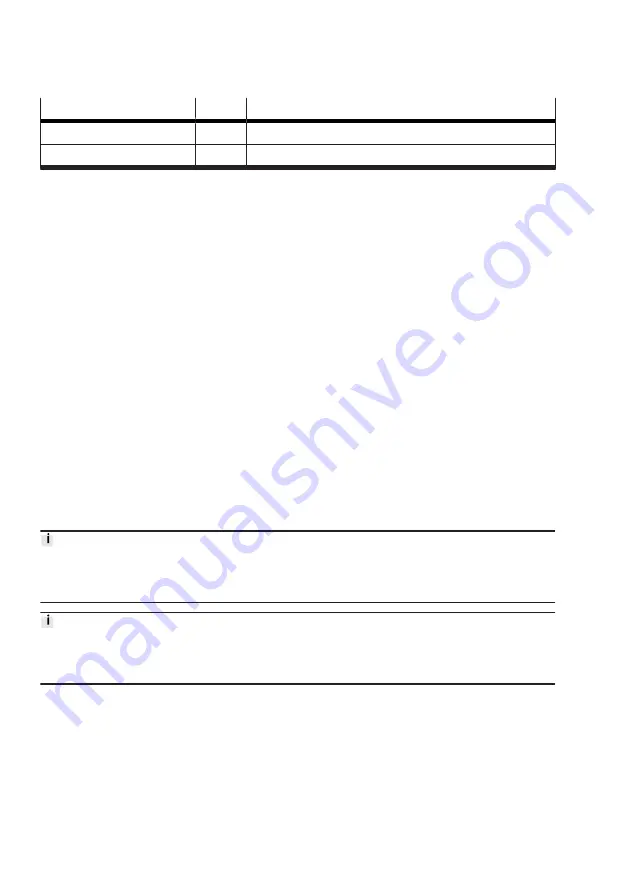
8
Festo — MS6(N)-SV-...-E-10V24 — 2021-11e
Product overview
Feature
Code
Type
UL certification
1)
– UL1
UL certification for Canada and USA
Alternative flow direction
1)
– Z
Flow direction from right to left
1) Optional
Tab. 2: Product overview
4.2
Function
The product is a safe, redundant mechatronic system in accordance with the requirements of EN ISO
13849-1+2. The safe venting pneumatic safety function is guaranteed even in the event of an fault in
the valve, e.g. due to wear or contamination. Through its electrical connection (NECA Sub-D multi-pin
plug socket, 9-pin), the product receives secure enable signals (EN1/EN2) from commercially-available
electronic or electromechanical safety relay units, which monitor the machine’s protective devices
(e.g. emergency stop, light curtain, electric door switch on the protective housing, etc.).
Automatic start/monitored start modes of operation
Two modes of operation are possible:
–
Automatic start (automatic reset)
The automatic start (automatic reset) mode of operation is preset with a bridge from terminal 5 to
terminal 6 in the multi-pin plug socket NECA (delivery status).
–
Monitored start (monitored reset)
The monitored start (monitored reset) mode of operation should be seen as a subordinate start
from the perspective of the complete system. The enable signal from the safety relay or the
controller always has priority.
In both modes of operation, the product can be electrically triggered using either static or dynamic
enable signals (EN1/EN2), depending on the NECA multi-pin plug socket.
The impulse generated by the start button must be within a time-frame of 0.1 s and 2 s.
If the start button is held down for too long or is locked down, the system identifies a cross circuit and
the product is placed in fault mode.
The start signal for S34 must not be generated until 1 s after the enable signals EN1/EN2 are created.
If the start signal is generated before or simultaneously with the enable signals, it will not be
recognised and must be generated again.
Summary of Contents for MS6 SV E 10V24 Series
Page 2: ...Translation of the original instructions...
Page 37: ......