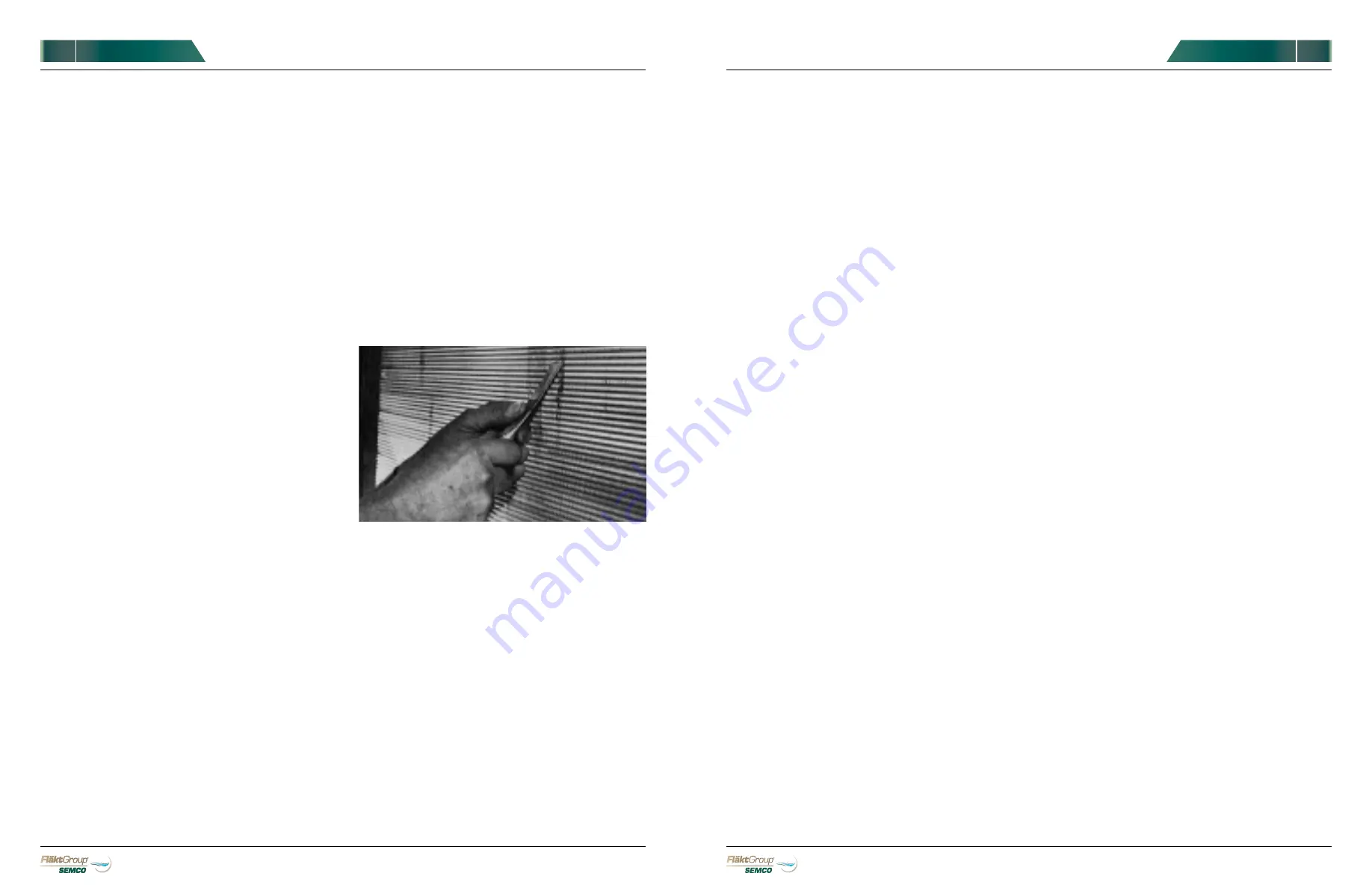
25
24
SPECIALIZED
HEALTHY
AIR SOLUTIONS
SPECIALIZED
HEALTHY
AIR SOLUTIONS
OWNER’S MANUAL
OWNER’S MANUAL
ASCENDANT
™
ASCENDANT
™
SPECIALIZED
HEALTHY
AIR SOLUTIONS
OWNER’S MANUAL
Check shafts and fan wheels every three months for
dirt buildup, corrosion and cracks, and other signs of
stress or fatigue. Clean as necessary, and apply new
coatings when appropriate.
NOTE:
After applying new coatings and/or applying welds
to the fan, be sure to check the assembly’s balance. The
application of welds and coatings can cause an imbalance.
MAINTENANCE: FANS
MAINTENANCE: FAN MOTORS
•
Motors will operate effectively for years if operated
by proper current and kept clean, dry and properly
lubricated.
•
Clean motors every six months. Use moderate air
pressure (25-30 psi) to blow away dirt from vent
fins and other accessible areas.
NOTE
:
Keep areas surrounding the motors clear so
air can circulate freely through the motor to cool it.
•
Inspect connections every six months. Watch for
frayed or exposed wiring and loose connections.
Repair or tighten as necessary.
•
Check operating current every six months. Make
sure that motors continue to operate at faceplate
current or below.
•
Check for vibration and for mounting-bolt tightness
every six months. Tighten any loose mounting bolts.
Make sure that motor runs smoothly without
vibrating.
•
Lubricate motor bearings with one or two squirts
of high grade, lithium-based grease annually
(Chevron SRI #2 or similar recommended). Do
not over lubricate! Consult motor manufacturer
for detailed lubrication instructions.
MAINTENANCE: DAMPERS
•
Every 3 months, inspect dampers, arms, bars, and
control rods and shafts for dirt and other foreign
matter that would impede normal movement and
prevent blades and seals from seating properly.
Clean as necessary.
•
Inspect seals every three months to be sure that
none have pulled loose or deteriorated. If
replacement is required and the seal can be
replaced, remove it and replace with a new
seal of the same shape, design and material used
originally. Do not use a different size or shape. In
some instances, the seal may not be replaceable
and it may be necessary to replace the entire
blade.
•
No lubrication required. Damper shafts utilize non-
lubricating bearings.
MAINTENANCE: COILS
Heating and cooling coils function at peak efficiency
when clean and free of foreign matter. Frequent visual
inspections should be made, and any built up dirt and
foreign matter should be removed. A fin comb may be
required to remove matter entangled in fins or coils
(See
FIGURE 32
), but flushing with water under normal
local pressure will remove most particulates.
FIGURE 32.
A fin comb may be used to remove matter
entangled in fins, as well as to straighten fins. But normally,
flushing coils with water under normal pressure will remove
most matter.
•
An acid or alkaline coil cleaner is recommended
every 1 or 2 years, depending upon the degree of
oxidation, to thoroughly clean and brighten coils
and fins.
•
Local water conditions may make it necessary to
treat chilled water systems, hot water systems and
steam systems to control corrosion, sludge and/or
metal oxides. In some water supplies, scale
removers and inhibitors may also be required.
•
Cooling coils – If water in the system will be
exposed to outdoor temperatures that are below
freezing, either drain the system before
temperatures dip below 32°F, or add glycol to the
system to prevent freezing.
THIS PAGE WAS INTENTIONALLY LEFT BLANK