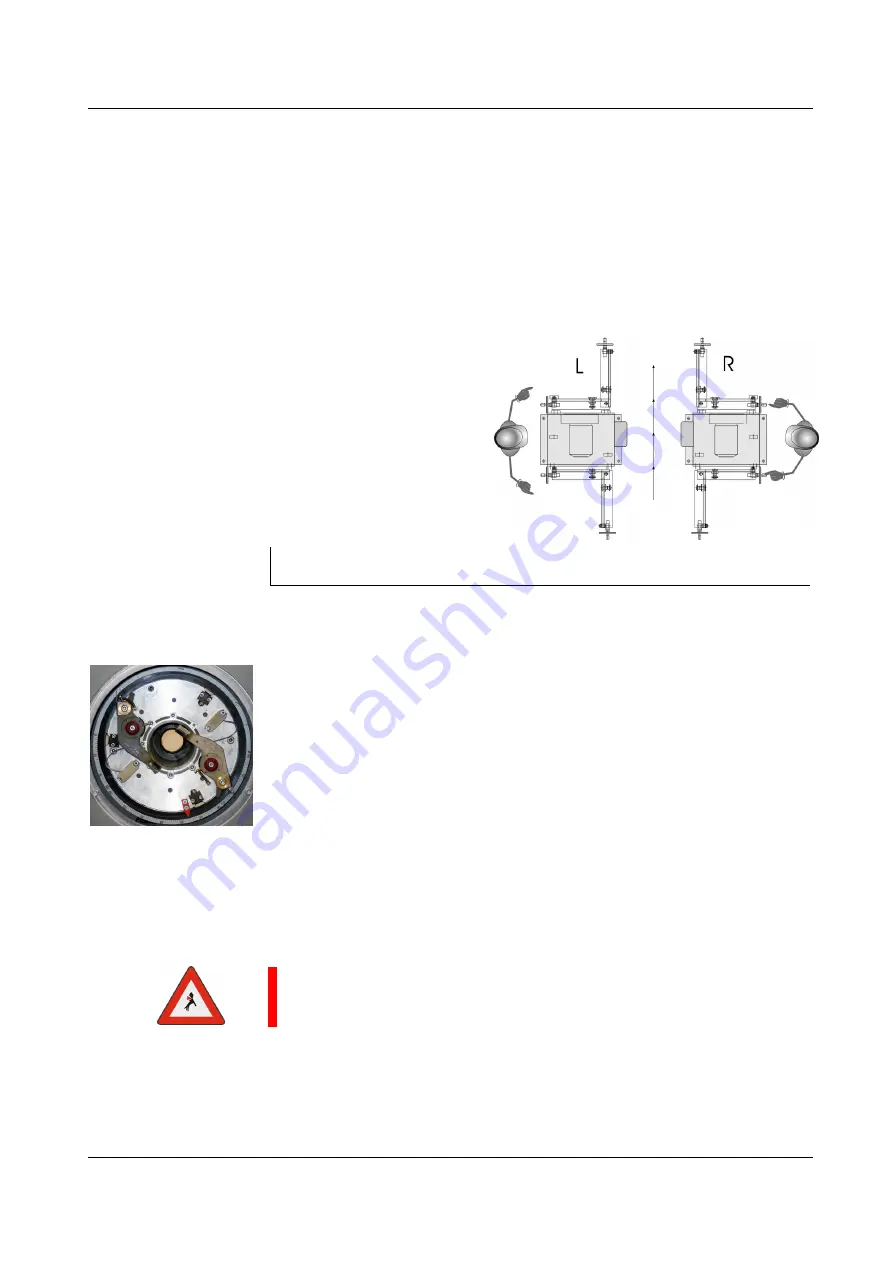
FUNCTIONAL DESCRIPTION
2.3 Construction
6.452
13
2.3.2 Rotating Head Ro 65
The rotating head is the main component of the sensor system.
It consists of:
Rotor
Transmitter
Drive
Housing
Rotating head electronics
The operating side is to be
selected as right or left in the
order!
Rotor
The rotor consists of a hollow shaft, a rotor disc and the movable part of
the transmitter.
The rotor is driven by the motor by means of a V-ribbed belt. It is sup-
ported in the housing by two high-speed bearings.
The high-precision rotating disc for holding the test heads is fitted on the
front side.
A pivot-mounted spiral disc with an actuating gear and automatic blocking
facility is fitted in the rotating disc for precise and simultaneous test head
diameter adjustment.
DANGER
!
Never run the rotating head without test heads!
Always use test heads in pairs with the spring in the same position!
Rotating disc with test heads
left: head in lift off position
right: testing position
Fig. 2.4 CIRCOGRAPH sensor system Ro 65, operating side left (L) or right (R)
Summary of Contents for CIRCOGRAPH DS
Page 1: ...CIRCOGRAPH DS Sensor system Ro 65 6 452 Operating Instructions Original Instructions...
Page 2: ......
Page 8: ...Table of Contents IV 6 452 Notes...
Page 14: ...1 13 Declaration of Conformity SAFETY 6 6 452 Notes...
Page 29: ...FUNCTIONAL DESCRIPTION 2 5 Dimension sheet 6 452 21 Fig 2 10 Dimension sheet 2...
Page 32: ...2 7 Standard Components FUNCTIONAL DESCRIPTION 24 6 452 Notes...
Page 52: ...4 6 Application drawing line OPERATION 44 6 452 Notes...