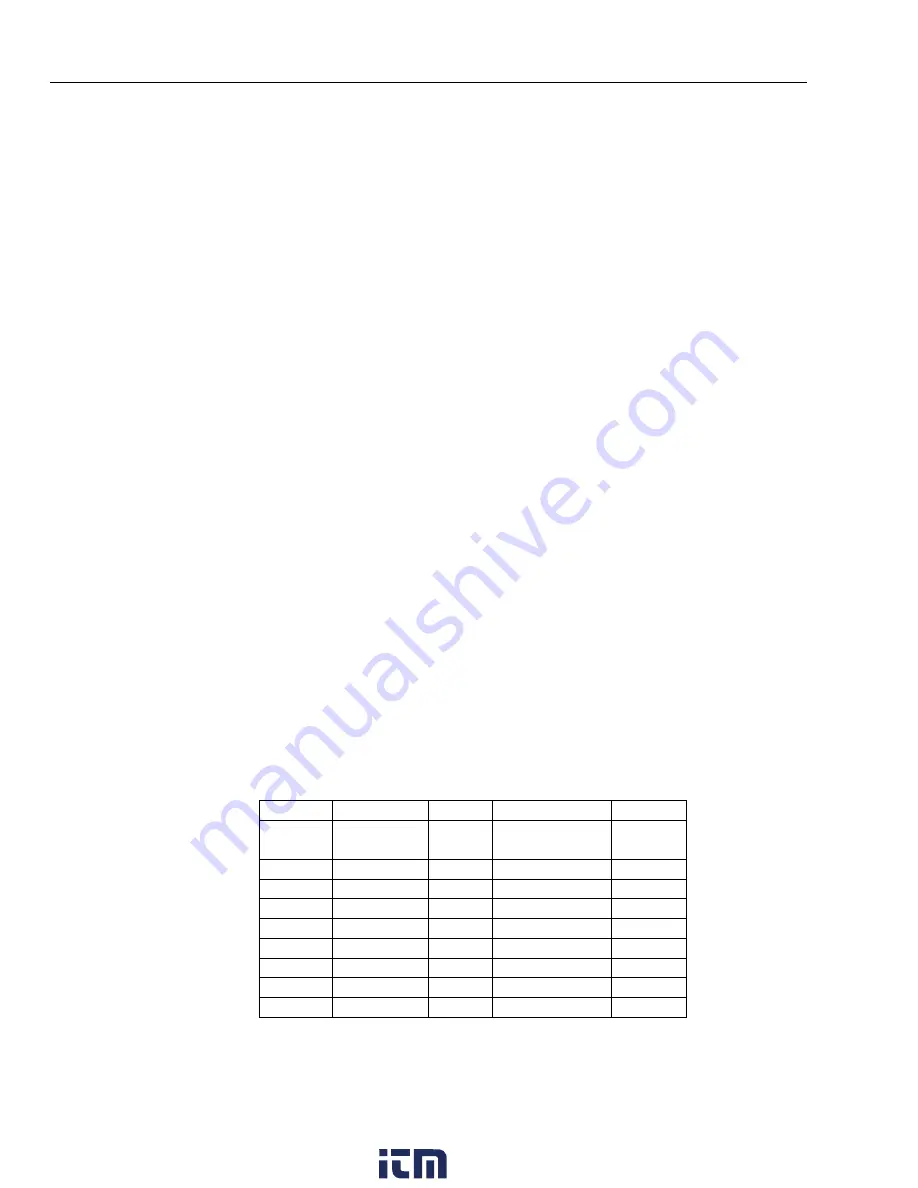
Thermalert
®
4.0 Series
Users Manual, Rev. 2.4, Jul 2021
66
9 EthernNet/IP
The EtherNet/IP module maps the object temperature, internal temperature, device status and other pyrometer
data to its input assembly which is then sent onto the EtherNet/IP network using CIP. In the initialization phase,
the device sends configuration data which is accessible for setup via the PLC programming software controller
tags. Furthermore, EtherNet/IP allows you to change a subset of sensor parameters in data exchange mode using
output data. For the device diagnostics, there is a special status register containing an error code, which is sent a
part of the device’s input data.
Specification:
•
Device class: adapter device
•
Device type: 06h (Photoelectric sensor)
9.1 Configuration
A manual configuration of the EtherNet/IP pyrometer is based on a generic Ethernet module. In this case, the
assembly instance number and size must be typed in. The device settings are:
•
Data type: SINT
•
Input assembly instance 101, size 12 byte
•
Output assembly instance 100, size 5 byte
•
Configuration assembly instance 102, size 0
9.2 Parameters
All settable parameters of the Thermalert 4.0 pyrometer are available in the Configuration Data. Changing the
parameters this way can only happen upon device initialization, i.e. when downloading the program to the PLC
(default values are sent if no changes have been made). Once the parameter setting has been performed, the I/O
device is ready to send cyclic productive data. While certain pyrometer characteristics are parameterizable only
during the configuration, others can also be set in the data exchange mode using Output Data. The tables below
contain all the parametrizable characteristics and are followed by a short implementation description.
The parameters included in the configuration data are accessible through controller tags in the PLC programming
environment. Changing them in the controller tags will first have effect after downloading the program to the PLC.
The programming software allows however for an easy saving of these tags so that the values can always be sent
as default upon initialization.
Table 9-1: Pyrometer Parameters
Attribute ID
Name
Data type
Data value
Access rule
0x01
Temperature unit
USINT
0x43 ('C') – Celsius
0x46 ('F') - Fahrenheit
Read/Write
0x02
Emissivity
REAL
0.1 ... 1.1
Read/Write
0x03
Transmissivity
REAL
0.1 ... 1.1
Read/Write
0x04
Device Offset
REAL
-200 … 200
Read/Write
0x05
Device Gain
REAL
0.8 ... 1.2
Read/Write
0x06
Average Time
REAL
0.1 ... 999.0
Read/Write
0x07
Peak hold Time
REAL
0.0 ... 999.0
Read/Write
0x08
Valley hold Time
REAL
0.0 ... 999.0
Read/Write
0x09
Laser control
USINT
0 - off, 1 - on
Read/Write
www.
.com
1.800.561.8187