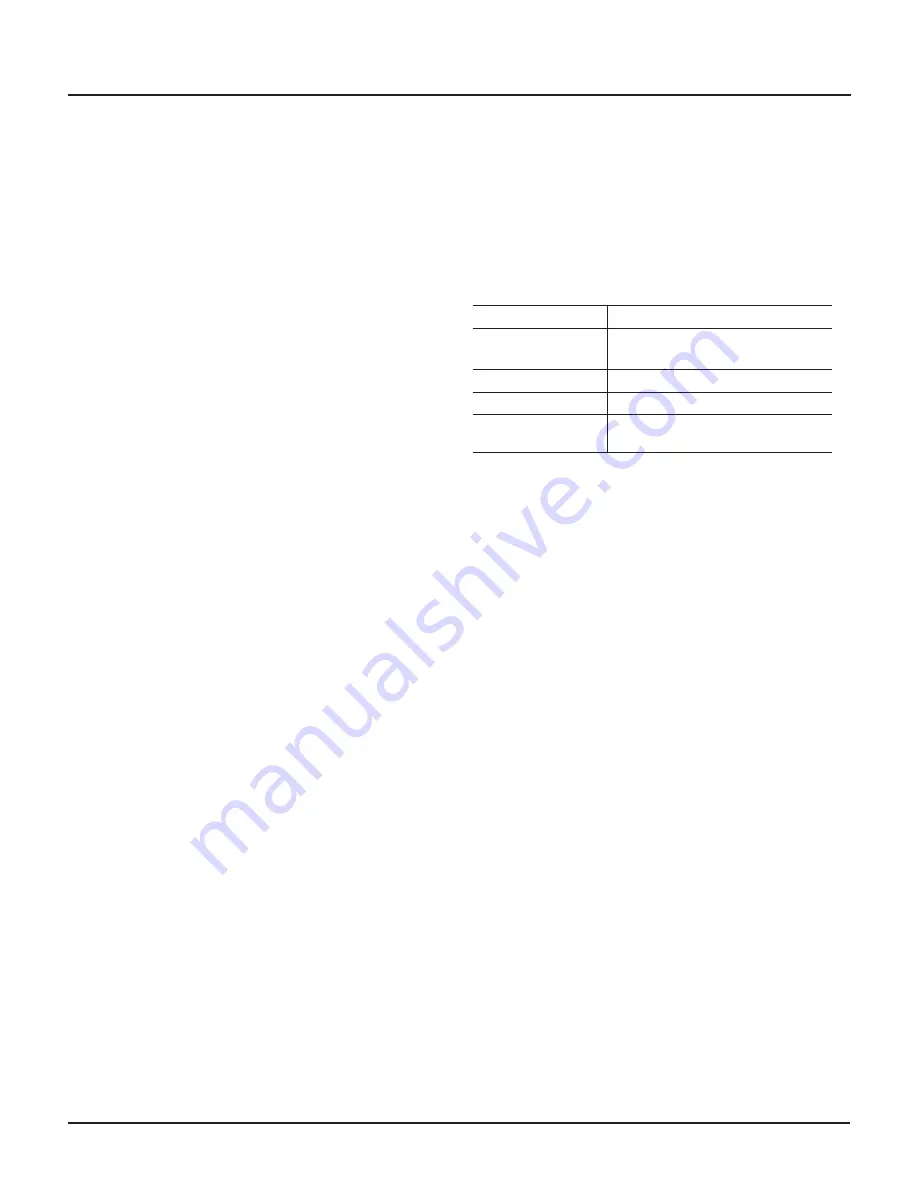
•
Replacement wires must conform to the manufac-
turer’s specifications, including proper color coding
and wire numbers.
Mechanical
•
Use only high-pressure fittings, valves, and tubing
certified for 92,000 psi (6483 bar) when making
changes to the high-pressure water system.
•
Immediately repair any leaks in fittings or connec-
tions. Torque all fittings to the manufacturer’s specifi-
cations.
•
When pressurizing any new, rebuilt, or recently ser-
viced high-pressure component, clear all personnel
from the immediate area until system pressure has
been applied for three minutes and cycled on and
off at least three times. Increase pressure slowly, a
maximum of 20,000 psi/min (1380 bar/min).
•
Do not touch high-pressure leaks.
•
Bleed down system pressure before servicing any
part of the system. Never tighten pressurized fittings.
•
Follow the manufacturer’s recommendations for
servicing the equipment, and use only original
manufacturer replacement parts.
•
Inspect the entire system before operating it. Correct
any fault or malfunction.
Tools
•
Use only approved test equipment, and check it
regularly for correct operation and calibration.
•
Use the correct tools—the incorrect tool can result in
injury to personnel or costly damage to the equipment.
•
Clear all tools and rags from around the machine
after service and before starting the equipment.
•
Use only approved work platforms. Never climb on
or around the equipment using makeshift devices.
Protective clothing
•
Do not wear loose clothing while working around
rotating parts of machinery.
•
Pressurized air can drive particles into eyes and skin
if handled improperly. To prevent injury, use appro-
priate protective equipment and clothing and exercise
extreme caution.
Hydraulic oil
Use an oil that does not contain anti-wear additives; the
following oils are recommended, but other manufacturer's
equivalents can be used:
•
Mobil DTE Medium
•
Shell Turbo T 46
•
Chevron Turbine Oil GST 46
•
Texaco Regal R&O 46
Kinematic viscosity
240 SSU @ 100°F (38°C)
Reservoir capacity
HyperJet
94i-S:
25 gal (95 L)
HyperJet
94i-D: 37 gal (140 L)
Filtration
6 microns, continuous flow
Cooling
Oil-to-water heat exchanger
Optimum oil temper-
ature
105°F (40.5°C)
32 | M-390
© Flow International Corporation
HYPERJET™ 94i-S AND 94i-D PUMPS
Summary of Contents for 94i-D
Page 1: ...HYPERJET 94i S 94i D M 390 REV C APRIL 2010 ...
Page 6: ...Notes 6 M 390 Flow International Corporation HYPERJET 94i S AND 94i D PUMPS ...
Page 20: ...Notes 20 M 390 Flow International Corporation HYPERJET 94i S AND 94i D PUMPS ...
Page 30: ...Notes 30 M 390 Flow International Corporation HYPERJET 94i S AND 94i D PUMPS ...
Page 40: ...Notes 40 M 390 Flow International Corporation HYPERJET 94i S AND 94i D PUMPS ...
Page 75: ...CHAPTER 7 Customer Support MS 2266 Customer Support Flow International Corporation M 390 75 ...
Page 76: ...Notes 76 M 390 Flow International Corporation HYPERJET 94i S AND 94i D PUMPS ...