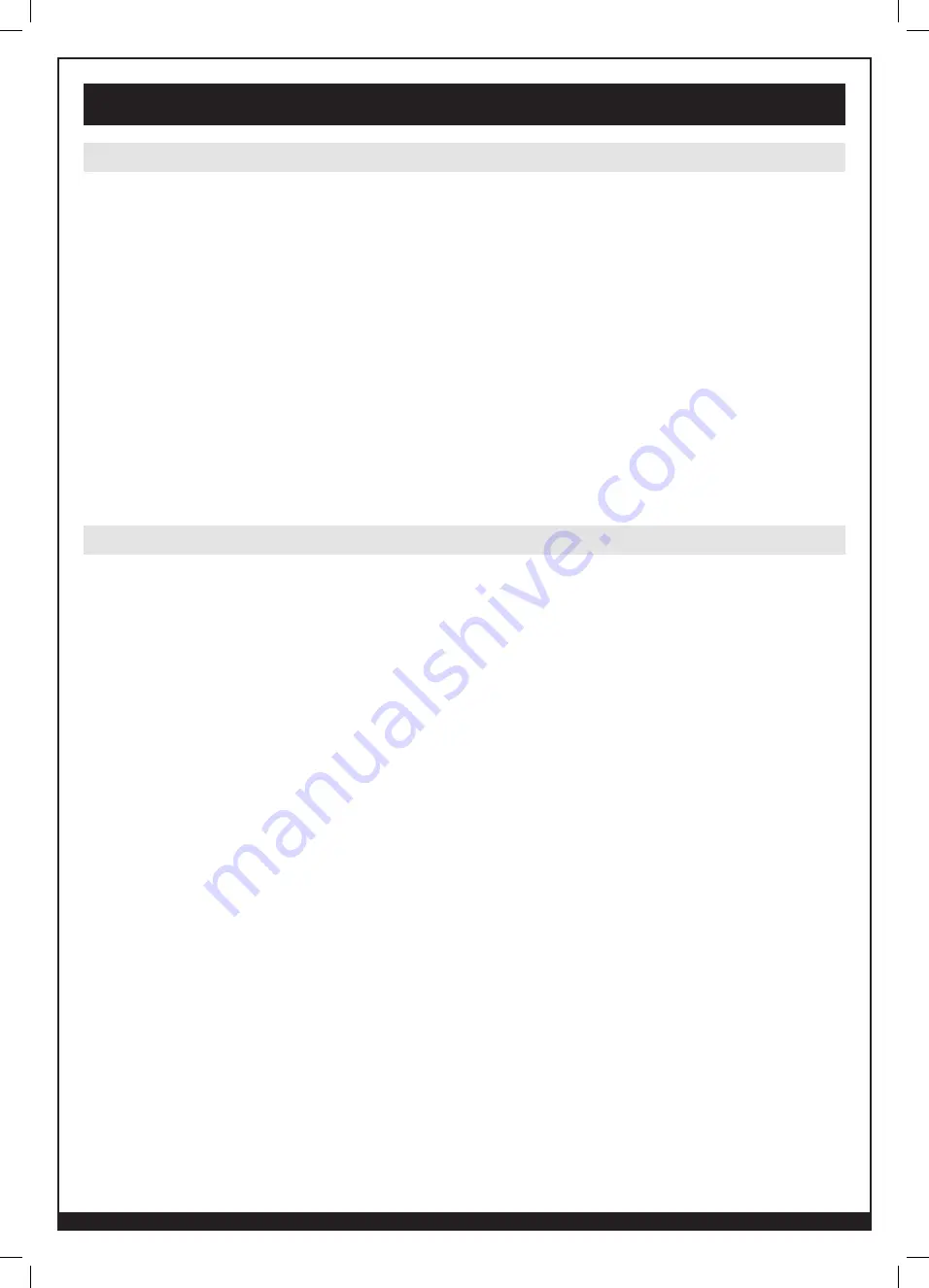
11
WWW.FORNEYIND.COM
Description
Your new Forney Spool PRO Hornet SG 250 spool gun was designed to be the most user-friendly and comfortable spool
gun on the market, all while delivering unprecedented performance.
Ergonomics
Through a re-examination of feature and component placement, your spool gun was optimized for balance and usability.
By draping the power cable out of the bottom of the spool gun and placing the welding wire spool beneath the wrist, the
center of gravity is in the palm of your hand. This also presents a second hand-grip portion on the front of the spool gun
allowing the gun to pivot. This allows you to consistently lay down longer, un-interrupted weld.
Efficiency
Your new spool gun was designed with your workflow in mind. We started from the ground up with a total overhaul of
traditional spool gun functionality. Patent pending non-threaded engagement of the spool cover release, patent pending
spool break and spool break lock, spool life indicator, tapered wire inlet guide, and integrated contact tip storage are all
features that will help you get the job done.
Control
Because each job is different, the settings you use for one project might not be the best settings for another project. We
wanted to take the time out of determining the right settings and finding the “sweet spot.” That’s why we’ve placed the
wire feed speed control knob at your fingertips. This will allow you to precisely control the wire feed speed while welding
so you can dial in the perfect settings with ease.
Spool Gun Layout and Controls
1. Spool Gun Trigger
– On/Off spool gun control initiates wire feed, gas flow, and arc.
2. Wire Feed Speed Adjustment Knob
– Allows the user to adjust wire feed speed while welding. Turning the
knob counter-clockwise (or away from the user) increases the wire feed speed, and vice versa.
3. Spool Cover Release Knob
– Using patent pending non-threaded engagement, this knob is turned counter-
clockwise and pulled outward to remove the wire spool cover.
4. Torch Neck
5. TWECO Style Consumables - Series 14H contact tips, 52FN gas diffuser, and 23-50 nozzle
– Your spool
gun uses common TWECO Style Series 14H consumables that are readily available at most welding supply
stores.
6. Hanging Hook
7. Wire Tension Control Knob
– Allows the user to adjust the drive system tension on the welding wire.
8. Integrated Contact Tip Storage
– Allows the user to store two additional consumable contact for
convenience.
9. Spool Brake / Spool Life Indicator
– The spool brake applies a constant braking force to the rotation of
the welding wire spool. Your spool gun is equipped with a spool brake system that can be locked away for
ease of wire spool replacement. The lock also serves as an approximate spool life indicator.
10. 25 Foot (7m) Power Cable
– Depending on the manufacturer of your power supply, your spool gun is
equipped with a 25 foot power cable with either Euro-Connect, or other proprietary machine connections.
11. Liner Inlet Guide
- The Teflon (PTFE) liner of your new Spool PRO Hornet SG 250 is a consumable part and
will need to be replaced from time to time. It can be easily removed and replaced via the liner inlet guide.
Getting to Know Your Spool Gun