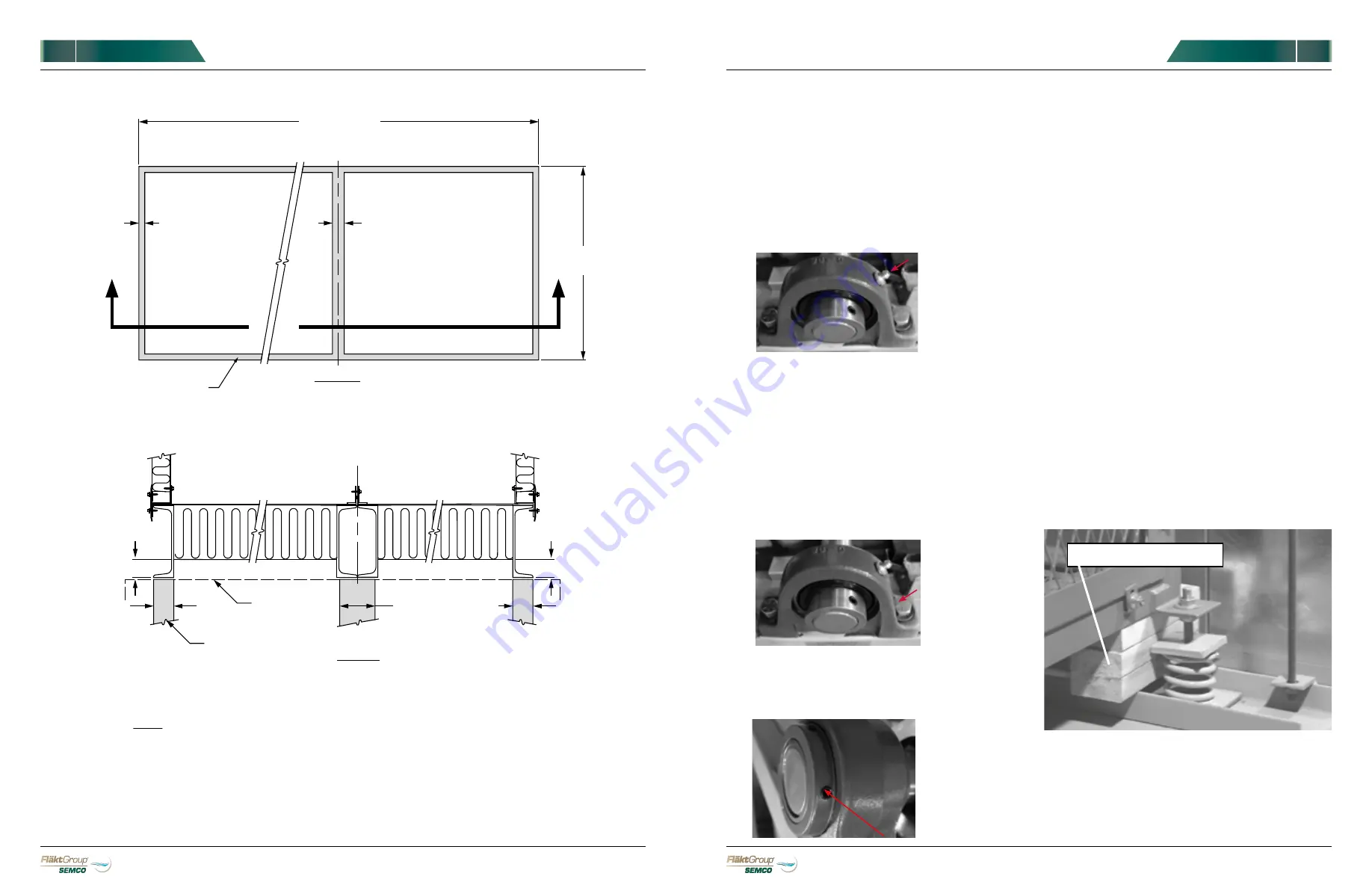
11
10
SPECIALIZED
HEALTHY
AIR SOLUTIONS
SPECIALIZED
HEALTHY
AIR SOLUTIONS
OWNER’S MANUAL
OWNER’S MANUAL
ASCENDANT
™
ASCENDANT
™
SPECIALIZED
HEALTHY
AIR SOLUTIONS
OWNER’S MANUAL
All necessary active desiccant wheel components
have been installed at the factory and tested for
proper operation prior to shipping. Before start up,
the following steps should be taken:
1)
Pump grease into the two rotor bearing grease
fittings using a high quality NLGI No. 2 grease
(See
FIGURE 18
).
ACTIVE DESICCANT WHEEL
FIGURE 21.
Fan shipping restraints located at the base of
the fan.
Remove wooden blocks
All necessary system fans and fan motors are installed
at the FläktGroup SEMCO factory. However, before
attempting to operate them, a pre-startup inspection is
recommended.
1)
Make sure all power to the fan motors is off.
2)
Remove wooden blocks and any shipping
restraints and discard (See
FIGURE 21
).
FANS
FIGURE 18.
Pump
grease into two
rotor bearing
grease points, one
on each side of
the rotor.
FIGURE 20.
The
bearing set
screws, one on
each side of the
rotor, should
be checked for
tightness every
six months.
FIGURE 19.
Inspect bearing
collar to ensure
all bolts and
screws are tight.
2)
Inspect the rotor visually. It should be well
centered in its casing and should not tilt in any
one direction. If alignment is not suitable, contact
FläktGroup SEMCO.
3)
Inspect the bearing bolts and the Allen screws
on the bearing collar to ensure that all are tight
(See
FIGURE 19
). Tighten any loose screws and
bolts. The bearing bolts should be torqued to 50
ft-lbs. The bearing set screws should be torqued
to 15 ft-lbs.
4)
The bearing set screws should be checked
periodically for tightness. A bearing set screw is
located on each side of the rotor (See
FIGURE 20
).
5)
The bearing set screws should be torqued to
15 ft-lbs.
6)
Upon unit startup observe the wheel in operation
and verify that the rotor does not bind. If binding
occurs in a new unit, it is usually caused by the
seal or freight damage.
ADJUSTING THE SEALS
Maintaining correct seal adjustment is vital to the
effective operation of the unit. The face and perimeter
seals are designed to gently contact the face of the
wheel and wheel rim angle to prevent air from leaking
across or around the wheel sections. Adjustment of the
seals is simply done by loosening the screws holding the
seal clips in place, adjusting the seal so it just contacts
the surface of the wheel/rim, and then re-tightening the
screws.
3)
Inspect the fans:
•
Check fan bolts and mountings for tightness.
Tighten loose screws and bolts.
SECTION
UNIT BASE WHEN MOUNTING
ON PAD OR STRUCTURAL GRID
PLAN VIEW
TYPICAL UNIT WITH HOUSEKEEPING PAD
OR STRUCTURAL GRID SUPPORT
UNIT LENGTH
UNIT PERIMETER
UNIT
WIDTH
4"
MINIMUM
SUPPORT AT
FIELD JOINTS
2"
MINIMUM
SUPPORT AT
UNIT PERIMETER
2"
MINIMUM
SUPPORT AT
UNIT PERIMETER
NOTES
1. UNIT SUPPORT IS REQUIRED
AROUND THE ENTIRE
PERIMETER AND ALONG BOTH
SIDES OF ANY FIELD JOINTS.
2. WHEN UNITS REQUIRE FIELD
JOINTS, SUPPORT SHOULD BE
LEVEL TO 1/16" BETWEEN FIELD
JOINTS.
2" WIDE SUPPORT AT
UNIT PERIMETER
FIELD JOINT
CENTERLINE
FIELD
JOINT
CONCRETE PAD
(BY OTHERS)
2"
2"
4" WIDE MINIMUM
SUPPORT AT
FIELD JOINTS
STRUCTURAL GRID
(BY OTHERS)
MOUNTING DETAILS, GRID OR PAD SUPPORT