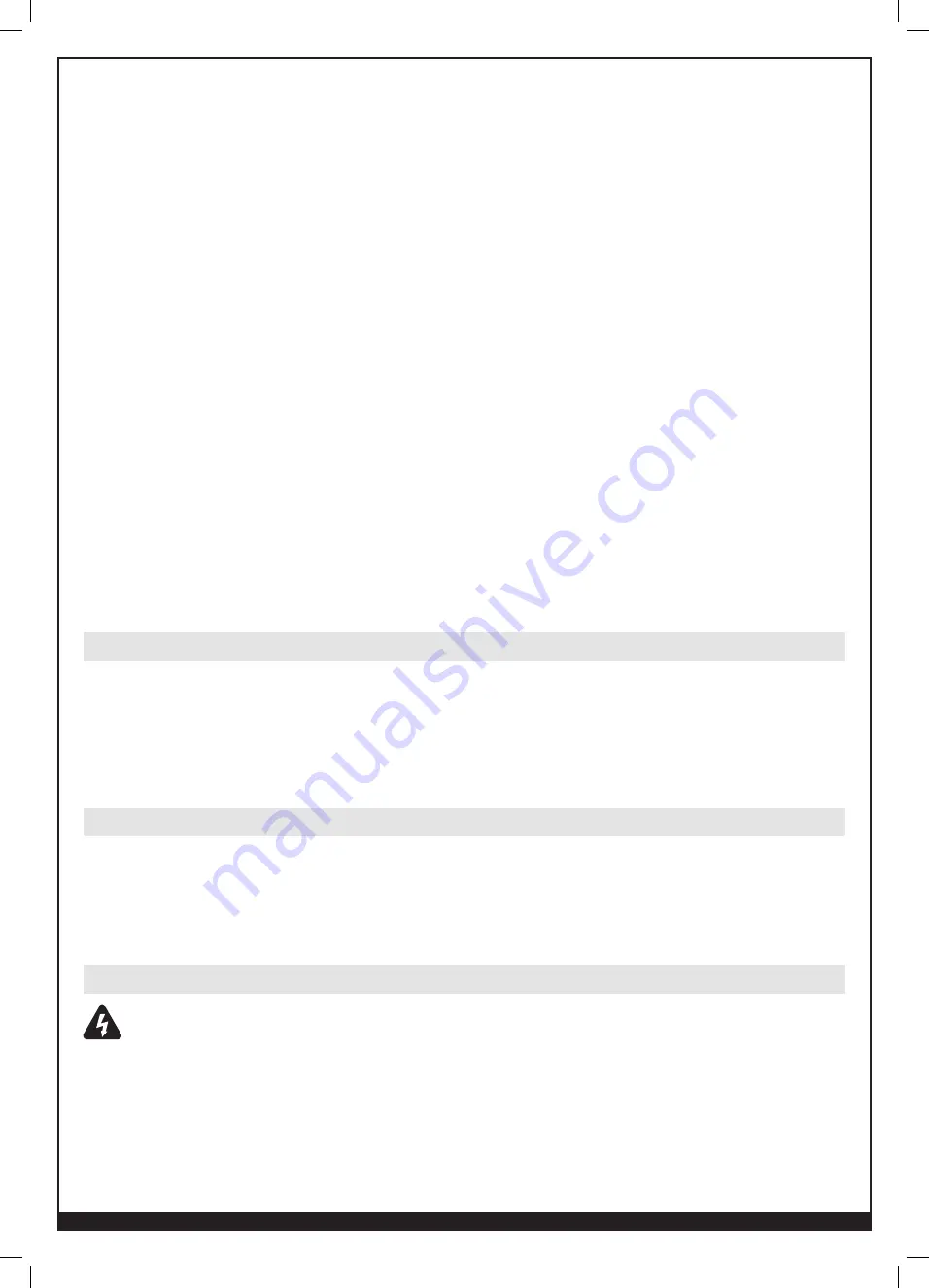
8
WWW.FORNEYIND.COM
pressure used. All hoses, fittings, etc. should be in good condition.
• Do not stand in front of or put your head or face in front of a cylinder valve outlet when opening the valve.
• If a cylinder is not in use or connected for use, keep a valve protection cap in place to protect the valve.
• Keep cylinders upright and securely chain them to a fixed support to prevent tipping.
• Keep cylinders away from areas where they may be subjected to physical damage or accidentally struck. Keep them
a safe distance from any source of flame, sparks, or heat.
• Do not weld or cut in an area where the air may contain flammable dust (such as grain dust), gas, or liquid vapors
(such as gasoline).
• Do not handle hot metal, such as the workpiece or electrode stubs, with bare hands.
• Wear leather gloves, heavy long sleeve shirt, cuffless pants, high-topped shoes, helmet, and cap. As necessary, use
additional fire-resistant protective clothing to cover and protect the upper and lower body. Hot sparks or metal can
lodge in rolled up sleeves, pant cuffs, or pockets. Sleeves and collars should be kept buttoned and pockets eliminated
from the shirt front.
• Have fire extinguisher equipment handy for immediate use. A portable chemical fire extinguisher, type ABC, is
recommended.
• Wear ear plugs when welding overhead to prevent spatter or slag from falling into ear.
• Make sure welding area has a good, solid, safe floor, preferably concrete or masonry, not tiled, carpeted, or made of
any other flammable material.
• Protect flammable walls, ceilings, and floors with heat resistant covers or shields.
• Check welding area to make sure it is free of sparks, glowing metal or slag, and flames before leaving the welding
area.
• Wear garments free of oil or other flammable substances such as leather gloves, thick cotton shirts with no synthetic
materials, cuffless trousers, closed toed shoes. Keep long hair pulled back.
• Remove any combustibles such as lighters and matches before doing any welding.
• Follow requirements in OSHA and NFPA for hot work and have an extinguisher nearby.
High Frequency Radiation
• High Frequency (H.F) can interfere with radio navigation, safety services, computers and communication equipment.
• It is the user’s responsibility to have a qualified electrician promptly correct any interference problem resulting from the
installation. Electrician should regularly check and maintain installation.
• Stop using the equipment if notified by the FCC about interference.
• Keep H.F. source doors and panels tightly shut and keep spark gaps at correct setting.
Arc Welding
•
Computers and computer driven equipment can be harmed with electromagnetic energy.
•
Be sure all equipment is compatible with electromagnetic energy.
•
Keep welding cables short to reduce interference.
•
Follow manual to install and ground machine.
•
If interference continues, shield the work area or move the welding machine.
WARNING: ELECTRIC SHOCK CAN KILL!
To reduce the risk of death or serious injury from shock, read,
understand, and follow the safety instructions. In addition, make certain that anyone else who uses this welding
equipment, or who is a bystander in the welding area understands and follows these safety instructions as well.
IMPORTANT! TO REDUCE THE RISK OF DEATH, INJURY, OR PROPERTY DAMAGE, DO NOT
ATTEMPT OPERA TION
of this welding equipment until you have read and understand the following safety summary.
•
Do not, in any manner, come into physical contact with any part of the welding current circuit. The welding current
circuit includes:
a. the workpiece or any conductive material in contact with it,
b. the ground clamp,
c. the electrode or welding wire,
Electric Shock