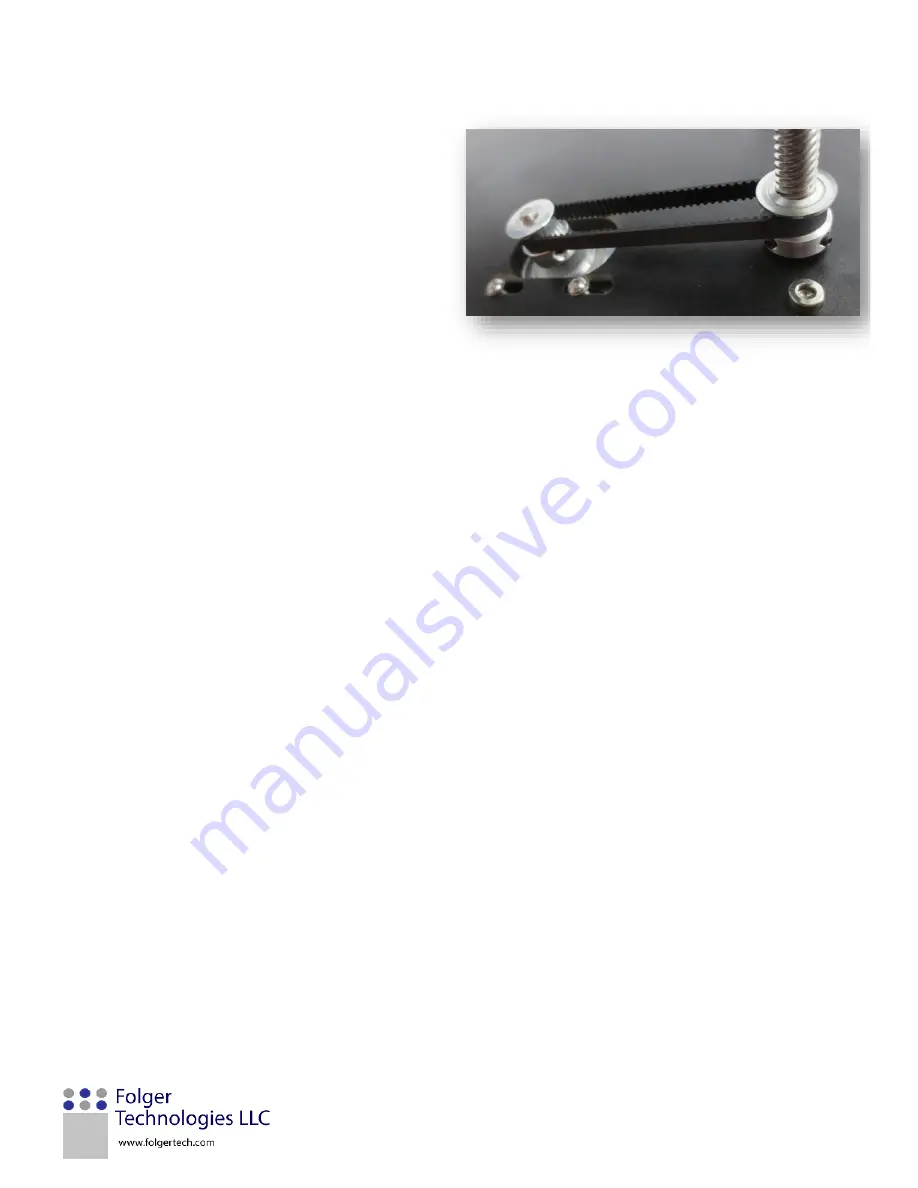
FT-5 User Manual Page 29
6.
Insert one of the 20T 5mm bore pulleys onto
the stepper motor located on the base plate.
Loosen the four stepper motor screws and
position the belt so it is in both of the toothed
groves on both pulleys. Ensure the belt is strait
and tighten the screws on the stepper motor.
7.
Repeat steps 3-6 on the other threaded rod.