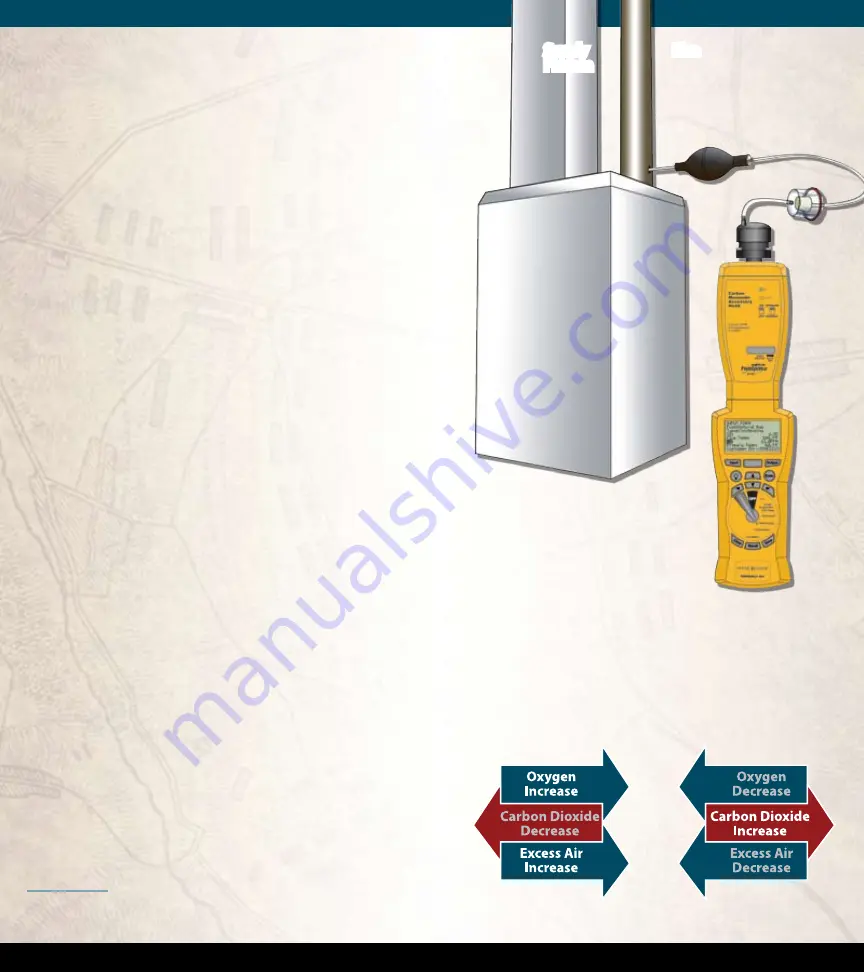
66
WWW.FIELDPIECE.COM WWW.FIELDPIECE.COM WWW.FIELDPIECE.COM WWW.FIELDPIECE.COM WWW.FIELDPIECE.COM WWW.FIELDPIECE.COM WWW.FIELDPIECE.COM WWW.FIELDPIECE.COM WWW.FIELDPIECE.COM WWW.FIELDPIECE.COM WWW.FIELDPIECE.COM
WWW.FIELDPIECE.COM WWW.FIELDPIECE.COM WWW.FIELDPIECE.COM WWW.FIELDPIECE.COM WWW.FIELDPIECE.COM WWW.FIELDPIECE.COM WWW.FIELDPIECE.COM WWW.FIELDPIECE.COM WWW.FIELDPIECE.COM WWW.FIELDPIECE.COM WWW.FIELDPIECE.COM
Combustion Basics
Combustion is the rapid oxidation of fuel. Oxygen
from air (20.9% oxygen & 79.1% Nitrogen) is used to
burn fuel producing heat. The appliances installed and
serviced by technicians rely on clean efficient flames to
produce the energy needed to heat homes and hot water,
etc. Combustion testing is necessary to maximize the ef-
ficiency of the combustion systems and to minimize the
harmful emissions produced. Carbon monoxide and
carbon dioxide (greenhouse gas emissions) are products
of combustion. Proper tuning of the combustion pro-
cess by combustion testing will reduce the production
of harmful carbon monoxide and decrease the amount
of fuel burned through the increase in efficiency.
Combustion efficiency can typically be increased by
creating a more balanced Air to Fuel ratio. The ratio of
air to fuel determines how much CO
2
is produced and
how efficient the flame is.
Tuning of the O
2
, CO
2
, excess air, stack temperature,
and temperature rise to match the appliance manufac-
turers specifications will increase the efficiency and help
to maximize the performance and life expectancy of the
equipment. It is also safer because the equipment will
produce minimal CO as a byproduct.
A properly tuned atmospheric natural gas or pro-
pane fired appliance will have approximately 6 to 9% O
2
in the flue gases. Fuel oil appliances with flame retention
burners will have approximately 3 to 7% O
2
in the flue
gases. For more details see the chart on page 32.
Testing and adjustment to the combustion process
ensures that the highest combustion efficiency is safely
achieved, thereby, reducing the overall amount of fuel
used in producing the energy needed. It is still necessary
to test and adjust the appliance to the manufacturer's
specification for airflow in the duct system, temperature
rise across the heat exchanger, and anything else that
may need testing. Testing and balancing of appliances
to meet manufacturers’ specifications helps to ensure
maximum system efficiency and equipment longevity.
8
Combustion testing does not take into account start
up losses, standby losses, cabinet/boiler body losses, or
distribution losses in ducts or piping.
8 Content adapted from Erik Rasmussen's book Combustion Analysis and Fuel
Efficiency
Figure 34. Entering the CO measurement for the Combustion Test us
ing an ACM3 Carbon Monoxide Head and the pump that's included
with the AOX2 Combustion Check Head.
Below is Fig 4-9 from the book Combustion Analy
-
sis and Fuel Efficiency, Erik Rasmussen ESCO Press
2007.
Supply
Plenum
Flue