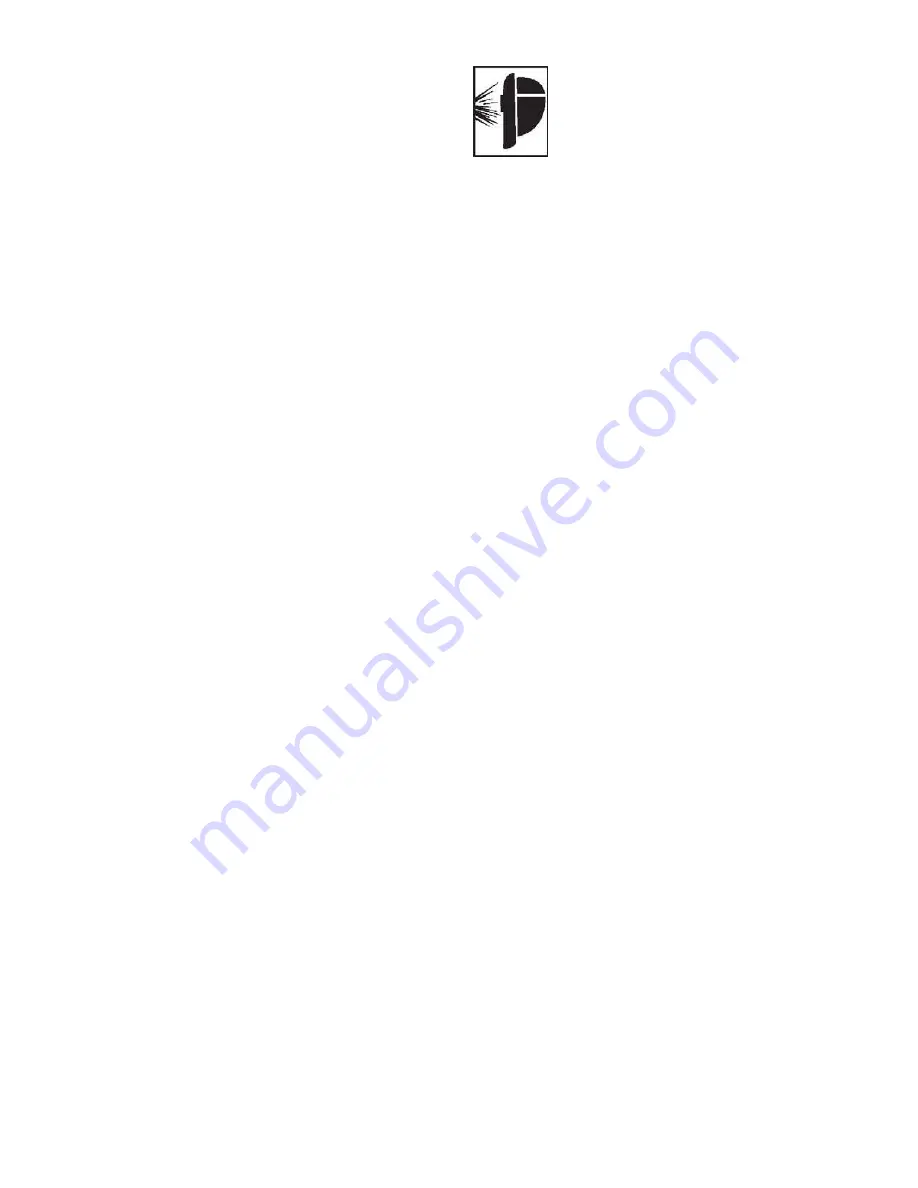
1
6
15. Connect the welder power cord to the ac
SET THE WIRE DRIVE TENSION
power source. Turn the welder ON by set-
ting the VOLTAGE switch to the voltage
(heat) setting recommended for the gauge
metal that is to be welded. Refer to the
label mounted on the cover, inside the
drive compartment, for recommended volt-
age (heat) settings for your welding job.
The VOLTAGE selector controls the weld
heat. There are six voltage heat selections
available on this welder. Placing the volt-
age switch in MIN position, and the voltage
dial in position 1 provides the lowest volt-
age (heat). Placing the voltage switch in
MAX position, and the voltage dial in posi-
tion 3 provides the highest voltage (heat).
16. Set the WIRE SPEED control to the middle
of the wire speed range.
17. Straighten the gun cable and pull the trig-
ger on the welding gun to feed the wire
through the gun assembly.
18. When at least an inch of wire sticks out
past the end of the gun, release the trigger.
19. Select a contact tip stamped with the same
diameter as the wire being used. If
stamped in metric see DESCRIPTION.
Note:
Due to inherent variances in flux-cored
welding wire, it may be necessary to use a
contact tip one size larger than your flux core
wire if wire jams occur.
20. Slide the contact tip over the wire (protrud-
ing from the end of the gun). Thread the
contact tip into the end of the gun and
hand-tighten securely.
21. Install the nozzle on the gun assembly. For
best results, coat the inside of the nozzle
with anti-stick spray or gel.
22. Cut off the excess wire that extends past
the end of the nozzle.
WARNING
Arc flash can injure your eyes!
To reduce
the risk of arc flash, make certain that the
wire coming out of the end of the gun does
not come in contact with work piece, ground
clamp or any grounded material during the
drive tension setting process or arcing will
occur.
1. Pull the trigger on the gun.
2. Turn the drive tension adjustment knob
clockwise, increasing the drive tension
until the wire seems to feed smoothly
without slipping.
When set correctly, there should be no slip-
page between the wire and the drive roller
under normal conditions. If an obstruction
occurs along the wire feed path, the wire
should then slip on the drive roller.
After the tension is properly adjusted, the
quick release drive tensioner may unlocked
and relocked and no radjustment of the drive
tension adjustment knob will be necessary
(unless the diameter or type of wire is
changed).
INSTALLING ALUMINIUM WIRE
Install aluminium wire the same as steel
wire, but with the following exceptions:
1. Install a plastic liner in the welding gun.
2. Adjust the drive tension VERY carefully.
Aluminium wire is very sensitive to slight
changes in drive tension.
Note:
For welding aluminium with this unit,
5356 alloy wire is recommended because of
its superior feedability. A plastic liner is need-
ed. When welding with softer aluminium
alloys, you may experience feed problems.
Summary of Contents for MIG 180FI
Page 31: ...w 0 4 1...
Page 33: ......
Page 34: ...32 y 5 3 2 J 6 7 I I I I I _ j B I 4 12 11...
Page 36: ...34 NOTES...
Page 37: ...I I S I N C E 1932...
Page 38: ...Forney Industries Inc 1 800 521 6038 www forneyind com...