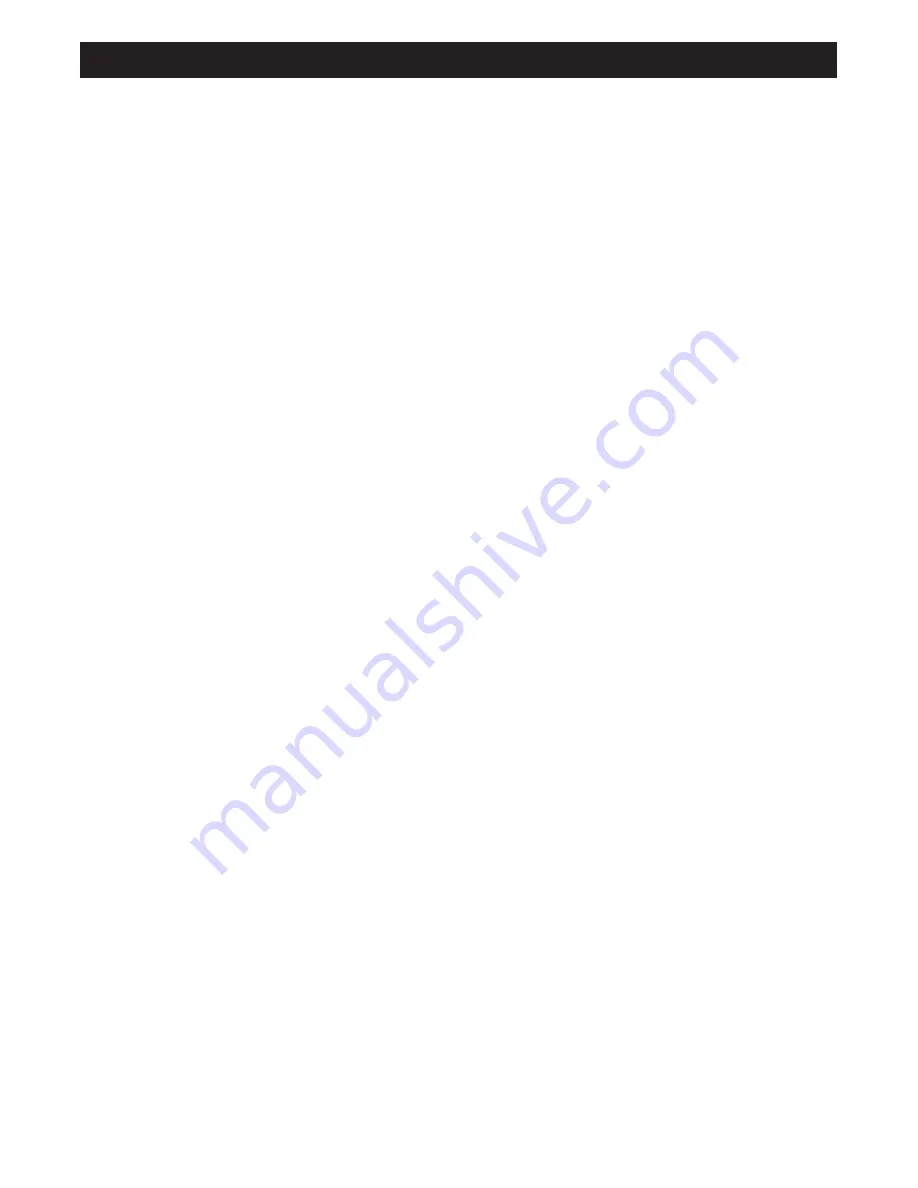
FIG #
01
OEM #
04600163
02
23005332
03
23005145
04
23005091
05
23005285
06
23005146
07
23005018
07
23005019
07
23005020
08
23005147
09
21200010
10
33800032
11
30900021
12
23005254
12A
30900002
13
22910001
13A
22910001
14
30900020
15
04600063
16
23005148
17
23005318
WIRE FEED WELDER GUN PARTS LIST
FORNEY #
DESCRIPTION
QTY
85296
HANDLE ASSY., BLUE
1
85190
GAS VALVE
1
85191
SWAN NECK WITH INSULATING COVER
1
85377
SWAN NECK LINER
1
85192
ISOLATING COVER FOR NECK
2
85295
TW1 TORCH DIFFUSER
1
60170
0.024 CONTACT TIP
1
60171
0.030 CONTACT TIP
1
60172
0.035 CONTACT TIP
1
85316
TORCH GAS NOZZLE
1
85313
FAST-ON CONTACT 6,3X0,8
1
85193
TORCH CONTACT SPRING
1
85194
RUBBER OUTER SLEEVE ø17,5 + HOSES
1
85317
STEEL LINER 1.4X4BLUE 2,2M W/END FITT
1
85195
PLASTIC WIRE LINER 1,5X4 2,5M
1
85307
FAST CONNECTION FOR HOSE ø4 M6X0,75
1
85307
END FITTING ø4 M6X0,75 FOR PLASTIC LIR
1
85195
TORCH GAS HOSE ø2X4 4,6M
1
85196
KIT 2 PINS MALE CON 2 CONT.
1
85376
NECK+OUTER INSDIFFUSER
1
85308
ALUMINIUM GAS VALVE + NECK + DIFF.
1
Summary of Contents for MIG 180FI
Page 31: ...w 0 4 1...
Page 33: ......
Page 34: ...32 y 5 3 2 J 6 7 I I I I I _ j B I 4 12 11...
Page 36: ...34 NOTES...
Page 37: ...I I S I N C E 1932...
Page 38: ...Forney Industries Inc 1 800 521 6038 www forneyind com...