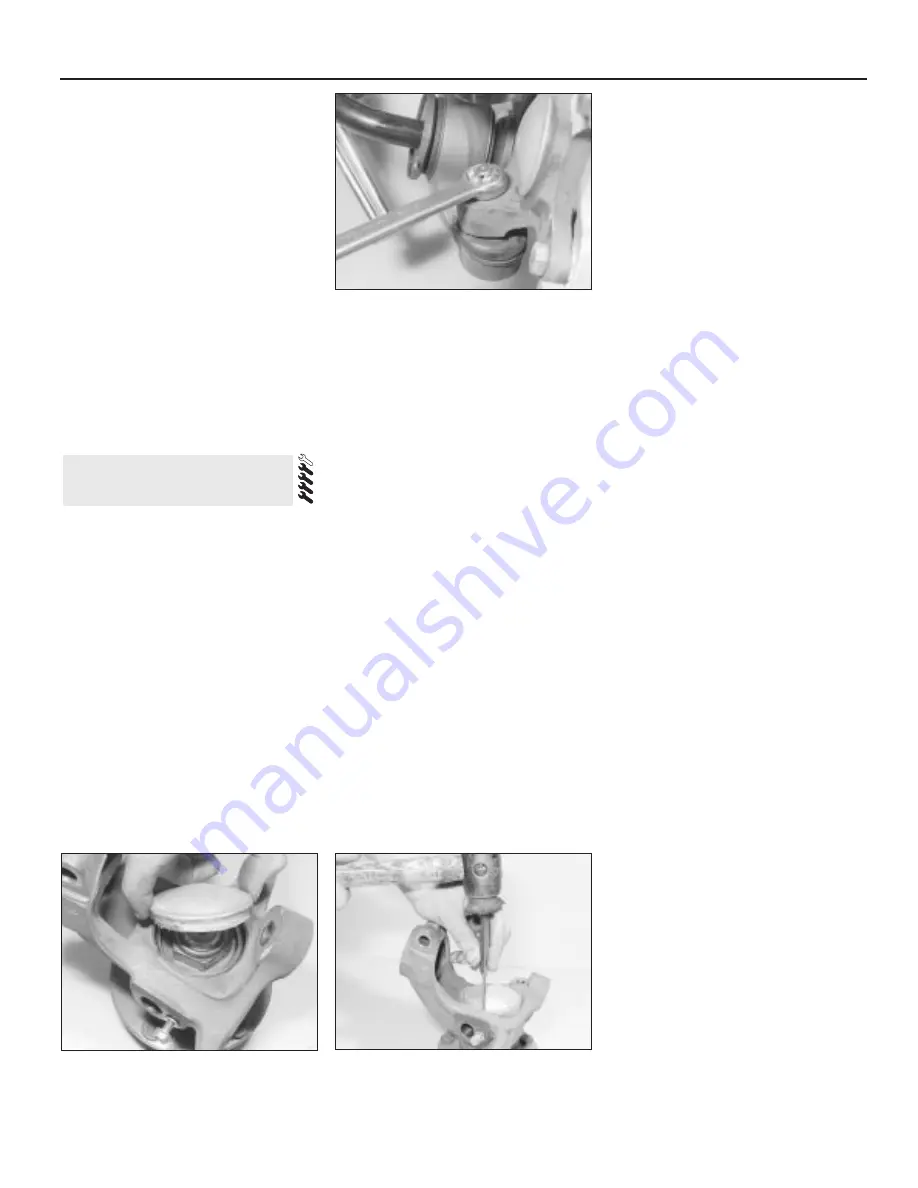
times, then use a proprietary balljoint
separator to break the taper (see illustration).
5 Use a stout piece of wood to lever the lower
arm downwards and free the balljoint from the
stub axle carrier.
6 Remove the ABS wheel sensor from its
hole.
7 Remove the spring clip from one of the
wheel studs and pull the brake disc off the
hub.
8 Remove the stub axle carrier pinch-bolt.
Spread the stub axle carrier by carefully
introducing a chisel or blunt instrument into its
slot. Draw the stub axle carrier off the
suspension strut and remove it.
9 Refit by reversing the removal operations,
noting the following points:
a) Tighten all fastenings to the specified
torque
b) Use new split pins, when applicable
c) Renew the wheel sensor O-ring if
necessary; clean the sensor and its bore,
and smear them with wheel bearing
grease
Models before August 1989
1 Remove the stub axle carrier as described
in the previous Section.
2 Screw the wheel nuts onto the studs to
protect the threads. Clamp the stub axle
carrier in a vice by means of the studs and
nuts; do not overtighten.
3 Remove the dust cap from the hub nut,
carefully levering it free (see illustration). A
new cap and a new hub nut will be required for
reassembly.
4 Undo the hub nut. This nut is very tight. The
right-hand hub nut has a left-hand thread,
therefore it is undone in a clockwise direction.
5 Remove the ABS rotor from below the hub
nut.
6 Lift the carrier off the stub axle, tapping it
with a mallet if necessary to free it. Remove
the bearing inner race from the carrier.
7 Prise the oil seal out of the carrier and
recover the bearing outer race.
8 Drive the bearing tracks out of the stub axle
carrier using a blunt drift and a hammer. Be
careful not to mark the bearing seats.
9 Clean all old grease and debris from the
stub axle carrier.
10 New bearing components are matched in
production and must only be fitted as a set.
Only the manufacturer’s approved
components should be used in order to obtain
the required long service life and freedom from
adjustment.
11 Drive the new bearing tracks into the
carrier, preferably using a suitable diameter
tube to seat them. Make sure the tracks are
fully seated.
12 Work some clean grease into the bearing
races. Use high melting-point lithium-based
grease (to Ford spec. SAMIC-9111A or
equivalent). Make sure all the spaces between
the rollers are filled; do not pack grease into
the space between the inner and outer
bearings however.
13 Fit the bearing outer race. Grease the lips
of a new oil seal and fit it to the stub axle
carrier, lips facing inwards. Seat the seal with
a pipe or large socket and a mallet.
14 Offer the carrier to the stub axle, tapping it
home if necessary. Fit the bearing inner race
over the stub axle.
15 Refit the ABS rotor, dished face
uppermost.
16 Fit a new hub nut (left-hand thread on the
right-hand hub) and tighten it to the specified
torque.
17 Fit a new dust cap and seat it by tapping
round the rim (see illustration).
18 Refit the stub axle carrier.
Models from August 1989
19 Modified front wheel bearing assemblies
were fitted to all models after 1989. The
modified bearings are of similar design, but
are interference fit type bearings. This was to
reduce the amount of endfloat present at the
wheel hub and to improve bearing preload
tolerances. This was achieved by increasing
the diameter of the stub axle, thus causing the
axle to be an interference fit in the bearing.
Note that the modified bearings can be fitted
to earlier models which were originally
equipped with non-interference fit front wheel
bearings. Note: Due to the design of the
interference fit bearings, a suitable heavy duty
bearing puller and a hydraulic press and
several suitable mandrels will be required to
remove the original bearing and install the new
one.
20 Interference fit front wheel bearings can be
removed and refitted as described above,
noting the following points.
a) It will be necessary to press or draw the
stub axle out of the carrier using a
hydraulic press or a suitable bearing
puller.
b) Draw the outer bearing off the stub axle
using a suitable bearing puller.
c) Press new bearing tracks into the hub
carrier using a suitable tubular spacer
which bears only on the tracks outer edge.
d) Pack the new outer bearing with Ford
grease (SAM-1C9111-A) and press the
bearing into the carrier.
e) Press a new seal into position in the
carrier and pack all cavities with the
specified grease.
f) Position the hub carrier over the stub axle
and press the carrier onto the axle using a
suitable tubular spacer which bears only
on the bearing track outer edge.
g) Pack the new inner bearing with the
specified grease then press the bearing
onto the stub axle, using a suitable tubular
spacer, whilst rotating the hub carrier to
ensure that the bearing is correctly seated.
h) Whilst tightening the hub nut to the
specified torque, rotate the hub carrier to
ensure that the bearing preload is correct
and bearings are correctly seated. Once
the nut is tightened to the specified
torque, rotate the hub carrier 20 times to
settle the bearings in position then
recheck that the hub nut is tightened to
the specified torque. Pack the inner
bearing with the specified grease and fit a
new dust cap.
17 Front wheel bearings -
renewal
11•8 Steering and suspension
16.4 Slackening the front suspension lower
arm balljoint nut
17.17 Seating the new dust cap
17.3 Removing the dust cap from the stub
axle carrier to expose the hub nut
Summary of Contents for Granada 1985-1994
Page 42: ...1 22 Notes...
Page 102: ...2C 22 Notes...
Page 136: ...4 24 Notes...
Page 176: ...11 14 Notes...
Page 196: ...12 20 Notes...
Page 221: ...Wiring diagrams WD 1 WD Diagram 16 Power operated sliding roof...
Page 222: ...WD 2 Wiring diagrams Diagram 2 Power distribution...
Page 223: ...Wiring diagrams WD 3 WD Diagram 2 Power distribution continued...
Page 224: ...WD 4 Wiring diagrams Diagram 3 Charge start and run Part 1...
Page 225: ...Wiring diagrams WD 5 WD Diagram 3 Charge start and run Part 1 continued...
Page 226: ...WD 6 Wiring diagrams Diagram 3A Charge start and run Part 2...
Page 227: ...Wiring diagrams WD 7 WD Diagram 3A Charge start and run Part 2 continued...
Page 228: ...WD 8 Wiring diagrams Diagram 4 Engine management 1 8 litre...
Page 229: ...Wiring diagrams WD 9 WD Diagram 4 Engine management 1 8 litre continued...
Page 230: ...WD 10 Wiring diagrams Diagram 4A Engine management 2 0 litre carburettor...
Page 231: ...Wiring diagrams WD 11 WD Diagram 4A Engine management 2 0 litre carburettor continued...
Page 232: ...WD 12 Wiring diagrams Diagram 5 Engine management 2 0 litre fuel injection...
Page 233: ...Wiring diagrams WD 13 WD Diagram 5 Engine management 2 0 litre fuel injection continued...
Page 234: ...WD 14 Wiring diagrams Diagram 5C Engine management 2 8 litre...
Page 235: ...Wiring diagrams WD 15 WD Diagram 5C Engine management 2 8 litre continued...
Page 236: ...WD 16 Wiring diagrams Diagram 7A Exterior lighting...
Page 237: ...Wiring diagrams WD 17 WD Diagram 7A Exterior lighting continued...
Page 238: ...WD 18 Wiring diagrams Diagram 9 Signalling and warning systems...
Page 239: ...Wiring diagrams WD 19 WD Diagram 9 Signalling and warning systems continued...
Page 240: ...WD 20 Wiring diagrams Diagram 10 Interior lighting...
Page 241: ...Wiring diagrams WD 21 WD Diagram 10 Interior lighting continued...
Page 242: ...WD 22 Wiring diagrams Diagram 12 Wipers and washers...
Page 243: ...Wiring diagrams WD 23 WD Diagram 12 Wipers and washers continued...
Page 244: ...WD 24 Wiring diagrams Diagram 14 Central locking system...
Page 245: ...Wiring diagrams WD 25 WD Diagram 14 Central locking system continued...
Page 246: ...WD 26 Wiring diagrams Diagram 15 Power operated windows...
Page 247: ...Wiring diagrams WD 27 WD Diagram 15 Power operated windows continued...
Page 248: ...WD 28 Wiring diagrams Diagram 21 ABS...
Page 249: ...Wiring diagrams WD 29 WD Diagram 21 ABS continued...
Page 250: ...WD 30 Wiring diagrams Diagram 23 Auxiliary warning system...
Page 251: ...Wiring diagrams WD 31 WD Diagram 23 Auxiliary warning system continued...
Page 252: ...WD 32 Wiring diagrams Diagram 29 Radio cassette player and associated circuits typical...
Page 254: ...WD 34 Wiring diagrams Diagram 11 Heater blower...