the compressor and package, pre-
mature failure of the bearings, liquid loading of the rotors,
liquid starvation of the rotors and catastrophic failure of the
compressor.
2. For proper and safe operation, the compressor must be
run at the proper speed and discharge pressure. Exceed-
ing design conditions creates a potential hazard.
3. Rotate and lubricate motor bearings according to
manufacturer’s recommendations PRIOR to start-up as re-
quired.
4. After running the unit for approximately three hours, ad-
just liquid injection oil cooling if applicable. If unit has water
cooled oil cooling, adjust water control valve to cooler.
5. The compressor slide valve and slide stop linear trans-
mitters should be calibrated.
6. Pull and clean suction strainer after 24 hours of opera-
tion. If it is excessively dirty, repeat every 24 hours until
system is clean. Otherwise, follow the normal MAINTE-
NANCE SCHEDULE.
7. Perform vibration analysis if equipment is available.
NORMAL START-UP PROCEDURE
1. Confirm system conditions permit starting the compressor.
2. Press the [RUN] key.
3. Allow the compressor to start-up and stabilize. Press the
[AUTO] key immediately below the V ratio label on the op-
erating display screen. Press the [AUTO] key immediately
below the SV POS label on the operating display. The
compressor is now operating in the automatic mode.
4. Observe the compressor unit for mechanical tightness of
the external piping, bolts and valves. Ensure that the ma-
chine is clean from oil and refrigerant leaks. If any of these
occur, shut down the compressor and correct the problem
as necessary using good safety precautions.
5. RETIGHTEN MANWAY BOLTS at condenser design pres-
sure (while system is running).
RESTARTING COMPRESSOR UNIT AFTER CONTROL
POWER INTERRUPTION (PLANT POWER FAILURE)
1. Check variable setpoints.
2. Follow normal start-up procedure.
Summary of Contents for RWF
Page 37: ...RWF ROTARY SCREW COMPRESSOR UNITS MAINTENANCE S70 600 IOM Page 37 P I DIAGRAM ...
Page 47: ...RWF ROTARY SCREW COMPRESSOR UNITS MAINTENANCE S70 600 IOM Page 47 OPERATING LOG SHEET ...
Page 53: ...RWF ROTARY SCREW COMPRESSOR UNITS MAINTENANCE S70 600 IOM Page 53 ...
Page 54: ...RWF ROTARY SCREW COMPRESSOR UNITS MAINTENANCE S70 600 IOM Page 54 ...
Page 55: ...RWF ROTARY SCREW COMPRESSOR UNITS MAINTENANCE S70 600 IOM Page 55 ...