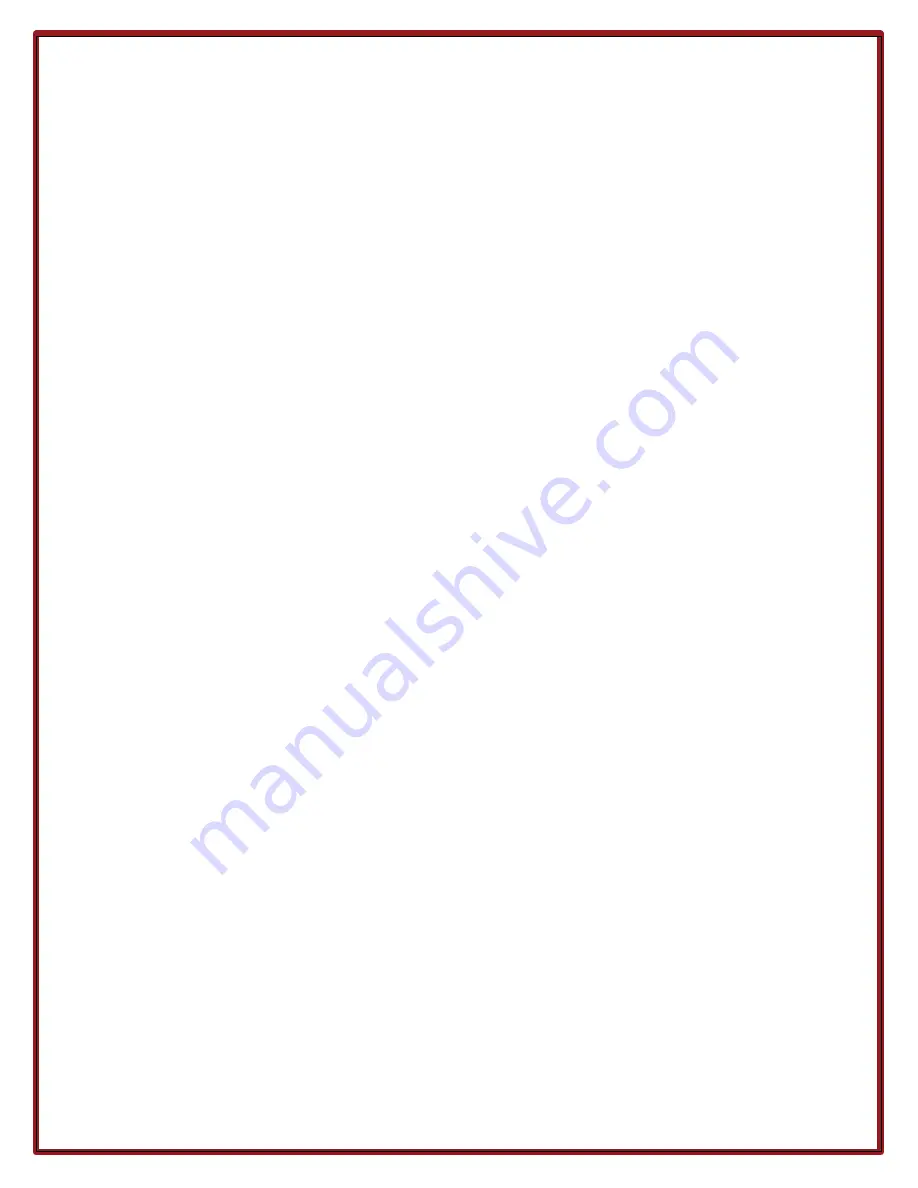
1/4/2021
REV. 002
27
TROUBLESHOOTING
Refer to the following list of common problems when it appears the FlexArm is not working properly. Most of
these are resolvable by in-house technicians or operators. Compare any problems with those given in the
examples below. Help is just a phone call away; always contact Factory Service at
800-837-2503
with any
questions or concerns about operating the
FlexArm Tapping Machine.
1.
The tap is not maintaining perpendicularity.
a)
Check all screws and bolts to make sure they are tight and secure.
b)
Check to make sure the angle mount washer and bolt are tight against the base.
c)
Check the flatness of the surface on which the unit is mounted.
d)
Check the motor mount screws. Make sure they are tight and are holding the motor securely in
the mount.
e)
Check the wear on the rear plates and rear pin. Return the unit to Factory Service if the unit
“rocks” on the rear pin, the holes in the plates have “wallowed”, or the pin connections are
worn.
2.
The air motor does not have enough power to drive the tap.
a)
Check the air pressure to the motor; it must be 90-110 psi at the motor. Depending on the rpm
of the motor, the compressor will need to supply 20-30cfm.
b)
Remove any quick disconnects in the airline leading to the unit. Quick disconnects can reduce
both volume and pressure.
c)
Lubricate the tap with the proper lubricant for the material being worked.
d)
Check the amount of oil being dispensed through the lubricator and adjust to
1-3 drops of oil
per minute.
Lack of oil will reduce speed and power.
e)
If the unit has been sitting a while between jobs it may be necessary to add 4-5 drops of oil
directly into the motor inlet to place oil on the vanes before running. The lubricator should be
periodically checked to ensure that the flow rate of 1-3 drops per minute is maintained.
f)
Contact Flex Machine Tool Service if the motor has not been operational for more than 6
months; most likely the motor needs to be thoroughly cleaned and the vanes need to be
replaced.
3.
The motor has stopped running completely.
a)
Disconnect the air supply. Check to see if the motor can be turned by hand.
b)
Motor lock up is normally the result of broken vanes, faulty bearings, or a broken gear tooth.
Replacement parts can be ordered from Flex Machine Tools.
c)
If the motor is less than 1 year old, return to Flex Machine Tools for warranty.
All items except for blades, O-rings, and springs are covered for one year.
d)
Check the type of oil being used in the lubricator. Use only an ISO viscosity grade 32 hydraulic
or spindle oil; do not use synthetic oils or oils advertised for air motors. Using the incorrect
lubricator fluid will cause premature wear on the vanes and lead to motor lock up.
e)
Check the amount of oil being dispensed through the lubricator and adjust to 1-3 drops of oil
per minute. Excess oil can create a gummy residue and lack of oil will cause the blades to get
dry, crack and eventually lock up the motor.
Summary of Contents for FLEXARM RNR
Page 15: ...1 4 2021 REV 002 15 DRAWING RNR...
Page 16: ...1 4 2021 REV 002 16 PARTS AND ASSEMBLY GEAR BOX...
Page 17: ...1 4 2021 REV 002 17 PARTS AND ASSEMBLY...
Page 21: ...1 4 2021 REV 002 21 RNRM PARTS AND ASSEMBLY...
Page 23: ...1 4 2021 REV 002 23 RNR SEMI TAP LUBE SYSTEM...
Page 24: ...1 4 2021 REV 002 24 RNR SEMI TAP LUBE SYSTEM...