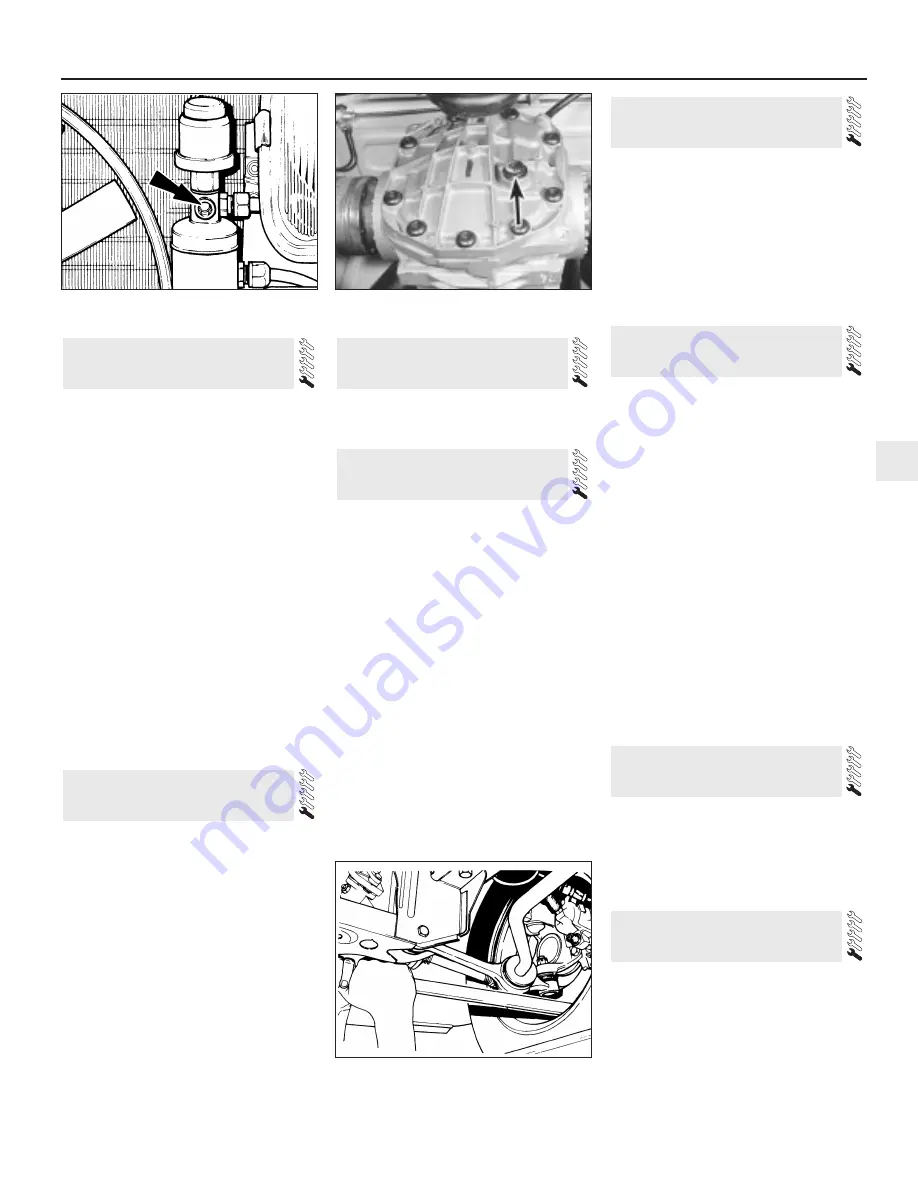
1 Remove the radiator grille being careful not
to damage the condenser fins.
2 Check the refrigerant charge as follows. The
engine should be cold and the ambient
temperature should be between 18° and 25°C
(64° and 77°F).
3 Start the engine and allow it to idle. Observe
the refrigerant sight glass (see illustration)
and have an assistant switch on the air
conditioning to fan speed III. A few bubbles
should be seen in the sight glass as the
system starts up, but all bubbles should
disappear within 10 seconds. Persistent
bubbles, or no bubbles at all, mean that the
refrigerant charge is low. Switch off the
system immediately if the charge is low and do
not use it again until it has been recharged.
4 Inspect the refrigerant pipes, hoses and
unions for security and good condition. Refit
the radiator grille.
5 The air conditioning system will lose a
proportion of its charge through normal
seepage typically up to 100 g (4 oz) per year -
so it is as well to regard periodic recharging as
a maintenance operation.
1 Check the final drive oil level as follows.
2 Position the vehicle over a pit, or raise it at
front and rear on ramps or axle stands (see
“Jacking”). The vehicle must be level.
3 Wipe clean around the final drive filler/level
plug (see illustration). Unscrew the plug with
a hexagon key. Using a piece of bent wire as
a dipstick, check that the oil is no more than
10 mm (0.4 in) below the plug hole.
4 If topping-up is necessary, use clean gear
oil of the specified type. Do not overfill.
Frequent need for topping-up can only be due
to leaks, which should be rectified.
5 When the level is correct, refit the filler/level
plug and tighten it.
6 There is no requirement for periodic oil
changing, and no drain plug is provided.
Lubricate the transmission selector and
kickdown linkages with engine oil or aerosol
lubricant.
1 Examine all steering and suspension
components for wear and damage. Pay
particular attention to dust covers and gaiters,
which if renewed promptly when damaged can
save further damage to the component
protected.
2 At the same intervals, check the front
suspension lower arm balljoints for wear by
levering up the arms (see illustration).
Balljoint free movement must not exceed
0.5 mm (0.02 in). The track rod end balljoints
can be checked in a similar manner, or by
observing them whilst an assistant rocks the
steering wheel back and forth. If the lower arm
balljoint is worn, the complete lower arm must
be renewed.
3 Check the shock absorbers by bouncing the
vehicle up and down at each corner in turn.
When released, it should come to rest within
one complete oscillation. Continued
movement, or squeaking and groaning noises
from the shock absorber suggests that
renewal is required.
Position the vehicle over a pit, or raise it at
front and rear on ramps or axle stands.
Examine the driveshaft joint rubber gaiters.
Flex the gaiters by hand and inspect the folds
and clips. Damaged or leaking gaiters must be
renewed without delay to avoid damage
occurring to the joint itself
Check the tightness of the final drive
mounting bolts and the driveshaft flange
screws.
1 Except on vehicles with a wax-based
underbody protective coating, have the whole
of the underframe of the vehicle steam-
cleaned, engine compartment included, so
that a thorough inspection can be carried out
to see what minor repairs and renovations are
necessary.
2 Steam-cleaning is available at many
garages, and is necessary for the removal of
the accumulation of oily grime, which
sometimes is allowed to become thick in
certain areas. If steam-cleaning facilities are
not available, there are some excellent grease
solvents available which can be brush-applied;
the dirt can then be simply hosed off.
3 After cleaning, position the vehicle over a
pit, or raise it at front and rear on ramps or axle
stands.
4 Using a strong light, work around the
underside of the vehicle, inspecting it for
corrosion or damage. If either is found, refer to
Chapter 12 for details of repair.
Periodically inspect the rigid brake pipes for
rust and other damage, and the flexible hoses
for cracks, splits or “ballooning”. Have an
assistant depress the brake pedal (ignition on)
and inspect the hose and pipe unions for
leaks. Renew any defective item without delay.
On 2.0 litre engines, good electrical contact
between the carburettor stepper motor
plunger and the adjusting screw is essential to
maintain a regular idle speed.
Clean the plunger and adjusting screw
contact faces with abrasive paper followed by
switch cleaning fluid. Switch cleaning fluid is
available from electronic component shops.
33 Idle speed linkage clean
32 Brake pipe and hose check
31 Underbody inspection
30 Driveshaft check
29 Steering and suspension
security check
28 Automatic transmission
selector linkage lubrication
27 Final drive oil level check
26 Air conditioner refrigerant
charge check
1•15
1
Every 12 000 miles or 12 months
27.3 Final drive oil filler/level plug (arrowed)
29.2 Checking a front suspension lower
arm balljoint
26.3 Refrigerant sight glass (arrowed)
Summary of Contents for Granada 1985-1994
Page 42: ...1 22 Notes...
Page 102: ...2C 22 Notes...
Page 136: ...4 24 Notes...
Page 176: ...11 14 Notes...
Page 196: ...12 20 Notes...
Page 221: ...Wiring diagrams WD 1 WD Diagram 16 Power operated sliding roof...
Page 222: ...WD 2 Wiring diagrams Diagram 2 Power distribution...
Page 223: ...Wiring diagrams WD 3 WD Diagram 2 Power distribution continued...
Page 224: ...WD 4 Wiring diagrams Diagram 3 Charge start and run Part 1...
Page 225: ...Wiring diagrams WD 5 WD Diagram 3 Charge start and run Part 1 continued...
Page 226: ...WD 6 Wiring diagrams Diagram 3A Charge start and run Part 2...
Page 227: ...Wiring diagrams WD 7 WD Diagram 3A Charge start and run Part 2 continued...
Page 228: ...WD 8 Wiring diagrams Diagram 4 Engine management 1 8 litre...
Page 229: ...Wiring diagrams WD 9 WD Diagram 4 Engine management 1 8 litre continued...
Page 230: ...WD 10 Wiring diagrams Diagram 4A Engine management 2 0 litre carburettor...
Page 231: ...Wiring diagrams WD 11 WD Diagram 4A Engine management 2 0 litre carburettor continued...
Page 232: ...WD 12 Wiring diagrams Diagram 5 Engine management 2 0 litre fuel injection...
Page 233: ...Wiring diagrams WD 13 WD Diagram 5 Engine management 2 0 litre fuel injection continued...
Page 234: ...WD 14 Wiring diagrams Diagram 5C Engine management 2 8 litre...
Page 235: ...Wiring diagrams WD 15 WD Diagram 5C Engine management 2 8 litre continued...
Page 236: ...WD 16 Wiring diagrams Diagram 7A Exterior lighting...
Page 237: ...Wiring diagrams WD 17 WD Diagram 7A Exterior lighting continued...
Page 238: ...WD 18 Wiring diagrams Diagram 9 Signalling and warning systems...
Page 239: ...Wiring diagrams WD 19 WD Diagram 9 Signalling and warning systems continued...
Page 240: ...WD 20 Wiring diagrams Diagram 10 Interior lighting...
Page 241: ...Wiring diagrams WD 21 WD Diagram 10 Interior lighting continued...
Page 242: ...WD 22 Wiring diagrams Diagram 12 Wipers and washers...
Page 243: ...Wiring diagrams WD 23 WD Diagram 12 Wipers and washers continued...
Page 244: ...WD 24 Wiring diagrams Diagram 14 Central locking system...
Page 245: ...Wiring diagrams WD 25 WD Diagram 14 Central locking system continued...
Page 246: ...WD 26 Wiring diagrams Diagram 15 Power operated windows...
Page 247: ...Wiring diagrams WD 27 WD Diagram 15 Power operated windows continued...
Page 248: ...WD 28 Wiring diagrams Diagram 21 ABS...
Page 249: ...Wiring diagrams WD 29 WD Diagram 21 ABS continued...
Page 250: ...WD 30 Wiring diagrams Diagram 23 Auxiliary warning system...
Page 251: ...Wiring diagrams WD 31 WD Diagram 23 Auxiliary warning system continued...
Page 252: ...WD 32 Wiring diagrams Diagram 29 Radio cassette player and associated circuits typical...
Page 254: ...WD 34 Wiring diagrams Diagram 11 Heater blower...