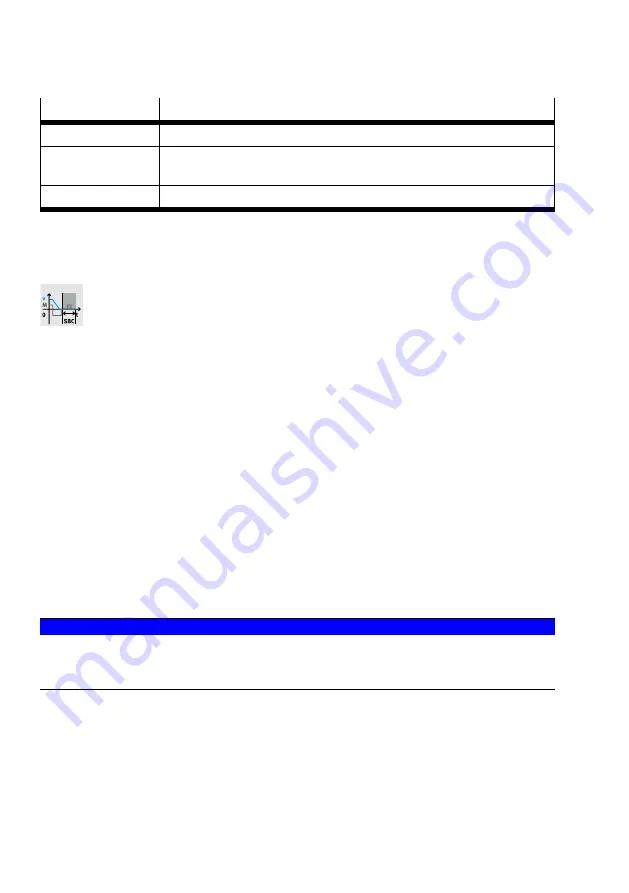
Term/abbreviation
Explanation
STA
Feedback, STO active
t
STA,Out
Max. delay for diagnostic feedback (≤ permissible reaction time when a
safety sub-function is requested
1)
+ 10 ms)
n
Rotational speed
1) See Technical data, safety reference data for STO
Tab. 3 Legend for STO timing
4.1.3
Safety sub-function SBC
Fig. 5 Symbol for SBC
The function described here implements the safety sub-function SBC according to EN 61800-5-2.
The safety sub-function SBC is used for controlling a holding brake in the motor and a clamping unit or
brake on the axis to slow an axis down mechanically or stop it safely.
Function and application of SBC
The safety sub-function SBC provides safe output signals for the control of brakes (holding brakes or
clamping units). The brakes are controlled on 2 channels by switching off the voltage at the following
outputs:
–
Safe output BR+/BR– [X6B] for the holding brake of the motor
–
Safe output BR-EXT/GND [X1C] for the external brake/clamping unit
The holding brake and/or clamping unit engage and slow the motor or axis. The purpose of this is to
slow down dangerous movements by mechanical means. The braking time is dependent on how
quickly the brake engages and how high the energy level is in the system.
The use of
just one brake
is only possible when performance requirements are low
è
Tab. 16 Safety reference data for the safety sub-function SBC. To do this, connect the brake either
to BR+/BR–
or
to BR-EXT.
NOTICE!
If there are suspended loads, they usually drop if SBC is requested simultaneously with STO. This can
be traced back to the mechanical inertia of the holding brake or clamping unit and is thus unavoid-
able. Check whether safety sub-function SS1 is better suited to your application.
SBC may only be used for holding brakes or clamping units which engage in the de-energised state.
Ensure the lines are installed in a protected manner.
Product overview
12
Festo — CMMT-AS-...-S1 — 2018-10a
Summary of Contents for CMTT-AS S1 Series
Page 45: ......