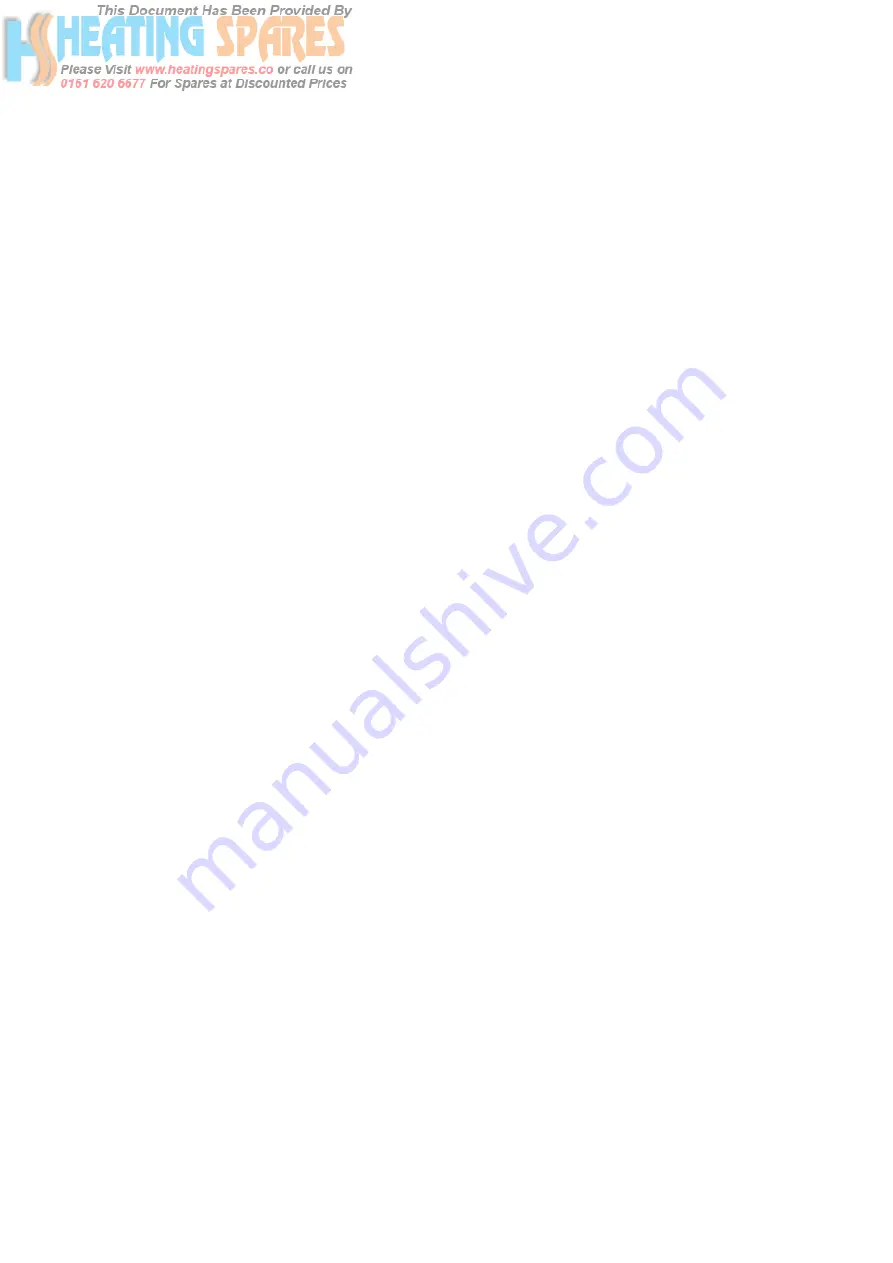
Supplied By www.heating spares.co Tel. 0161 620 6677
4.2.6
Swap the valve mounting plate onto the new valve by unscrewing the
two M5 nuts and bolts holding it in position .
4.2.7
Re-assemble with new valve in reverse order.
4.3
Removing the Battery Pack
4.3.1
Disconnect the wire from the battery pack, located at the bottom
L/H/S of the combustion chamber.
4.3.2
Lift the battery pack out of its mounting cradle.
4.3.3
Re-fit the new battery pack in its cradle and re-fit the wire.
4.4
Removing the Pilot Assembly
4.4.1
Isolate the gas supply
4.4.2
Remove the fender as described in section 3.3, on page 17
4.4.3
Remove the glass frame assembly from the fire, as shown in section
2.8 on page 13.
4.4.4
Remove the ceramic coal forms from the combustion chamber
taking care not to damage them.
4.4.5
Loosen the pilot pipe, disconnect the ignition lead from the electrode,
and remove the thermocouple from the pilot body.
4.4.6
Remove the two fixing screws which secure the pilot assembly to the
pilot mounting panel in the base of the combustion chamber.
4.4.7
Remove the pilot assembly.
4.4.8
Re-assemble with an new pilot assembly, and gasket, ensuring that an
even seal around the pilot assembly is obtained. Carry out a gas
tightness test after re-assembly.
4.5
Replacing the Touch Control Switch
4.5.1
Remove the right hand side panel from the fire. Remove the touch
control switch by releasing the nuts that hold it in position on the inside
face.
4.5.2
Remove the connecting wires from the top left hand side of the
control valve.
19