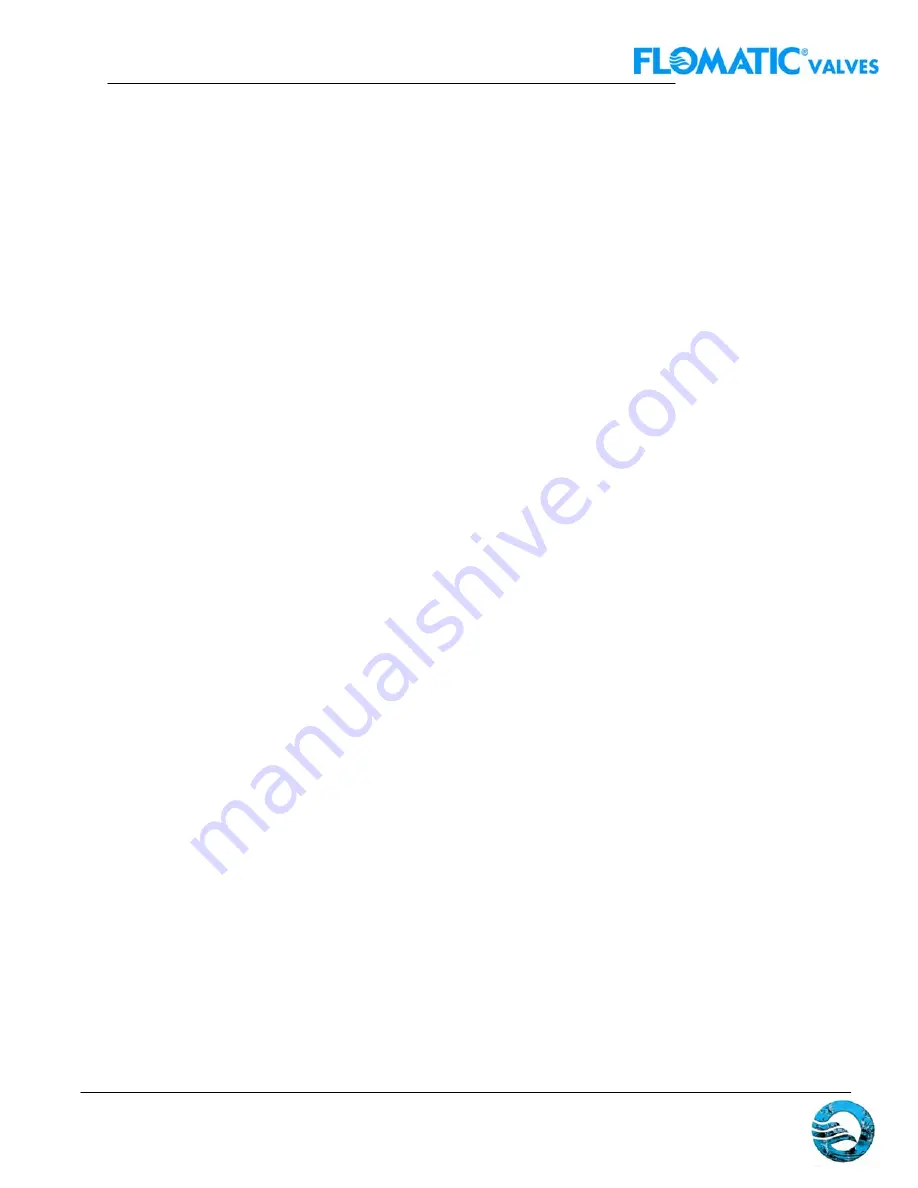
Flomatic Smart Card
TM
Model FDHC-100 (Digital High-Resolution Controller)
Configuration and Operation Manual
FDHC-100 Configuration & Operation Man. Rev 0
August 16, 2010
9 of 14
Flomatic Corporation
Glens Falls, NY 12801
Phone (518) 761-9797
Fax (518) 761-9798
in a motion greater than 1.5°, or 3) a mechanical manual override forces the 1.5° motion, provided the
mechanical motion is monitored by the feedback pot.
MOTOR 2 STALL - A fault is detected when no actuator motion is detected while the Motor 2 output is
turned on. The fault can be cleared in the same manner as a Motor 1 Stall (see above).
DOUBLE STALL - If the FDHC-100 detects no actuator motion in either direction, both motor outputs will
be disabled. The command signal cannot clear this condition; only manual operation or a mechanical
override can clear the fault. Alternatively, the FDHC-100 can be powered off and then on to temporarily
clear the fault; however, this practice should be avoided without permanently correcting the cause of
such a fault.
STALL DETECTION FEATURE
The Stall Detection feature of the FDHC-100 (see FAULT INDICATOR) essentially performs a similar
function as commonly used torque switches; however, the differences should be considered before
eliminating the torque switches. The FDHC-100 feature does not measure torque, but rather motion; if
the load is sensitive to excessive torque, the torque switches may be desirable. Since common torque
switches are mechanical devices, they can provide a fail safe feature in the event of electrical failures
(Such as shorted wires or damage to the FDHC-100). The Stall Detection feature is useful for detecting
when any of the motor wires become disconnected. However, limit switches employed in actuators
essentially disconnect one of the motor windings. The FDHC-100 will detect this as a motor stall. To
avoid this condition, the limit switches must be set outside of the operating range set by the CLOSE and
OPEN functions.
ELECTRONIC BRAKE FEATURE
The Electronic Brake feature of the FDHC-100 provides highly reliable and accurate braking of the
motor, and it is a key element in achieving high resolution. A mechanical brake can still be implemented
without interfering with the FDHC-100 operation. Mechanical brakes can be useful for providing a holding
brake in the event power to the actuator is lost. Since the Electronic Brake feature provides the
primary braking of the motor, the life of a mechanical brake is dramatically extended. Additionally, the
Adaptive Control feature of the FDHC-100 automatically compensates for changes in a mechanical
brake’s performance due to temperature or age. Note that the actuator’s limit switches should be set
outside of the operating range set by the CLOSE and OPEN functions. The Electronic Brake feature
degrades in performance if a limit switch is engaged. Limit switches exhibit wide variations, and the
FDHC-100 can position the actuator more precisely at
closed
and
open
than the limit switches. A limit
switch serves better as a fail safe device to protect against electrical failures in the actuator.
DUTY CYCLE CONTROL FEATURE
The Duty Cycle Control feature of the FDHC-100 allows actuators rated at 25% duty or more to be
safely used in automated valve applications. The FDHC-100 accurately monitors the relative heating of
the motor and automatically duty cycles the unit at a safe level when a process becomes unstable, or if a
control loop is not properly set. While the thermal switch in the motor protects the motor from
overheating, thermal switches can shutdown the actuator for ten minutes or more. Further, typical
thermal switches do not activate until temperatures inside the actuator become too high for other
components in the actuator. The Duty Cycle Control feature allows continuous operation of the motor
until it detects an excess heat build up in the motor (usually well below the limit of the thermal switch).
At that time, duty cycle operation is automatically enabled and continues until the motor cools enough to