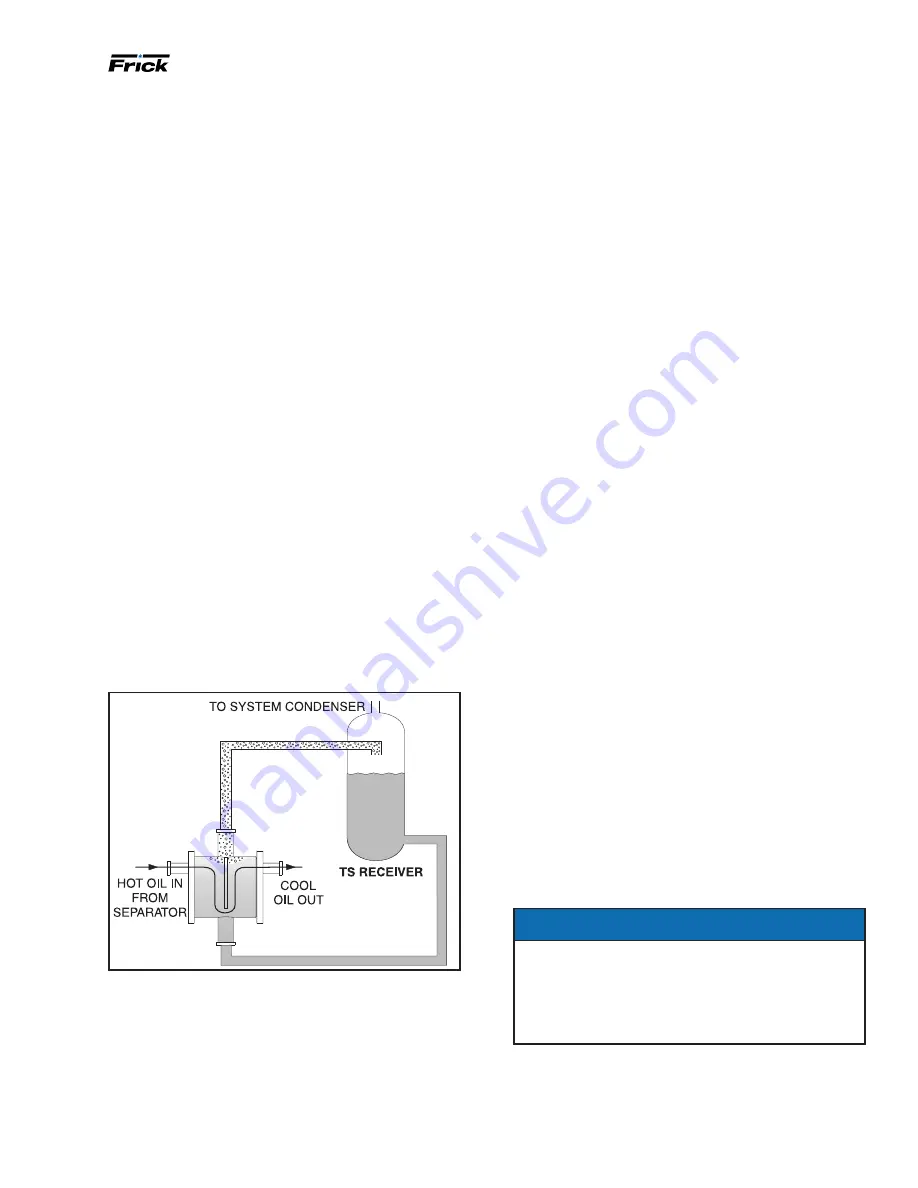
HPS Rotary Screw Compressor Units
070.700-IOM (MAR 21)
Page 9
Installation
System operation
Liquid refrigerant fills the cooler shell-side up to the Ther
-
mosyphon receiver liquid level.
Hot oil (above the liquid temperature) flowing through the
cooler causes some of the refrigerant to boil and vapor
-
ize. The vapor rises in the return line. The density of the
refrigerant liquid/vapor mixture in the return line is con
-
siderably less than the density of the liquid in the supply
line. This imbalance provides a differential pressure that
sustains a flow condi tion to the oil cooler. This relationship
involves:
•
Liquid height above the cooler.
• Oil heat of rejection.
•
Cooler size and piping pressure drops.
The liquid/vapor returned from the cooler is separated in
the receiver. The vapor is vented to the condenser inlet and
need only be reliquified because it is still at condenser pres
-
sure (see
Oil temperature control
Oil temperature generally runs about 15°F to 35°F (8.3°C
to 19.4°C) above
the high-side condensing tempera ture. In
many cases, oil cooling is not required due to the low heat
of compression for CO
2
applications:
•
High-side
65°F to 105°F
condensing temperature:
(18.3
°C to 40.6°C)
•
CO2 discharge
80°F to 140°F
temperature
:
(26.7°C to 60°C)
Installation
The welded plate-type thermosyphon oil cooler with oil-
side piping and a thermostatically controlled mixing valve
are factory mount ed and piped. The customer must supply
and install all piping and equip ment located outside of
the shaded area on the piping diagram with consideration
given to the following:
•
Ensure the refrigerant source, thermosyphon or system
receiv er, is in close proximity to the unit to minimize
piping pressure drop.
• The
liquid level in the refrigerant source must be a
minimum calculated height above the center of the oil
cooler.
• Install a safety valve if
using refrigerant isolation valves
for the oil cooler.
Notice
The component and piping arrangement shown in
the following figure is intended only to illustrate the
operating principles of thermosyphon oil cooling. Other
component layouts may be better suited to a specific
installation. Refer to publication
070.900-E
for addi-
tional information on Thermosyphon Oil Cooling.
Thermosyphon oil cooling (TSOC)
The refrigerant for TSOC (on a high pressure package) is
piped from the high side of the cascade system. Ther
-
mosyphon oil cooling is an economical, effective method
for cooling oil on screw compressor units. Ther mosyphon
cooling uses liquid refrigerant at condenser pressure and
temperature that is partially vaporized at the condenser
temperature in a plate and shell vessel, cooling the oil to
within 35°F (19.4°C) of that temperature. The vapor, at
condensing pressure, is vented to the
condenser inlet and
reliquified. This method is the most cost-effective of all
currently applied cooling systems because no compres sor
capacity is lost or compressor power penalties in curred.
The vapor from the cooler need only be con densed, not
compressed. Refrigerant flow to the cooler is automatic,
driven by the thermosyphon principle and cooling flow
increases as the oil inlet temperature rises.
Equipment
The basic equipment required for a ther mosyphon system
consists of the following components:
•
A source of liquid refrigerant at condensing pressure
and temperature, located in close proximity to the unit
to mini mize piping pressure drop. The liquid level in the
refrigerant source must be a minimum calculated height
above the center of the oil cooler.
• A
plate and shell oil cooler with:
–
Plate side: Oil 1000 psig (6894.8 kPa) design
–
Shell side: Refrigerant 1000 psig (6894.8 kPa) design
Due to the many variations in refrigeration system design
and physical layout, several systems for ensuring the
above criteria are possible.
Figure 9: Condenser/Receiver
Note:
Example using ammonia as the high-side refrigerant
95°F (35°C)
2.5 lb/ft
3
95°F
(35°C)
36 lb/ft
3