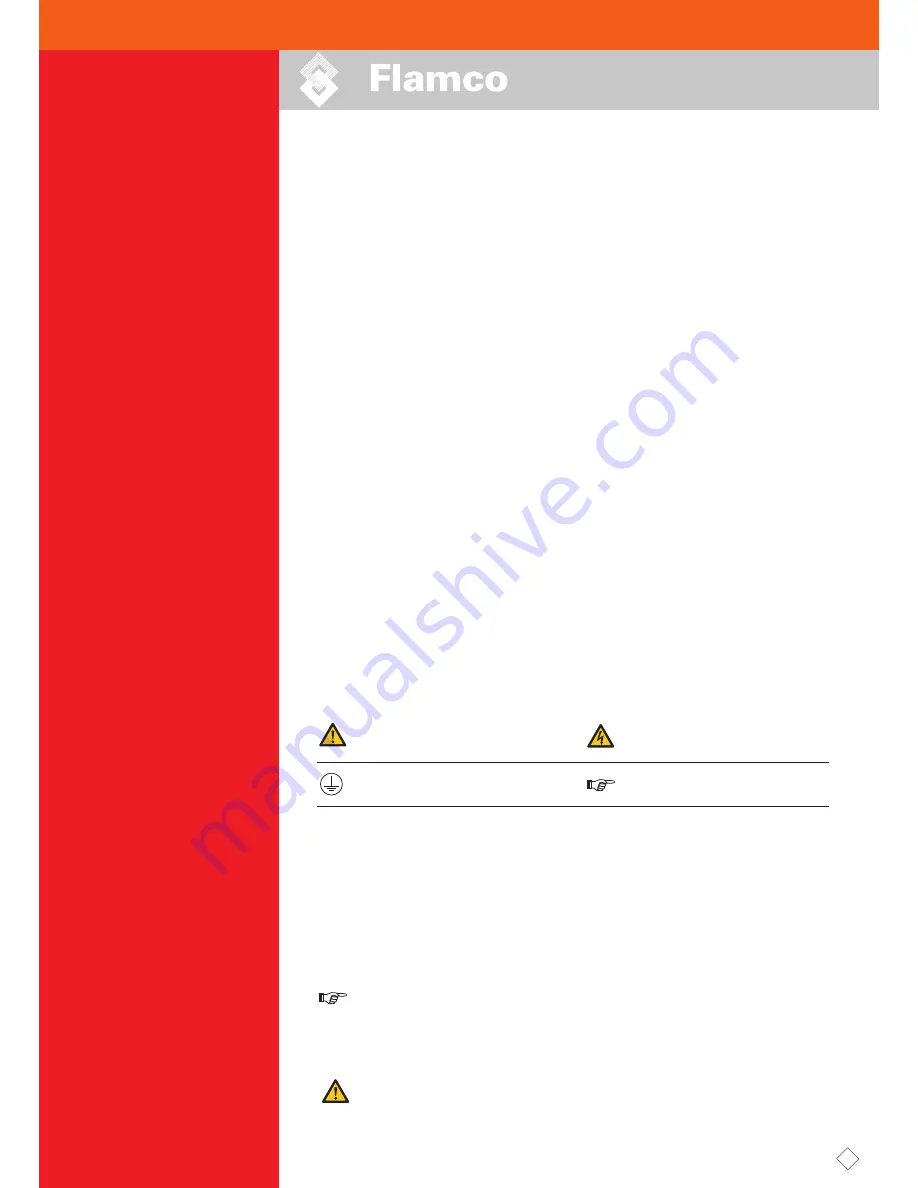
3
Installation and
operating instructions
FLAMCO-FILL PE INSTALLATION AND OPERATING INSTRUCTIONS
TP.04/02/09.EN
Edition 2009 / EXP
1
General
1.1
About this manual
This manual includes technical specifications, instructions and explanations that helps to use this automat safely.
Read and understand all the instructions before you transport, install, commission, restart, operate or maintain the
automat.
1.2
Other supplied documentation
General information of additional components, such as the pump and the sensors, is included in this manual. If
additional documentation is supplied, also follow the instructions in those.
1.3
Use of Flamco products
According to order or execution complementary documentations can be added. Follow the positions performed
in the dispatch papers.
1.4
Further help and information
Contact your local supplier for additional services as:
Training
•
Maintenance agreements.
•
Service contracts.
•
Repairs and improvements.
•
2
Safety
2.1
Intended use
The automat is suitable for closed heating and air conditioning systems:
in which losses of system water are to be refilled;
•
are to be filled for the first time.
•
2.2
Important information
The automat has safety devices intended to prevent injury and damage. Use the automat in the following way:
Have the installation be carried out by qualified personnel.
•
Comply with local legislation and guidelines.
•
Do not make modifications to the automat without prior written permission of Flamco.
•
Make sure that all automat covers and doors are closed when operating the automat.
•
Do not touch live voltage. The sensor units and the capacity pressure sensors operate with extra low safety
•
voltage.
Flamco shall not be liable for any losses arising from the non-observance of safety conditions or as a
consequence of the disregard of standard precautionary measures when performing such services as transport,
installation, commissioning, re-starting, operation, maintenance, testing and repair, even in the event that these
are not expressly described in these instructions.
2.3
Signs in this manual
Identifies a hazard that could lead to personal
injury including death/damage to the
automat, damage to other equipment and/or
environmental pollution.
Identifies an electric hazard that could
lead to personal injury including death/
damage to the automat, damage to other
equipment and/or environmental pollution.
Earthing
Important information.
2.4
Specifications
The construction of the automat is designed in accordance with the norms DIN EN 1717 and DIN 1988.
2.5
Safety devices
The automat does not contain any safety components that prevent that the operation pressure and the
operation temperature range are exceeded or go below a limit. Install components for the limitation of
pressure and temperature in the system.
2.5.1 Avoiding excessive pressure
Appropriate safety valves that prevent that the maximum operation pressure is exceeded:
Open not later than the maximum allowable working pressure is reached.
•
Can conduct the occurring volume flow (including the maximum possible refilling volume) up to the 1.1-fold
•
of the maximum operation pressure;
Have a proven reliability or are certified.
•
Do not narrow the inlet or outlet piping of the safety valve.
2.5.2 Avoiding excessive temperature
Appropriate safety components:
Guarantee that the operation temperature range is not exceeded at any point of the system;
•
Are approved and tested on operation safety.
•
Activate the pressure and temperature safety devices and check them regular on proper working.