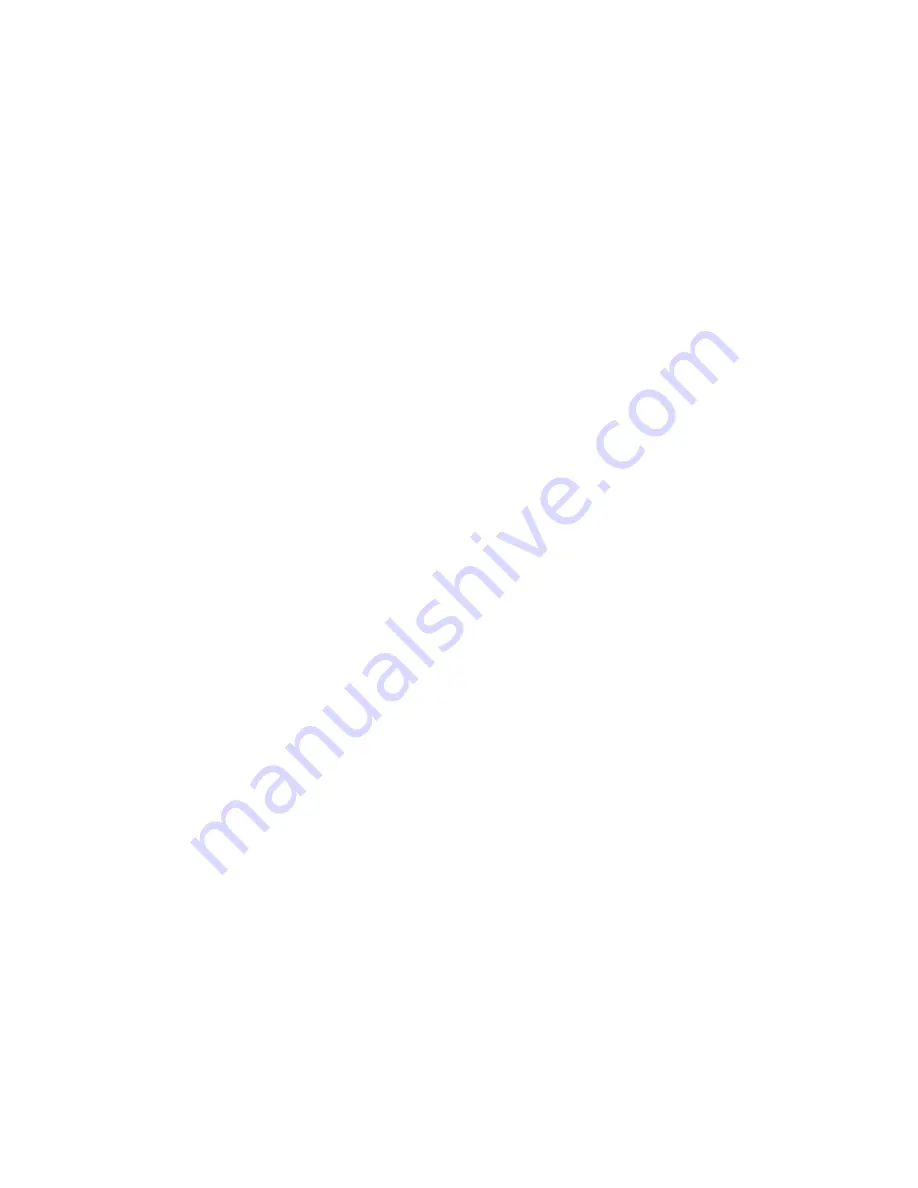
517766
March 2003
- 33 -
50.
(00110010) Phase 2 to 6 - Hot Valve Faulty (digital)
The Motor Controller module has measured a voltage from the valve diagnostic
circuit that indicates the hot valve is faulty. The most likely cause is that the valve
harness has not been connected correctly or the valve is open circuit. See fault
code 48 for service procedure.
Note: Phase 5 can give a fault code 50 when the smart drive powers off while
spinning. There will actually be no fault if this has happened.
51.
(00110011) Phase 5 and 6 Eco - Diverter Valve Fault
Primary:
The motor controller has registered a drop in water level in the
recirculation phase of the wash cycle, water is being drained instead of recirculated.
Or water has been sprayed onto the valve from an external source and caused the
solenoid to blow.
Action:
Turn the power off at the machine but leave the power on at the wall, then measure
the voltage across the terminals of the wax actuator, if a reading of 120V is
achieved the motor controller has failed due to the valve and both will need to be
replaced.
Secondary:
Check for blockage in the valve itself or a broken hinge mechanism.
52.
(00110100) Phase 5 and 6 Eco - Diverter Top-up Fault
More than 6 attempts to top-up the water level in the tub, this then signifies the
valve has not closed and is diverting to drain, or the top-up was not increasing quick
enough suggesting the valve has a blockage and is also draining.
Primary Source:
Diverter valve
Action:
Remove the diverter valve and check for blockages or broken hinge
mechanism.
Secondary Source:
Wax Solenoid
Action:
Check the resistance of the wax solenoid, also look for corrosion on the terminals
(greenie deposit) resistance range will be between 0.7k
W
and 2.5k
W
. Values are
dependant on ambient temp and when the valve was last actuated. Anything
outside of these values should be automatically replaced.
53.
(00110011) Phase 2 to 6 - Rotor Position Sensor Step Fail
The motor controller has attempted a motor step test and has found that the motor
has not stepped in the correct direction. It has detected that the motor is connected
and that the motor drive is operational. The rotor position sensing system is at fault
here.
Primary Source:
Wiring.
Action:
Check the Rotor Position Harness for continuity and that the connectors are
correctly to the Rotor Position Sensor and the Motor Controller.
Secondary Source:
Rotor Position Sensor
Action:
Check the Rotor Position Sensor patterns with a RPS Tester, if faulty fit a
new Rotor Position Sensor.
Tertiary Source:
Motor Controller module.
Action:
Replace the Motor Controller module as the sensing circuitry may be faulty.
Summary of Contents for ecosmart GWL11
Page 2: ...517766 March 2003 ...