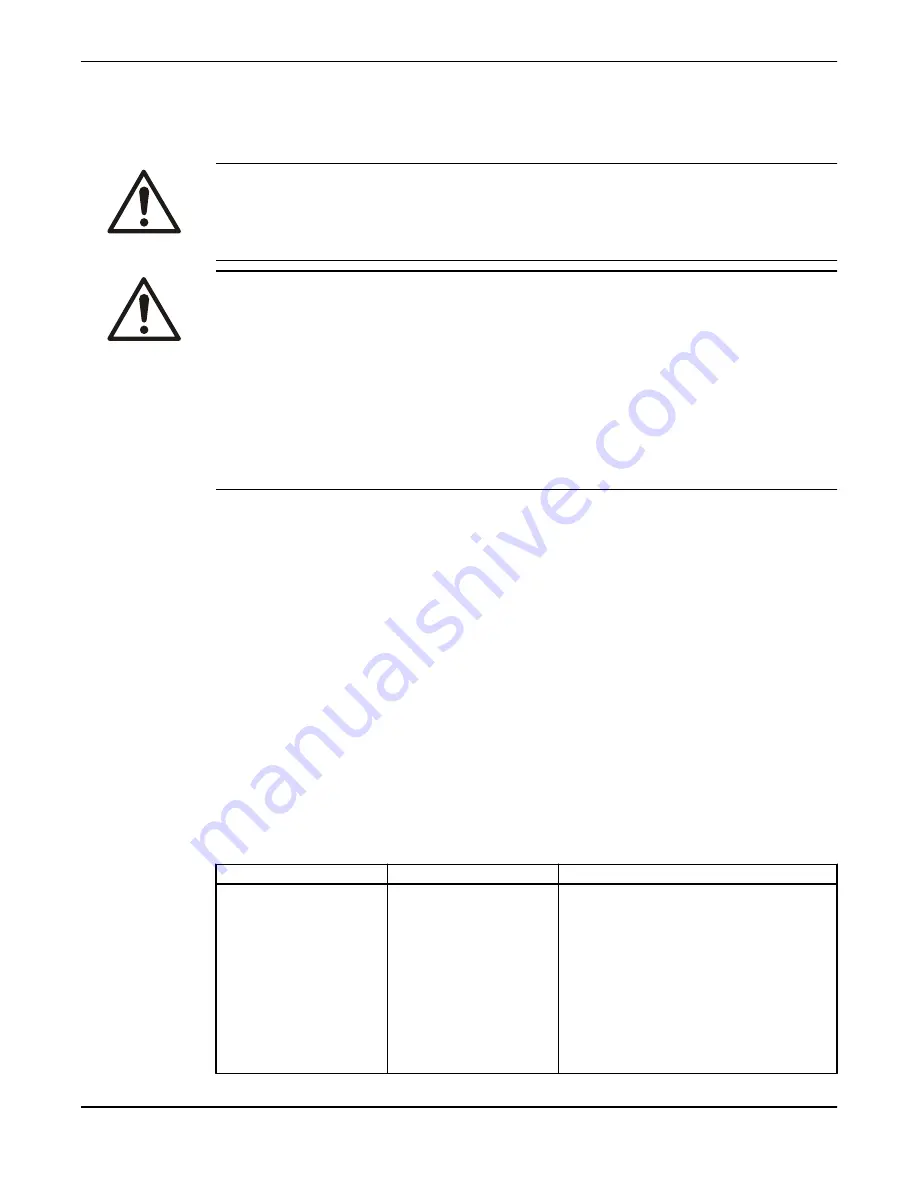
Maintenance
Precautions
WARNING:
• Always follow safety guidelines when working on the pump. See
(page 5).
• If you need to work on the pump, make sure that it is isolated from the power supply and cannot be
energized.
WARNING:
• Check that local safety regulations are followed.
• Check the guard rails, covers, and other protections.
• Rinse the pump thoroughly with clean water before working on the pump.
• Rinse the components in water after dismantling.
• Make sure that the pump cannot roll or fall over and injure people or damage property.
• In some installations, the pump and the surrounding liquid may be hot. Bear in mind the risk of burn
injuries.
• Make sure nobody is close to the pump when it is started. The pump will jerk in the opposite
direction of the impeller rotation.
The following requirements apply:
• Make sure that all safety guards are in place and secure.
• Make sure that you have a clear path of retreat.
• Never work alone.
• Check the explosion risk before starting work.
• Allow all system and pump components to cool before you handle them.
• Do not open any vent or drain valves or remove any plugs while the system is pressurized. Make sure
that the pump is isolated from the system and that pressure is relieved before you disassemble the
pump, remove plugs, or disconnect piping.
• Depressurize and empty the coolant system for T and Z installations, and all installations with
external cooling.
• Make sure electrical power is disconnected, locked and tagged.
Service
Regular inspection and service of the pump ensures more reliable operation.
Every time the site is visited, visually inspect the accessories and sump for corrosion, wear or damage.
Table 19: Service intervals
Type of service
Purpose
Interval
Inspection
To prevent operational
interruptions and machine
breakdown. Measures to
secure performance and
pump efficiency are defined
and decided for each
individual application. It can
include such things as
impeller trimming, wear part
control and replacement,
control of zinc-anodes and
control of the stator.
12,000 hours or 3 years, whichever comes first.
Applies to normal applications and operating
conditions at media (liquid) temperatures
< 40°C (104°F).
Maintenance
C3300/6x5, C/R3231, C3240, C3306, C3312, C3351, C3356, C3400, C3501, C3531, C3602, C3800 Installation,
Operation and Maintenance Manual
81