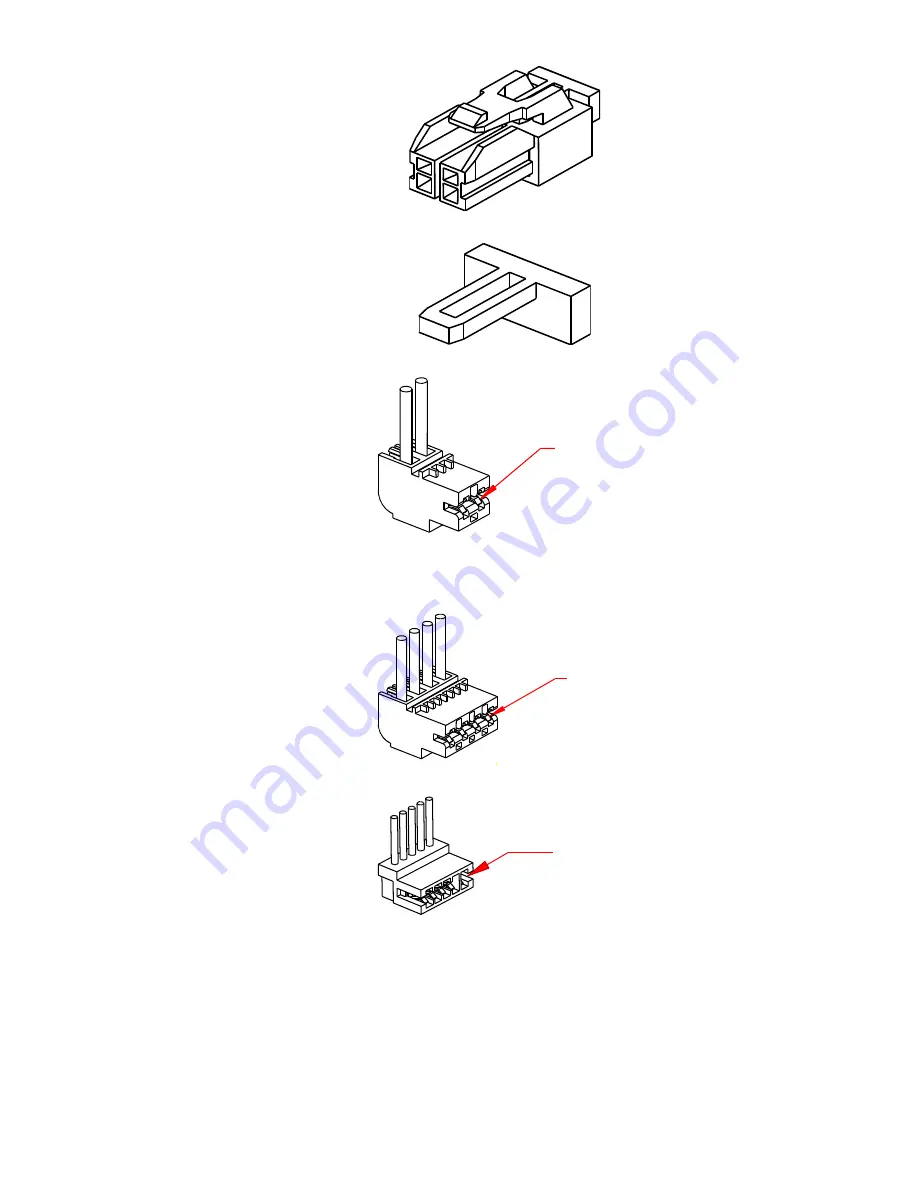
840653
73
881593 MOLEX PLUG MALE 51138-0200
881594 MOLEX RETAINER 51140-0205
PIN 1
881588 STOCKO 9290-02-AB01-000-960 (Mains cord)
881599 STOCKO 9290-02-BA01-000-960 (Defrost Heater)
881600 STOCKO 9290-02-EE01-000-960 (Run Capacitor)
Note that in the part names of these connectors, the -02- refers to it being a 2 way connector, and the -
AB01- (for example) refers to the coding of the connector. Stocko is the manufacturer of these connectors.
PIN 1
881591 STOCKO 9290-04-EF02-000-960 (Compressor cable)
PIN 1
New Edge connector series with internal coding – note the wall.
Note that to minimize the number of spare parts that need to be carried, these coded connectors are to be
replaced with their un-coded equivalents.
Summary of Contents for RB36S25MKIW
Page 1: ...840653 Service Manual CoolDrawer Models RB36S25MKIW RB90S64MKIW ...
Page 12: ...840653 12 3 4 Integrated Panel Preparation ...
Page 14: ...840653 14 3 5 Create Cut Outs In Frame 3 6 Locate And Secure Install Brackets ...
Page 15: ...840653 15 3 7 Attach Inlet And Outlet Vent Ducts 3 8 Attach Power Cord And Trim Brackets ...
Page 16: ...840653 16 3 9 Move Product Into Cavity 3 10 Fit Drawer Panel Attachment Hooks ...
Page 17: ...840653 17 3 11 Attach Drawer Panel To Front Of Drawer ...
Page 18: ...840653 18 3 12 Secure Trim Brackets To Cabinetry 3 13 Attach Trims To Sides Of Cabinetry ...
Page 19: ...840653 19 3 14 Attach False Panel 3 15 Check Operation ...
Page 53: ...840653 53 11 WIRING DIAGRAMS Ω Ω Ω Ω Ω Ω Ω Ω Ω Ω ...
Page 54: ...840653 54 ...
Page 77: ...840653 77 ...