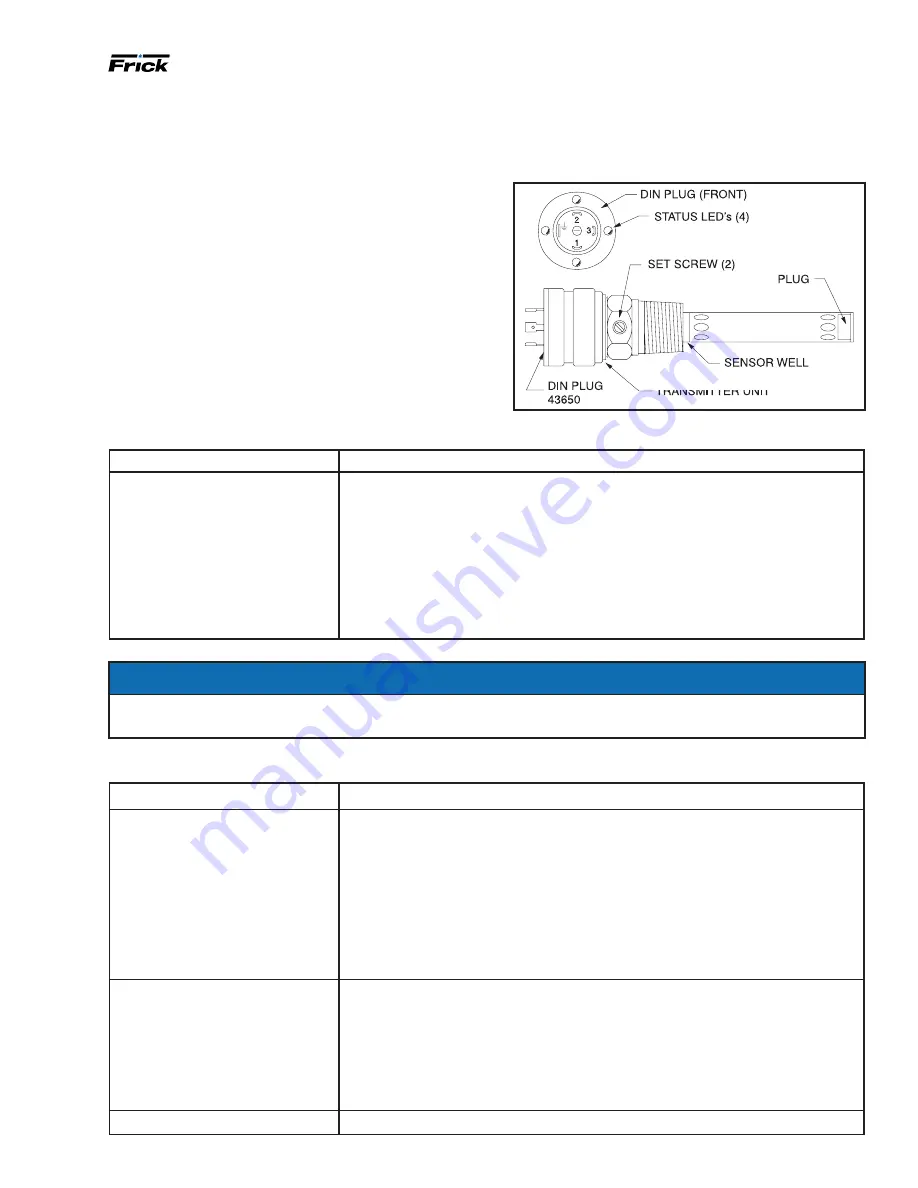
HPS Rotary Screw Compressor Units
070.700-IOM (MAR 21)
Page 39
Maintenance
Troubleshooting the HPS Compressor unit
Symptom
Probable causes and corrections
Excessive noise and vibration
Main oil injection valve may be closed. Open valve.
Main oil injection valve may be open too far. Adjust.
Bearing damage or excessive wear. Contact Frick Factor or Frick service.
Coupling loose on shaft. Tighten coupling. Replace if damaged.
If motor or compressor have been reinstalled, check that installation done according
to
070.660-SM
Refrigerant flood-back. Correct system problem.
Notice
Troubleshooting the compressor is limited to identifying the probable cause. If a mechanical problem is suspected
contact the Service Department. Do not attempt to disassemble the compressor.
Replacement
The oil level switch is located on the front of the separator
near the bottom/center. See
The operation of the switch is based on the capacitive
measuring principle. It features removable electronics
(from the sensor well) eliminating the need to evacuate
the package for replacement. This switch is dedicated to
oil level control and has no user adjustments.
1. Shut off control power
2.
Remove the DIN connector plug from the transmitter
3. Loosen the set screws
4. Remove the electronic switch head
5. Install the new electronic switch head
6.
Tighten the set screws
7.
Apply the DIN connector plug to the electronic switch
head
8. Turn on control power
Figure 40: Oil level switch
ELECTRONIC HEAD
Troubleshooting the oil separation system
Symptom
Probable causes and corrections
Gradual oil loss with an oil
Level in the coalescer
Section sight glass
Maintaining too high an oil level, lower level.
Refrigerant carryover or liquid injection overfeed ing, correct operation.
Loss of suction superheat. Adjust evaporator feeds.
Contaminated oil, damaged or not seated coalescer filter elements. Replace
oil charge and coalescers.
Coalescer return valve closed. Open return valve.
Coalescing oil return line strainer blocked. Clean.
Rapid loss with no oil level
In the coalescer section
Sight glass
On shutdown, compressor unit suction check valve did not close. Repair valve.
Suction check valve bypass valve open too far to meter flow. Close valve.
Coalescers loose or not seated correctly. Correct or replace.
On economized unit: economizer check valve not working. Repair or replace.
Economizer check valve not in automatic position or manually opened. Place in auto
position.
Shaft seal leakage
If leakage exceeds normal allowable rate of 7 drops a minute, replace seal.