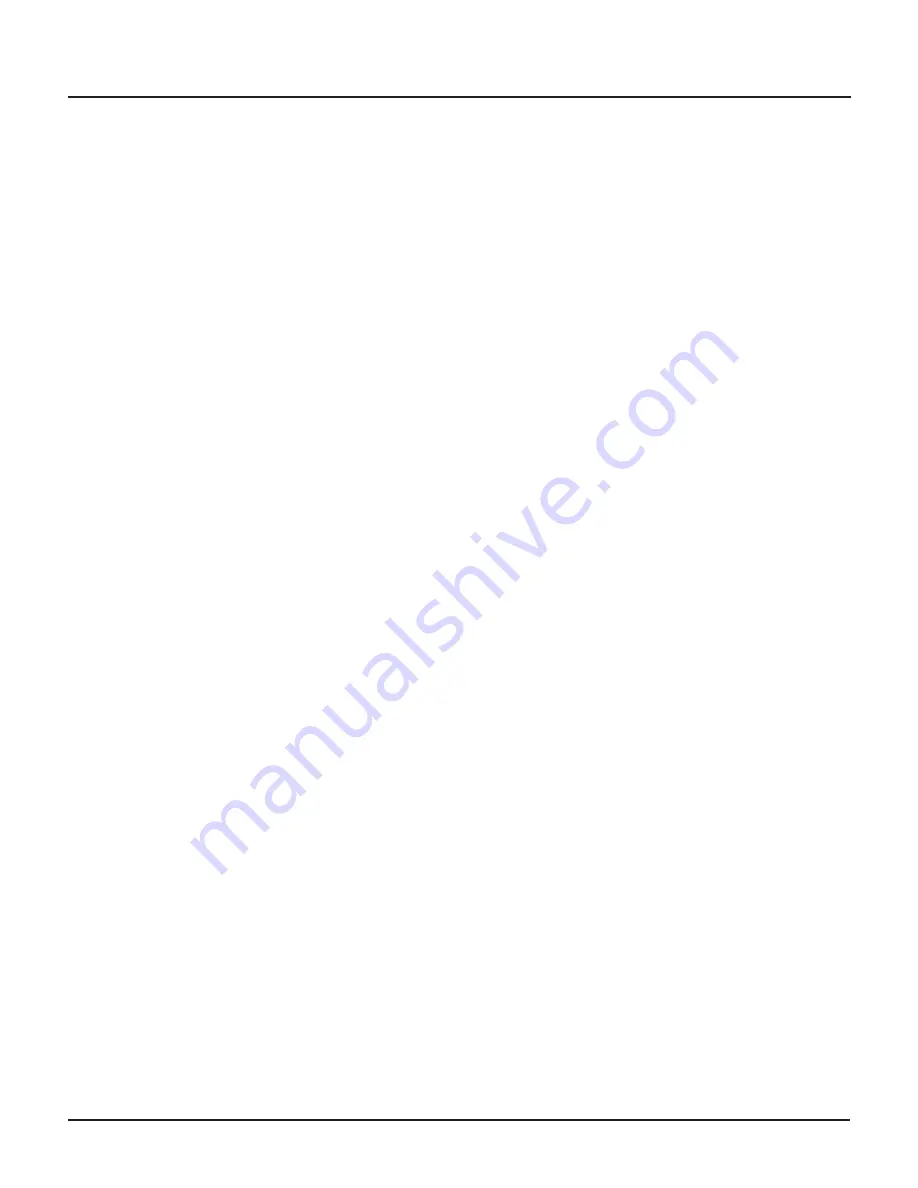
Shipping or storing the HyperJet pump
Whenever moving, storing, or shipping a Flow pump,
following these guidelines will help prevent damage
caused by movement or environmental conditions. These
instructions comply with transportation regulations.
Note:
U.S. Department of Transportation regulations
require that hydraulic fluid be transported only in sealed
containers. Before shipping, remove all hydraulic fluid
from the oil reservoir.
Service steps
1. Disconnect power and turn off inlet water.
2. Disconnect main motor lead terminations from the
motor starter in the machine power enclosure. DO
NOT CUT LEADS.
Note
: Motor leads are terminated with eye lugs and
bolted to terminations from the motor starter primary
conductors.
3. Remove water filters from housings. Empty and
clean the housings, then reinstall without filters.
4. Disconnect the plumbing from the water leakage
line.
5. Disconnect customer plumbing from the
FILTERED
WATER IN
bulkhead connection.
Install antifreeze
Notes:
•
Use Dow Chemical Dowfrost Propylene Glycol
food-grade antifreeze (or equivalent). Antifreeze,
container, pump, and hoses must be clean to prevent
contamination.
•
Antifreeze MUST NOT be introduced into an 87K
intensifier.
6. Use a small pump to force clean antifreeze through
the cooling water circuit. To ensure that the flow
control valve is open, run the pump until the oil is at
operating temperature. Otherwise, bypass the flow
control valve. A drill-motor operated transfer pump
is often adequate. Continue to pump antifreeze until
it exits the
COOLING WATER OUT
connection, then
disconnect the hose from the inlet water connection.
7. Remove water from the intensifier inlet water circuit
by emptying the filter housings and blowing out the
hoses and booster pump using compressed air.
Water in the intensifiers and high-pressure tubing
does not need to be removed.
Plug fittings
8. Plug all bulkhead connections. Tie wrap the inlet
water line and drain line.
Crating
9. The pump must be shipped on a framed and rein-
forced wooden pallet designed to isolate and sup-
port its weight and load characteristics.
10. Secure the filter bracket so it cannot vibrate.
11. Wrap a plastic band around the horizontal circum-
ference of the pump, protecting all corners with
cardboard between the strap and the cover corner.
Wrap an additional plastic band around the top and
under the frame, also protecting corners with card-
board.
12. The pump cover package must also be fully enclosed
in a rigid wooden crate for shipment.
14 | M-390
© Flow International Corporation
HYPERJET™ 94i-S AND 94i-D PUMPS
Summary of Contents for 94i-D
Page 1: ...HYPERJET 94i S 94i D M 390 REV C APRIL 2010 ...
Page 6: ...Notes 6 M 390 Flow International Corporation HYPERJET 94i S AND 94i D PUMPS ...
Page 20: ...Notes 20 M 390 Flow International Corporation HYPERJET 94i S AND 94i D PUMPS ...
Page 30: ...Notes 30 M 390 Flow International Corporation HYPERJET 94i S AND 94i D PUMPS ...
Page 40: ...Notes 40 M 390 Flow International Corporation HYPERJET 94i S AND 94i D PUMPS ...
Page 75: ...CHAPTER 7 Customer Support MS 2266 Customer Support Flow International Corporation M 390 75 ...
Page 76: ...Notes 76 M 390 Flow International Corporation HYPERJET 94i S AND 94i D PUMPS ...