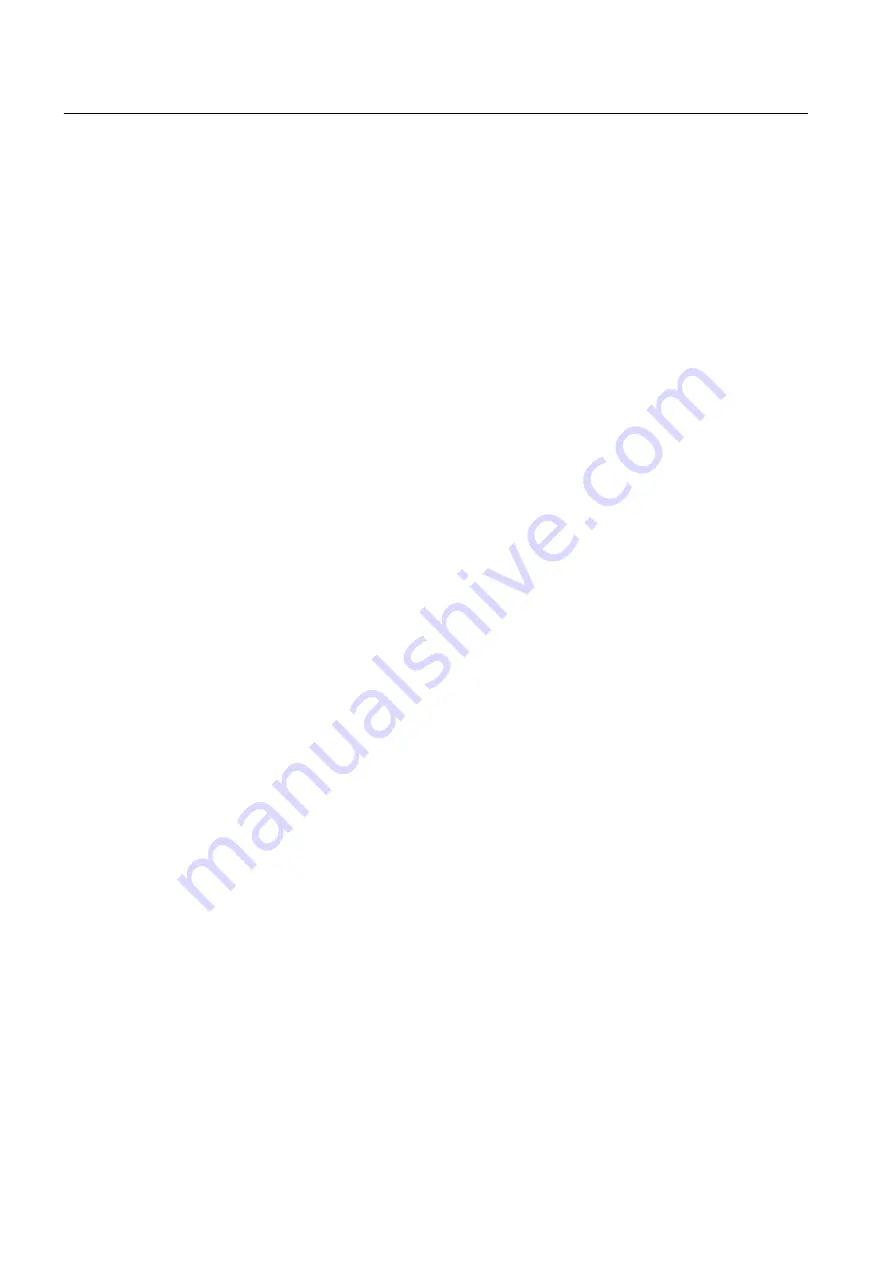
● Coupling parts interchanged and hence not assigned to the specified shaft.
● Stipulated locking elements to prevent axial movements not installed.
● Stipulated tightening torques not adhered to.
● Bolts inserted dry or greased.
● Flange surfaces of screwed connections not cleaned.
● Alignment and/or shaft misalignment values not set in accordance with the instructions.
● Coupled machines were not correctly connected to the foundation so that a shifting of the
machines leads to an impermissible displacement of the coupling parts.
● Coupled machines not earthed adequately.
● Coupling guard used is not suitable.
Maintenance-related causes
● Stipulated maintenance intervals not adhered to.
● Spare parts that were used were not original spare parts from Flender.
● Flender spare parts that were used were old or damaged.
● Leak in the area of the coupling not detected so that chemically aggressive substances
damage the coupling.
● Indications of faults, such as noise or vibration, were not heeded.
● Stipulated tightening torques not adhered to.
● Alignment and/or shaft misalignment values not set in accordance with the instructions.
Specific installation-related and maintenance-related causes
● Cam ring (20) not fitted.
● Fitted cam ring (20) heated up excessively when applying heat to the coupling parts.
7.2.3
Correcting faults
7.2.3.1
Replacing wearing parts
Cam rings (20) are subject to wear and this wear can result in torsional backlash.
Procedure
1. Check the wear on the cam ring (20) (see section Maximum permissible torsional
2. Replace the cam ring (20) where appropriate (see section Replacing wearing parts
(Page 40)).
Operation
7.2 Faults - causes and rectification
BIPEX-S 3410en
36
Operating Instructions 10/2017
Summary of Contents for BCC
Page 2: ...21 09 2017 12 18 V6 00 ...
Page 10: ...Introduction 1 3 Copyright BIPEX S 3410en 10 Operating Instructions 10 2017 ...
Page 22: ...Description BIPEX S 3410en 22 Operating Instructions 10 2017 ...
Page 32: ...Commissioning BIPEX S 3410en 32 Operating Instructions 10 2017 ...
Page 44: ...Service and support 9 1 Contact BIPEX S 3410en 44 Operating Instructions 10 2017 ...
Page 46: ...Disposal BIPEX S 3410en 46 Operating Instructions 10 2017 ...
Page 65: ......