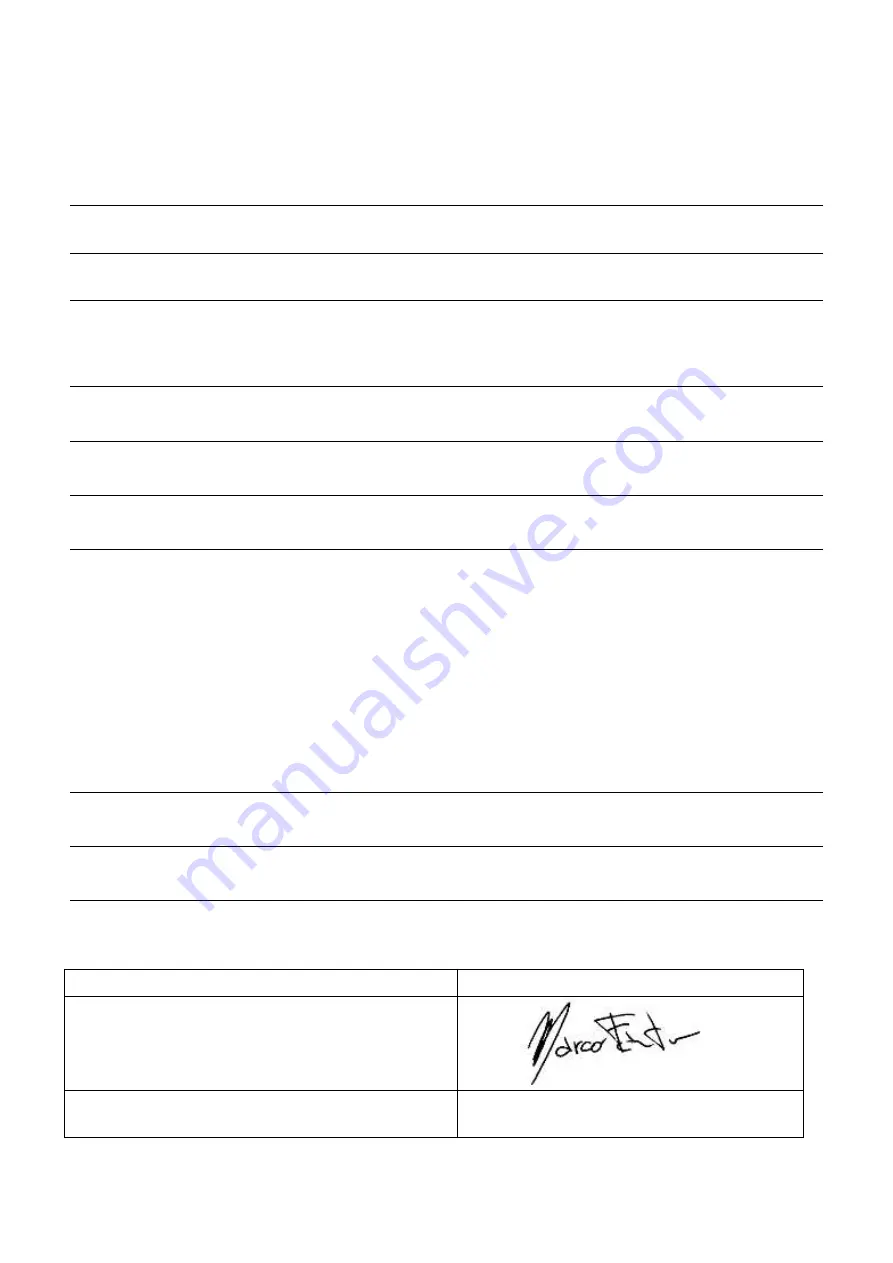
FRANCO srl Manual of use and maintenance UCP-fly
12
1.15 Declaration of conformity
(Att. IIa DIR. 2006/42/CE)
THE MANUFACTURER
FRANCO S.r.l.
Company
Via Nazionale, 80
12010
CN
Address
Postal code
Province
Cervasca
Italy
City
Country
DECLARES THAT THE MACHINE
Cooler / Humidifier
UCPfly H15 / UCPfly H20 / UCPfly H25
Description
Model
3108000 / 3108100 / 3108200 / 3108300 / 3108400 / 3108500
2018
Series/Registration number
Year of construction.
UCP - fly Cooler / Humidifier
Commercial denomination
Humidification and/or cooling of environments
Intended use
Meets the following essential requirements:
RESS from 1.1 to 1.7
Complies with the EU directives:
Directive 2006/42/CE - Directive 2006/95/CE - Directive 2004/108/CE
Referring to harmonized norms:
EN 120100-1; EN 12100-2;EN 60204-1
AND AUTHORIZES
Marco Fantino
Name
Via Nazionale 80
12010
CN
Address
Postal code
Province
Cervasca
Italia
City
Country
TO COMPILE THE TECHNICAL FILE ON HIS BEHALF
Place and date of the document
The manufacturer
Cervasca, 10/05/2010
Firma
Function
Administrator
D.C.: DC N-001/310001