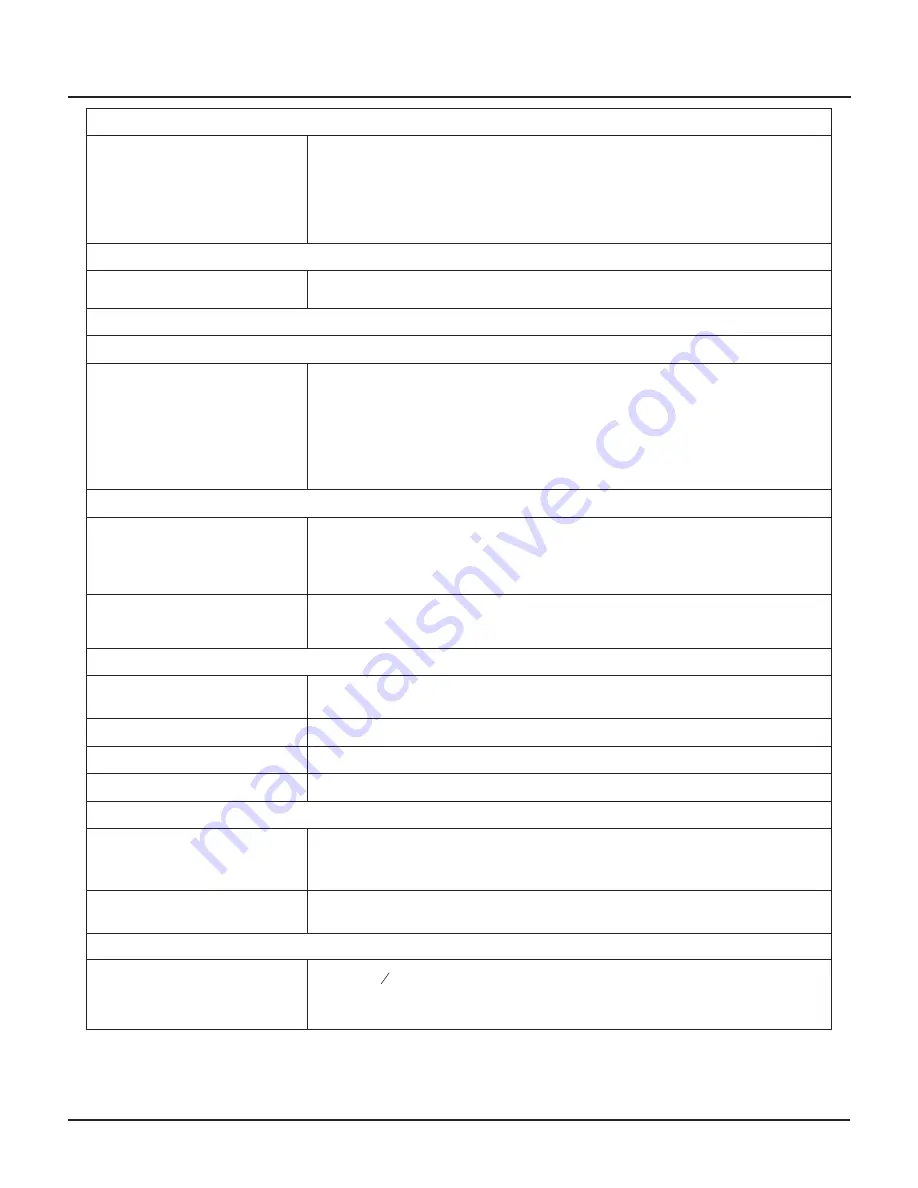
7. Hydraulic oil is milky or foamy
Leaking heat exchanger
1. Test the heat exchanger either removed or in place, for a static air leak at
150 psi (10.3 bar). Replace as necessary. Drain oil from the reservoir, hydrau-
lic pump case(s), hoses, and intensifier assembly(ies). Refill the reservoir and
pump case with clean hydraulic oil.
2. If the heat exchanger is not defective, look for a source of water vapor
condensation.
8. Oil is leaking around pump shaft
Defective hydraulic pump seal
Replace the seal; check for leaking after replacement. See
Replacing the shaft seal
.
9. Hydraulic oil contains metallic particles
Excessive wear of the intensifier low-pressure cylinder. Immediately stop the pump if one or more of the listed signs is present.
Signs of excessive wear: hydraulic sys-
tem is running hot, uneven stroking,
unusually high hydraulic pump noise
during shifting, sudden drop in the in-
tensifier's ability to meet demand for
high-pressure water, and severe pres-
sure fluctuation in the output water
1. Disassemble the intensifier, inspect the components, and rebuild, replacing all
worn parts. Inspect hoses.
2. Drain, thoroughly clean, and refill the hydraulic oil system (see
Cleaning a
contaminated hydraulic system
).
3. Replace the oil filter.
4. Reinstall the intensifier and return the equipment to service.
Excessive wear of the hydraulic pump. Immediately stop the pump if you see one or more of the listed signs.
Signs of a faulty hydraulic oil pump:
higher-than-normal pump noise, in-
ability to maintain the rated hydraulic
oil pressure, or loss of water pressure
1. Drain and thoroughly clean the hydraulic oil system. Replace the hydraulic
pump. Refill the hydraulic oil reservoir and pump case; see
Cleaning a con-
taminated hydraulic system
.
2. Return the pump to service.
Using the wrong oil
Drain, thoroughly clean, and refill the hydraulic oil system (see
Cleaning a contaminated
hydraulic system
).
10. Excessive pump noise and loss of oil pressure
Insufficient inlet hydraulic oil flow
to the pump
Make sure the reservoir is full of oil.
Air in oil
Inspect suction lines for leaks.
Water in oil
Inspect oil in reservoir. See Item 7 of this troubleshooting guide.
Malfunctioning hydraulic pump
Replace the hydraulic pump (see
Replacing the hydraulic pump
).
11. Orifice assembly life is too short
Poor water quality
1. Check the inlet water filter elements. Inlet water must be filtered to 0.5 mi-
cron and have a pH value of 6-8. Replace filter elements if clogged.
2. If applicable, check the deionization and water treatment systems.
Clogged or ruptured delivery
system component filter
Remove and inspect filters; replace if clogged or ruptured.
12. Attenuator is leaking water from end cap weep hole
There is a loose connection at out-
let or inlet fitting to attenuator
Loosen the
9
16
-in. tubing gland nut and torque the fitting adapter into the attenuator
housing to 60-75 ft-lb (81-102 N-m). Retorque the gland nut to 60-75 ft-lb and check
for leaks. If leaking continues, replace the fitting insert.
36 | M-390
© Flow International Corporation
HYPERJET™ 94i-S AND 94i-D PUMPS
Summary of Contents for 94i-D
Page 1: ...HYPERJET 94i S 94i D M 390 REV C APRIL 2010 ...
Page 6: ...Notes 6 M 390 Flow International Corporation HYPERJET 94i S AND 94i D PUMPS ...
Page 20: ...Notes 20 M 390 Flow International Corporation HYPERJET 94i S AND 94i D PUMPS ...
Page 30: ...Notes 30 M 390 Flow International Corporation HYPERJET 94i S AND 94i D PUMPS ...
Page 40: ...Notes 40 M 390 Flow International Corporation HYPERJET 94i S AND 94i D PUMPS ...
Page 75: ...CHAPTER 7 Customer Support MS 2266 Customer Support Flow International Corporation M 390 75 ...
Page 76: ...Notes 76 M 390 Flow International Corporation HYPERJET 94i S AND 94i D PUMPS ...