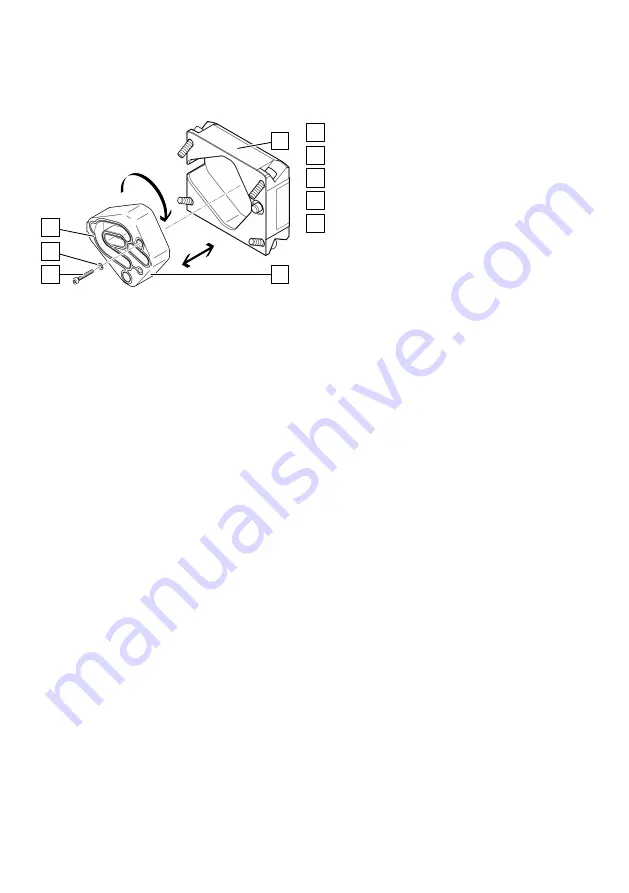
24
Festo — VTOP — 2021-07
Modification
12.2
Reversing effective direction
1
4
3
2
5
Fig. 22: Reversing effective direction
1
End plate VABA
2
Reversing plate
3
Screw
4
Spring washer
5
Seal
1. Unscrew the screws of the end plate VABA.
2. Remove the end plate VABA.
3. Unscrew the screw of the reversing plate.
4. Remove the reversing plate from the end plate VABA.
5. Check that the seals on the reversing plate are seated correctly.
6. Replace the reversing plate in the end plate VABA.
7. Attach the split washer to the screw of the reversing plate.
8. Tighten the screw of the reversing plate. Tightening torque: 0.9 Nm ± 10%
9. Assemble the end plate VABA with the module in the correct position.
10. Apply the screws of the end plate VABA and tighten evenly. Tightening torque: 10 Nm ± 20%