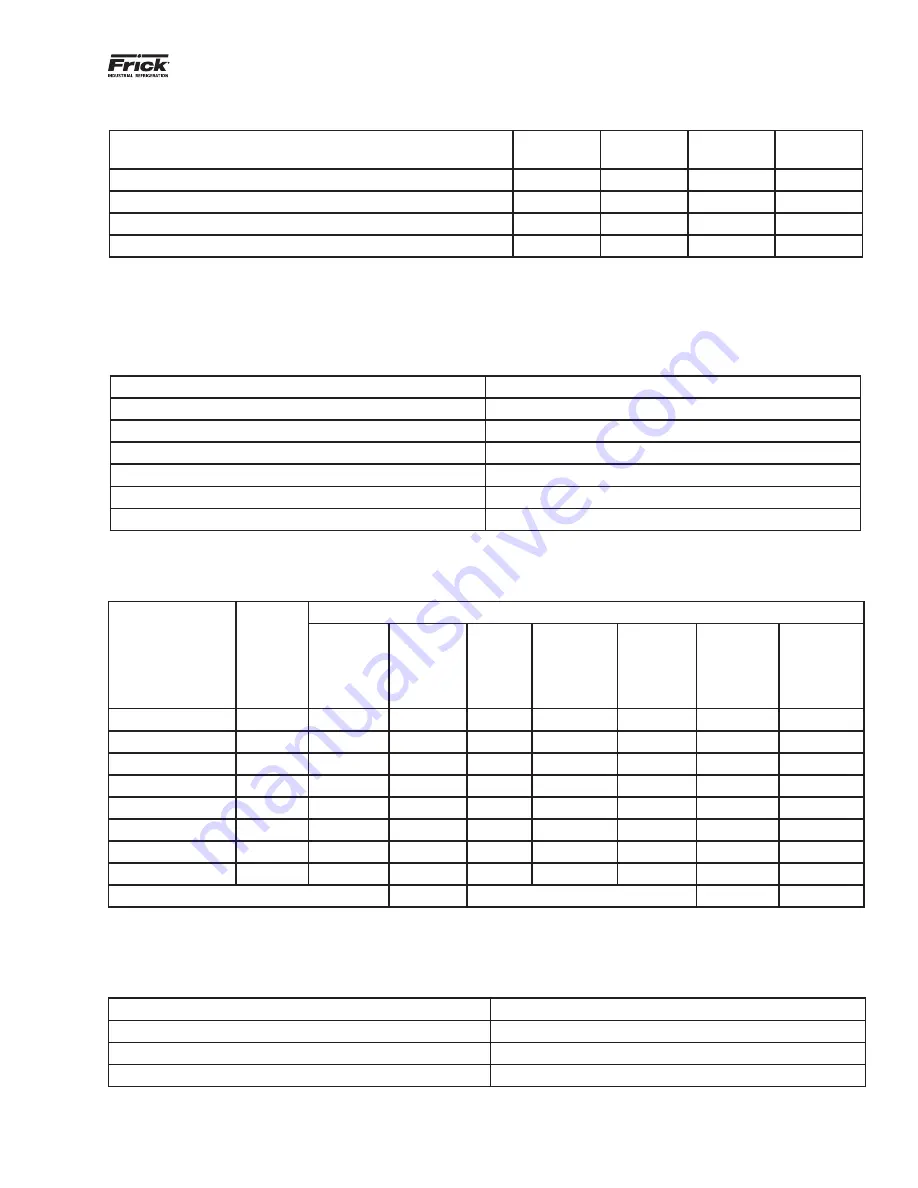
610.020-IOM (NOV 19)
Page 9
EVAPORATOR AND AIR COOLER
INSTALLATION - OPERATION - MAINTENANCE
Table 3: Defrost types based on room temperature
Temperature
Air
defrost
Water
defrost
Electric
defrost
Hot gas
defrost
High temperature > 40°F (4.4°C)
Yes
No
No
No
Medium temperature > 20°F (-6.7°C) < 40°F (4.4°C)
No
Yes
Yes
Yes
Low temperature < 20°F (-6.7°C)
No
Yes
Yes
Yes
Ultra low temperature < -40°F (-40°C)
No
No
Yes
Yes
Note:
Insulated pans are recommended for any application with a room temperature below freezing.
Table 4: Hot gas pressures at the evaporator
Refrigerant
Required pressure at evaporator, psig (bar)
R22
90 to 110 (~6 to 7.5)
R404a
115 to 140 (~8 to 9.5)
R507A
115 to 140 (~8 to 9.5)
R134a
50 to 65 (~3.5 to 4.5)
R410a
155 to 185 (~10.5 to 12.5)
NH
3
80 to 100 (~5.5 to 7)
Table 5: Hot gas defrost - sequence of operation
Defrost stages
Time in
minutes
(approx.)
Control Valves
Liquid
solenoid
(LSV)
Suction
solenoid
(SSV)
Delay
Soft hot
gas sole-
noid valve
(SHGSV)
Hot gas
solenoid
valve
(HGSV)
Bleed sole-
noid valve
(BSV)
Fan motor/
motors
running
Refrigeration mode xx
—
—
yes
Pump out period
10 - 30
—
yes
Delay
5 s - 10 s
—
no
Soft gas period
1 - 2
—
—
no
Hot gas period
5 - 30
—
no
Equalizing period
2 - 5
—
no
Fan delay period
1 - 3
—
—
no
Refrigeration mode xx
—
—
yes
=
Solenoid open
Table 6: Wattages for electric defrost
Temperature range
Wattage per ft
2
of coil surface area
Medium temperature > 20°F (-6.7°C) < 40°F (4.4°C)
6 to 8
Low temperature < 20°F (-6.7°C)
8 to 12
Ultra low temperature < -40°F (-40°C)
12 to 15