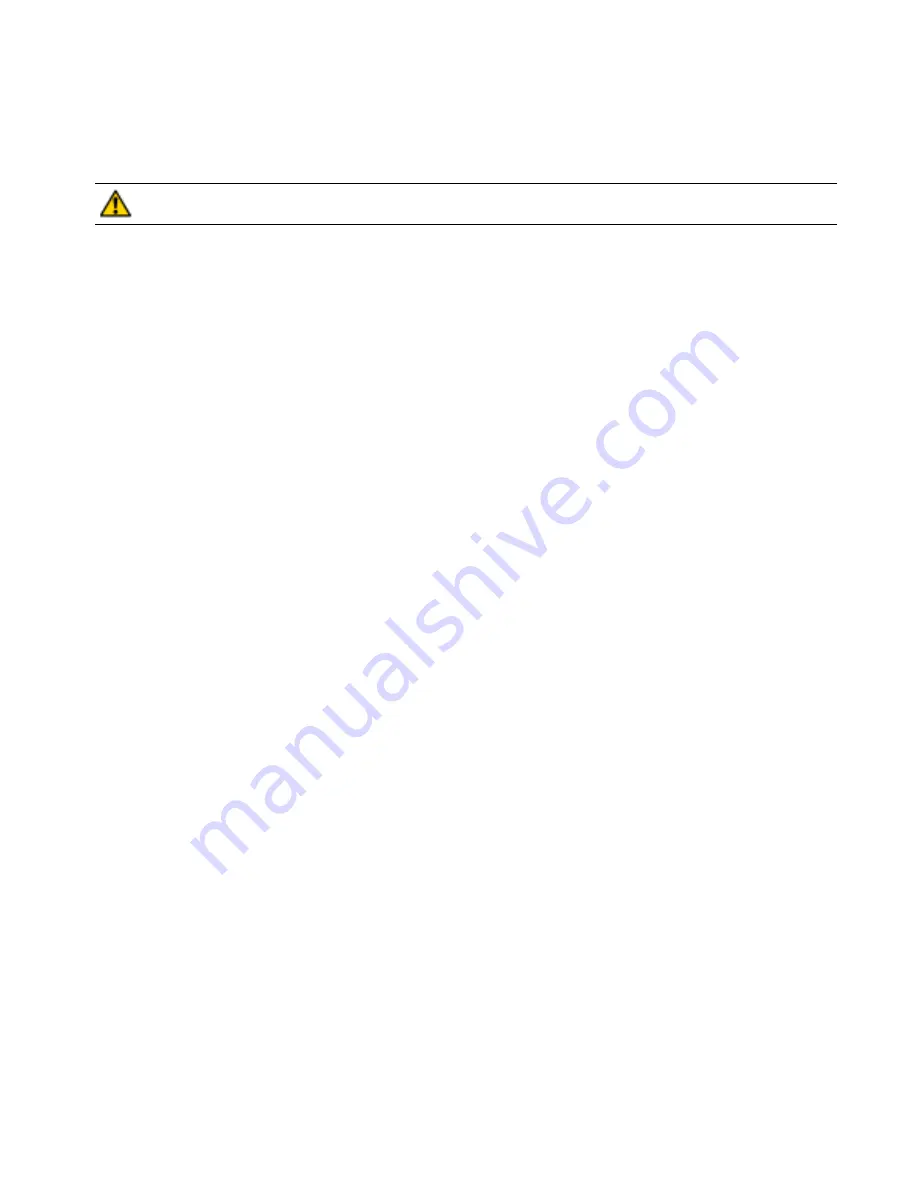
3. Inspect drain pan cleanliness annually and clean as required. Inspect the condensate drain prior and periodically
during the cooling season for proper draining.
4. Check blower motor and wheel for cleanliness each heating and cooling season. Clean as required.
5. Inspect electrical connections for tightness and controls for proper operating each heating and cooling season.
Service as required.
WARNING:
As with any mechanical equipment, personal injury can result from sharp metal edges, etc.,
therefore, care should be taken when removing and working on metal parts.
Maintenance Updates
A current copy of the Maintenance Program log can be found at
www.firstco.com
under Product Informa-
tion.
15